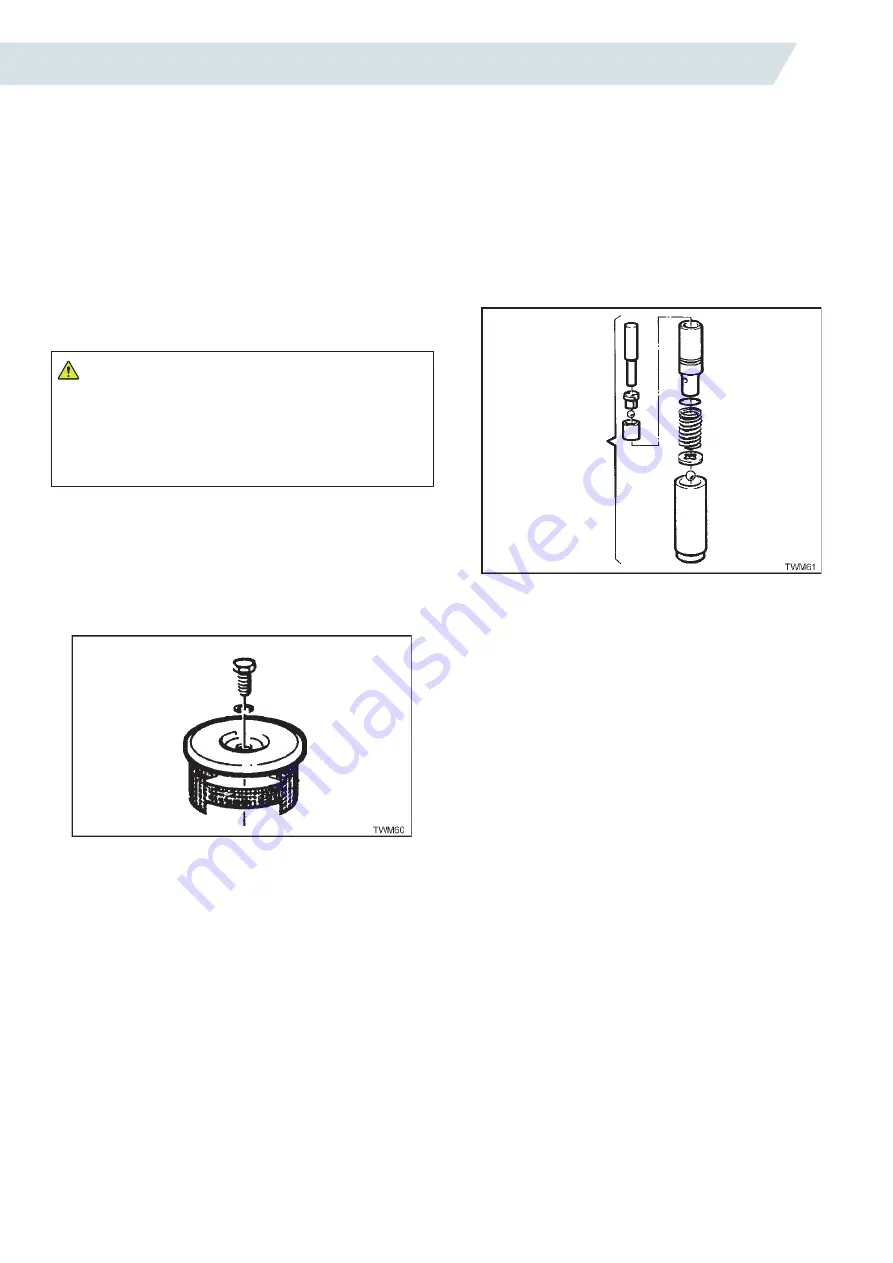
TS, TR, TX engines workshop manual
48
4. Replace and torque the remaining sump bolts to 27.0 Nm
(20.0 lbf ft).
5. Coat the threads of the drain plug with Hylomar PL32/M or
Three Bond 1110B and refit.
6. Return the engine to its normal position.
7. Fill the sump to the correct level with the correct grade and
type of lubricating oil.
8. Start the engine and run it for a few minutes to circulate the
oil and check the drain plug does not leak.
9. Stop the engine and allow time for the oil to settle and re-
check the level on the dipstick.
10. Add more oil if necessary.
CAPTION
If the procedure in items 2. and 4. is not correctly carried
out there is a possibility of distorting the fanshroud
resulting in excessive flywheel to fanshroud run-out. The
tolerances for bore and face run-out must be within 0.25
mm (0.010 in) TIR.
2.52 The Oil Strainer and Pump
The Oil Strainer
The engines are fitted with a coarse lubricating oil strainer on
the suction side of the oil pump; access to the strainer is gained
by removing the sump.
