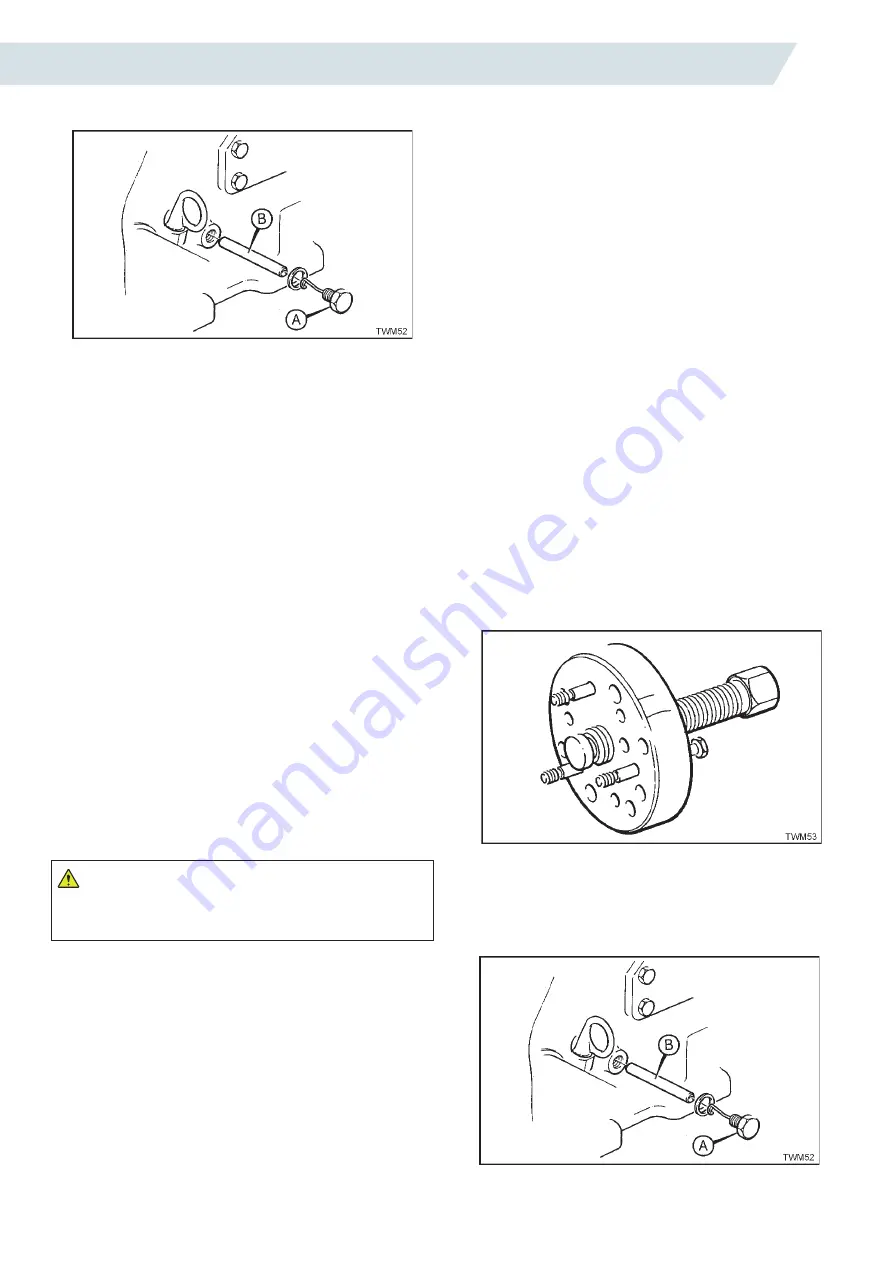
TS, TR, TX engines workshop manual
42
T SERIES ENGINES WORKSHOP MANUAL
45
CAUTION
If the sump has been removed, the procedure
detailed in "Replacing the Oil Sump" must
be followed when refitting the fanshroud to
prevent the possibility of distorting it resulting
in excessive flywheel to shroud run-out. This is
particularly important on Build 16 engines.
2.43 FLYWHEEL HOUSING - TX
Removing the Flywheel Housing
1.Remove the flywheel.
2.Remove the six self-locking setscrews.
3.Remove the fanshroud, noting that it is secured
to the sump by two bolts.
Refitting the Flywheel Housing
Refitting is carried out in the reverse order with the
self-locking setscrews torque loaded to 88.0Nm
(65.0lbf ft).
CAUTION
If the sump has been removed, the procedure
detailed in "Replacing the Oil Sump" must
be followed when refitting the fanshroud to
prevent the possibility of distorting it resulting
in excessive flywheel to shroud run-out.
2.43 MAIN BEARING HOUSING
The main bearing housing is secured to the
crankcase at the flywheel end and has an oil drain
which must be located towards the bottom of the
crankcase when the housing is refitted. Shims are
fitted between the housing and the crankcase to
maintain the crankshaft end float. An oil seal is
fitted to the centre bore of the housing and an '0'
ring is fitted in the side of the bearing housing to
provide a seal between the housing and bearing oil
feed drilling in the crankcase.
On engines fitted with battery charging equipment
the stator is secured to the main bearing housing
with screws.
If the crankshaft is moved towards the flywheel
end after the housing has been removed the thrust
washer at the gear end could become detached
from its recess. This can be avoided by removing
the gear end cover and placing two suitable thin
strips of metal between the crankshaft pinion and
the crankcase.
To prevent the thrust washer at the flywheel end
becoming detached from the main bearing housing
while removing the housing, turn the engine until
No. 1 cylinder piston is at the BDC position.
Removing the Main Bearing Housing
1.Remove the centre bearing locating dowel
securing screw (A) from the fuel pump side of the
engine.
CAUTION
Failure to remove the dowel may result in
distorting it making it difficult to remove at a
later stage.
2.Using a fuel pump securing bolt remove the
centre bearing dowel (B); leave the bolt in the
dowel until it is refitted to ensure the dowel is
fitted the correct way round.
Figure 2.43.1 Centre Bearing Dowel
3.Remove the bolts securing the main bearing
housing.
4.On early TS engines remove the charge winding
adaptor adapter.
5.Remove the bearing housing: if it is tight use
two M8 setscrews through the threaded holes
provided and jack it off.
6.Drift out the oil seal taking care not to damage
the bearings.
Refitting the Main Bearing Housing
When refitting the housing ensure that the oil
supply holes line up and the grooved bearing shell
is fitted at the top.
1.Lightly grease the steel back of the thrust washers
and position them in the housing, ensure they
are correctly located and the copper face will be
towards the crankshaft.
2.Remove the oil seal from the main bearing
housing.
3.Coat the bearing housing face with Loctite 221,
fit a shim and coat the outside face of the shim.
Continue adding and coating the remaining
shims.
4.Replace the housing and charge winding adaptor,
if fitted, and torque the bolts to 27.0Nm (20.0lbf ft).
5.Check the crankshaft endfloat.
Figure 2.43.1 Centre Bearing Dowel
3. Remove the bolts securing the main bearing housing.
4. On early TS engines remove the charge winding adaptor
adapter.
5. Remove the bearing housing: if it is tight use two M8 setscrews
through the threaded holes provided and jack it off.
6. Drift out the oil seal taking care not to damage the bearings.
Refitting the Main Bearing Housing
When refitting the housing ensure that the oil supply holes line
up and the grooved bearing shell is fitted at the top.
1. Lightly grease the steel back of the thrust washers and
position them in the housing, ensure they are correctly
located and the copper face will be towards the crankshaft.
2. Remove the oil seal from the main bearing housing.
3. Coat the bearing housing face with Loctite 221, fit a shim and
coat the outside face of the shim.
Continue adding and coating the remaining shims.
4. Replace the housing and charge winding adaptor, if fitted,
and torque the bolts to 27.0Nm (20.0lbf ft).
5. Check the crankshaft endfloat.
6. Replace the oil lip seal.
7. Replace the centre bearing locating dowel/s with the tapped
end facing outwards.
8. Replace the locating dowel securing screw and torque it to
20.5Nm (15.0lbf ft).
CAPTION
Striking the crankshaft may displace the thrustwashers
and damage the bearing locating dowel.