T SERIES ENGINES WORKSHOP MANUAL
52
Figure 2.51.1 Oil Filler and Drain
4.Clean and coat the threads of the drain plug with
Hylomar PL32/M or Three Bond 1110B.
5.Replace the drain plug taking care not to
overtighten it.
6.Fill the sump to the correct level with the correct
grade and type of lubricating oil.
7.Start the engine and run it for a few minutes to
circulate the oil and check the drain plug does
not leak.
8.Stop the engine and allow time for the oil to settle
and re-check the level on the dipstick.
9.Add more oil if necessary.
Oil Sump Capacity
litres
pints
US qts
TS/TR1
2.7
4.7
2.8
TS/TR/TX2
4.0
7.0
4.2
TS/TR/TX3
6.0
10.5
6.3
Removing the Sump
1.Remove the drain plug from the sump and drain
the oil into a suitable receptacle.
2.Remove the oil level dipstick.
A polypropylene handled dipstick is currently
fitted; refer to "02.50 The Oil Dipstick".
3.Stand the engine on its flywheel using a suitable
piece of wood or similar material on which to rest
the flywheel but not the fanshroud; this will enable
the engine to be rotated and ease subsequent
dismantling.
4.Remove the sump bolts and spring washers
noting that two bolts pass through the fanshroud
into the sump.
As the bolts are removed from the sump the oil
pump will move it away from the crankcase.
5.Remove the sump taking care not to damage the
oil pump.
Replacing the Oil Sump
1.Using a new joint, replace the sump with the
recess corner adjacent to the oil pump.
2.Replace the four long corner bolts finger tight.
3.Replace the two bolts through the fanshroud into
the sump and torque them to 43.5Nm (32.0lbf ft).
4.Replace and torque the remaining sump bolts to
27.0Nm (20.0lbf ft).
5.Coat the threads of the drain plug with Hylomar
PL32/M or Three Bond 1110B and refit.
6.Return the engine to its normal position.
7.Fill the sump to the correct level with the correct
grade and type of lubricating oil.
8.Start the engine and run it for a few minutes to
circulate the oil and check the drain plug does
not leak.
9.Stop the engine and allow time for the oil to settle
and re-check the level on the dipstick.
10.Add more oil if necessary.
CAUTION
If the procedure in items 2. and 4. is not correctly
carried out there is a possibility of distorting
the fanshroud resulting in excessive flywheel to
fanshroud run-out. The tolerances for bore and
face run-out must be within 0.25mm (0.010in) TIR.
2.52 THE OIL STRAINER AND PUMP
The Oil Strainer
The engines are fitted with a coarse lubricating oil
strainer on the suction side of the oil pump; access
to the strainer is gained by removing the sump.
Figure 2.52.1 Oil Strainer
Care must be taken to ensure that rags are not
used to wipe the inside of the crankcase during
overhauls to eliminate the possibility of fluff entering
the strainer and causing a restricted oil flow.
Note
- Early TS Engines:
On re-assembly take care to replace the
distance piece under the top plate and ensure
that the anti-surge plate on the strainer is
parallel to the crankcase web.
Figure 2.52.1 Oil Strainer
Care must be taken to ensure that rags are not used to wipe
the inside of the crankcase during overhauls to eliminate the
possibility of fluff entering the strainer and causing a restricted
oil flow.
Note - Early TS Engines:
On re-assembly take care to replace the distance piece under the top plate and ensure
that the anti-surge plate on the strainer is parallel to the crankcase web.
Oil Pump
The camshaft operated oil pumps are the self-regulating,
plunger type and they are not interchangeable across the
ranges.
Removing the Oil Pump
1. Drain the oil.
2. Remove the dipstick and sump.
3. Lift out the oil pump.
4. Using long nosed pliers remove the oil pump push rod from
the crankcase.
5. Dismantle the oil pump making a careful note of the
component positions and the two different sized ball
valves.
T SERIES ENGINES WORKSHOP MANUAL
53
Oil Pump
The camshaft operated oil pumps are the
self-regulating, plunger type and they are not
interchangeable across the ranges.
Removing the Oil Pump
1.Drain the oil.
2.Remove the dipstick and sump.
3.Lift out the oil pump.
4.Using long nosed pliers remove the oil pump
push rod from the crankcase.
5. Dismantle the oil pump making a careful note
of the component positions and the two different
sized ball valves.
Figure 2.52.2 The Oil Pump
Refitting the Oil Pump
1.Check that the oil pump is correctly assembled
as shown.
2.Check that the pump is working freely by
compressing it between the palms of the hands.
3.Replace the oil pump push rod with the larger
diameter towards the camshaft.
4.Replace the oil pump with the plunger end
towards the push rod.