The Main Bearing Oil Lip Seal
1. Place the new seal squarely into the housing; do not use any
jointing compound.
2. Hold the oil seal tool onto the outside face of the seal and
using the oil seal tool, drive in the seal until the tool shoulder
is against the bearing housing.
2.44 The Crankshaft
The crankshaft is a steel forging and is carried in steel backed
copper faced main bearings which are located in the crankcase
at the gear end, the flywheel end and the central web/s of the
crankcase.
End thrust is taken on steel backed copper faced split thrust
washers fitted at the gear end of the crankcase and in the
flywheel end main bearing housing.
The main bearings are in two halves which are not
interchangeable; the top half has an oil groove and an oil hole
which must be correctly located.
An interference fit pinion is keyed onto the end of .the crankshaft
and engages with the camshaft gear.
Early crankshaft balance weights were secured with only one
retaining bolt up to the following engines:
35 00630 TS1
36 00255 TR1
35 06716 TS2
36 00073 TR2
35 05963 TS3
36 00112 TR3
After these and on all TX engines the weights were secured
by two capscrews; the later weights and capscrews are not
interchangeable with the original items.
Crankshaft Removal
1. Remove the cylinder barrels and pistons, main bearing
housing and the sump.
2. Using the Service Tool 393175 remove the crankshaft pinion.
T SERIES ENGINES WORKSHOP MANUAL
46
6.Replace the oil lip seal.
7.Replace the centre bearing locating dowel/s with
the tapped end facing outwards.
8.Replace the locating dowel securing screw and
torque it to 20.5Nm (15.0lbf ft).
CAUTION
Striking the crankshaft may displace the
thrustwashers and damage the bearing
locating dowel.
The Main Bearing Oil Lip Seal
1.Place the new seal squarely into the housing; do
not use any jointing compound.
2.Hold the oil seal tool onto the outside face of
the seal and using the oil seal tool, drive in the
seal until the tool shoulder is against the bearing
housing.
2.44 THE CRANKSHAFT
The crankshaft is a steel forging and is carried in
steel backed copper faced main bearings which
are located in the crankcase at the gear end,
the flywheel end and the central web/s of the
crankcase.
End thrust is taken on steel backed copper faced
split thrust washers fitted at the gear end of the
crankcase and in the flywheel end main bearing
housing.
The main bearings are in two halves which are not
interchangeable; the top half has an oil groove and
an oil hole which must be correctly located.
An interference fit pinion is keyed onto the end of
.the crankshaft and engages with the camshaft
gear.
Early crankshaft balance weights were secured
with only one retaining bolt up to the following
engines:
35 00630 TS1
36 00255 TR1
35 06716 TS2
36 00073 TR2
35 05963 TS3
36 00112 TR3
After these and on all TX engines the weights were
secured by two capscrews; the later weights and
capscrews are not interchangeable with the original
items.
Crankshaft Removal
1.Remove the cylinder barrels and pistons, main
bearing housing and the sump.
2.Using the Service Tool 393175 remove the
crankshaft pinion.
Figure 2.44.1 Crankshaft Gear Removal Tool
3.Remove the pinion gear Woodruff key if
necessary.
4.Remove each centre bearing locating dowels
securing screw (A).
Figure 2.44.2 Centre Bearing Dowel
5.Using a fuel pump securing bolt remove each
centre bearing dowel (B).
Leave the bolt in the dowel until it is refitted to
ensure the dowel is fitted the correct way round.
6.Remove the crankshaft balance weights.
7.Gently withdraw the crankshaft through the
flywheel end of the crankcase.
8.Remove the two socket screws and dismantle
the centre bearing housing/s.
9.Remove the gear end thrust washers.
Servicing the Crankshaft
a.Inspect the main bearings for scoring or wear.
If necessary, the bearings can be removed and
replaced using either Service Tool 393235 or
317-50006 as described in "02.47 Crankshaft
Main Bearings".
b.If the connecting rod big end has been dismantled
because of failure of the bearing, the oil passages
in the crankshaft must also be examined for
obstruction and fragments of metal.
c.Check the clearance between the crankshaft and
journals, the main bearings and crankpins and
Figure 2.44.1 Crankshaft Gear Removal Tool
3. Remove the pinion gear Woodruff key if necessary.
4. Remove each centre bearing locating dowels securing screw
(A).
T SERIES ENGINES WORKSHOP MANUAL
46
6.Replace the oil lip seal.
7.Replace the centre bearing locating dowel/s with
the tapped end facing outwards.
8.Replace the locating dowel securing screw and
torque it to 20.5Nm (15.0lbf ft).
CAUTION
Striking the crankshaft may displace the
thrustwashers and damage the bearing
locating dowel.
The Main Bearing Oil Lip Seal
1.Place the new seal squarely into the housing; do
not use any jointing compound.
2.Hold the oil seal tool onto the outside face of
the seal and using the oil seal tool, drive in the
seal until the tool shoulder is against the bearing
housing.
2.44 THE CRANKSHAFT
The crankshaft is a steel forging and is carried in
steel backed copper faced main bearings which
are located in the crankcase at the gear end,
the flywheel end and the central web/s of the
crankcase.
End thrust is taken on steel backed copper faced
split thrust washers fitted at the gear end of the
crankcase and in the flywheel end main bearing
housing.
The main bearings are in two halves which are not
interchangeable; the top half has an oil groove and
an oil hole which must be correctly located.
An interference fit pinion is keyed onto the end of
.the crankshaft and engages with the camshaft
gear.
Early crankshaft balance weights were secured
with only one retaining bolt up to the following
engines:
35 00630 TS1
36 00255 TR1
35 06716 TS2
36 00073 TR2
35 05963 TS3
36 00112 TR3
After these and on all TX engines the weights were
secured by two capscrews; the later weights and
capscrews are not interchangeable with the original
items.
Crankshaft Removal
1.Remove the cylinder barrels and pistons, main
bearing housing and the sump.
2.Using the Service Tool 393175 remove the
crankshaft pinion.
Figure 2.44.1 Crankshaft Gear Removal Tool
3.Remove the pinion gear Woodruff key if
necessary.
4.Remove each centre bearing locating dowels
securing screw (A).
Figure 2.44.2 Centre Bearing Dowel
5.Using a fuel pump securing bolt remove each
centre bearing dowel (B).
Leave the bolt in the dowel until it is refitted to
ensure the dowel is fitted the correct way round.
6.Remove the crankshaft balance weights.
7.Gently withdraw the crankshaft through the
flywheel end of the crankcase.
8.Remove the two socket screws and dismantle
the centre bearing housing/s.
9.Remove the gear end thrust washers.
Servicing the Crankshaft
a.Inspect the main bearings for scoring or wear.
If necessary, the bearings can be removed and
replaced using either Service Tool 393235 or
317-50006 as described in "02.47 Crankshaft
Main Bearings".
b.If the connecting rod big end has been dismantled
because of failure of the bearing, the oil passages
in the crankshaft must also be examined for
obstruction and fragments of metal.
c.Check the clearance between the crankshaft and
journals, the main bearings and crankpins and
Figure 2.44.2 Centre Bearing Dowel
Содержание TS/TR1
Страница 1: ...P027 08270 edition 8 April 2021 TS TR TX Engines Workshop Manual T SERIES ...
Страница 80: ...TS TR TX engines workshop manual 80 T SERIES ENGINES WORKSHOP MANUAL 90 ct ical Wiring i g ...
Страница 81: ...TS TR TX engines workshop manual 81 T SERIES ENGINES WORKSHOP MANUAL 91 Elect i al Wiring Diagram ...
Страница 82: ...TS TR TX engines workshop manual 82 T SERIES ENGINES WORKSHOP MANUAL 92 ctr ca Wi ing Diagrams ...
Страница 83: ...TS TR TX engines workshop manual 83 T SERIES ENGINES WORKSHOP MANUAL 93 Electrical Wiring iagram ...
Страница 84: ...TS TR TX engines workshop manual 84 T SERIES ENGINES WORKSHOP MANUAL 94 ect ica Wiring Diagrams ...
Страница 85: ...TS TR TX engines workshop manual 85 T SERIES ENGINES WORKSHOP MANUAL 95 ...
Страница 99: ...TS TR TX engines workshop manual 99 ...