5.Replace the sump, drain plug and the dipstick.
6.Refill the sump with oil.
2.53 THE OIL SEALS
Lip type seals are
fitted
to all TR and current TS
engines although two other types have been
fitted
to early TS engines:
Rotary type - very early TS2, 3.
Screw type - early TS2, 3.
A lip seal is
fitted
to the gear end cover with a
rotary, screw or lip type
fitted
in the
flywheel
end
main-bearing housing.
Lip Seals
Lip type seals will not seal if the shaft is scratched
or bruised within 5mm (0.20in) either side of the
path of the lip of the seal.
A
finely
and accurately ground shaft without chatter
marks and with a surface
finish
of 0.4 microns Ra
(16 micro inches CLA) maximum is advisable.
Emery cloth of any grade must not be used in
the area of the lip. Very
fine
scratches should be
corrected by polishing the working surface with a
wet mixture of metal polish and optical aluminium
oxide powder, failing this domestic scouring powder
may be used. Fold a strip of rag some 400mm long
by 50mm wide lengthwise into a 10mm belt and
wet it with the abrasive mixture, wrap the belt once
around the shaft and use it with a reciprocating
motion.
The End Cover Lip Seal
1.Remove the end cover and press out the old
seal.
2.Place a new seal into the outside neck of the end
cover, lip side
first,
and position it squarely on the
shoulder of the seal boss; do not use any jointing
compound.
3.Using the oil seal tool. 317-50065 press the seal
into position within the oil seal housing boss until
it is flush with the inside face of the boss.
In an emergency if the tool is not available a
suitable plug, preferably hard wood, can be
used.
The Main Bearing Housing Lip Seal
1.Remove the bearing housing and press out the
old seal.
2.Place the new seal squarely into the housing; do
not use any jointing compound.
3.Hold the oil seal tool, 317-50065, onto the outside
face of the seal and drive in the seal until the tool
shoulder is against the bearing housing.
In an emergency if the tool is not available a
suitable plug, preferably hard wood, can be
used.
The Rotary Oil Seal
If a rotary seal requires changing on a very early
engine it can be replaced by the current lip type.
The three components of the rotary seal are:
a.A rotating impeller which is an interference
fit
on
the crankshaft and has an oil sealing thread
machined on the outside diameter.
The seals used must be the approved type as
supplied by Lister Petter Power Systems and they
are fitted without any jointing compound being
applied.
Figure 2.52.2 The Oil Pump
Refitting the Oil Pump
1. Check that the oil pump is correctly assembled as shown.
2. Check that the pump is working freely by compressing it
between the palms of the hands.
3. Replace the oil pump push rod with the larger diameter
towards the camshaft.
4. Replace the oil pump with the plunger end towards the
push rod.
5. Replace the sump, drain plug and the dipstick.
6. Refill the sump with oil.
2.53 The Oil Seals
Lip type seals are fitted to all TR and current TS engines although
two other types have been fitted to early TS engines:
Rotary type - very early TS2, 3.
Screw type - early TS2, 3.
A lip seal is fitted to the gear end cover with a rotary, screw or
lip type fitted in the flywheel end main-bearing housing.
Lip Seals
Lip type seals will not seal if the shaft is scratched or bruised
within 5 mm (0.20 in) either side of the path of the lip of the
seal.
A finely and accurately ground shaft without chatter marks and
with a surface finish of 0.4 microns Ra (16 micro inches CLA)
maximum is advisable.
Emery cloth of any grade must not be used in the area of the
lip. Very fine scratches should be corrected by polishing the
working surface with a wet mixture of metal polish and optical
Содержание TS/TR1
Страница 1: ...P027 08270 edition 8 April 2021 TS TR TX Engines Workshop Manual T SERIES ...
Страница 80: ...TS TR TX engines workshop manual 80 T SERIES ENGINES WORKSHOP MANUAL 90 ct ical Wiring i g ...
Страница 81: ...TS TR TX engines workshop manual 81 T SERIES ENGINES WORKSHOP MANUAL 91 Elect i al Wiring Diagram ...
Страница 82: ...TS TR TX engines workshop manual 82 T SERIES ENGINES WORKSHOP MANUAL 92 ctr ca Wi ing Diagrams ...
Страница 83: ...TS TR TX engines workshop manual 83 T SERIES ENGINES WORKSHOP MANUAL 93 Electrical Wiring iagram ...
Страница 84: ...TS TR TX engines workshop manual 84 T SERIES ENGINES WORKSHOP MANUAL 94 ect ica Wiring Diagrams ...
Страница 85: ...TS TR TX engines workshop manual 85 T SERIES ENGINES WORKSHOP MANUAL 95 ...
Страница 99: ...TS TR TX engines workshop manual 99 ...