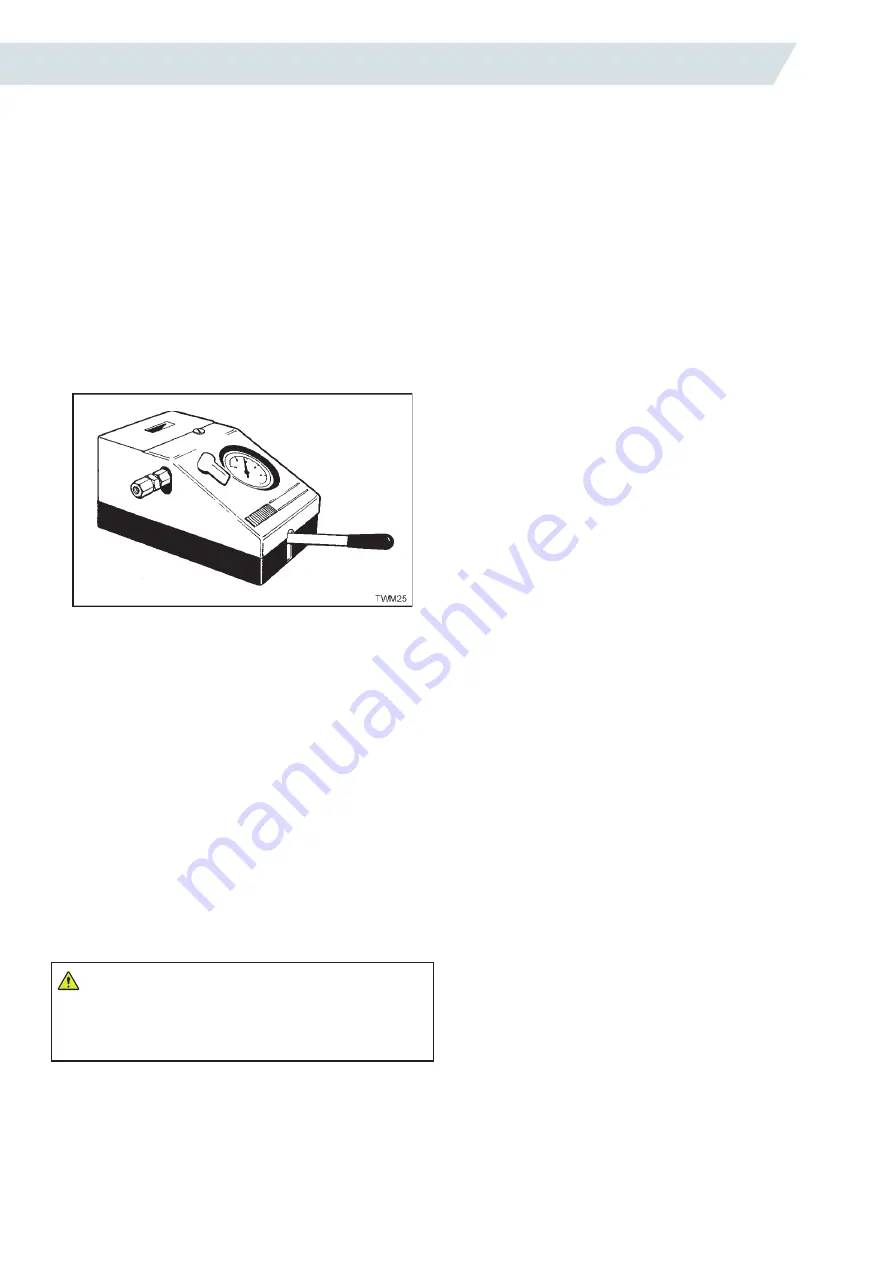
TS, TR, TX engines workshop manual
25
Cleaning an Injector
A thoroughly cleaned container holding a supply • of clean, fresh
fuel oil should be available for washing dismantled parts.
The components of each individual injector • should be kept
together at all times.
Never use paraffin or woven cloths; it is • permissible to use
non-fluffing paper during the cleaning process.
Components should be assembled wet.•
Setting the Injector
To ascertain if the injector is in good condition, it is removed
from the engine and connected to a fuel injector test rig, similar
to the one shown.
T SERIES ENGINES WORKSHOP MANUAL
27
6.Fit the slide hammer to the adapter and remove
the injector.
WARNING
Care must be taken to ensure that any part of
the hand is not likely to become trapped between
the two parts of the slide hammer while it is
being used.
Cleaning an Injector
A thoroughly cleaned container holding a supply
•
of clean, fresh fuel oil should be available for
washing dismantled parts.
The components of each individual injector
•
should be kept together at all times.
Never use paraffin or woven cloths; it is
•
permissible to use non-fluffing paper during the
cleaning process.
Components should be assembled wet.
•
Setting the Injector
To ascertain if the injector is in good condition, it is
removed from the engine and connected to a fuel
injector test rig, similar to the one shown.
Figure 2.26.3 Typical Injector Test Rig
If a rig is not available it becomes necessary to
replace the complete injector by a new or serviced
one which has a clean nozzle and has been
correctly set.
All sprays should have the same appearance and
the same length of penetration in the air. If one
spray is shorter or weaker than the others this
means that the corresponding hole is partially
blocked and best results will not be obtained. If one
hole is totally blocked or the nozzle dribbles it must
be replaced.
When a new nozzle is fitted the injector must be
reset on a test rig. After testing and resetting the
injector top plug must be torque loaded to 27.1 Nm
(20.0lbf ft).
Note:
Injector setting pressures can be found
in 'Technical Data" in the relevant engine
section.
WARNING
Under no circumstances allow unprotected skin
to come into contact with the spray as the fuel
may enter the blood stream with fatal results.
Injector Back Pressure
The leak-off rate is 6-27 seconds between 172-
142bars (170-140atmos) on an injector tester using
Calibration C fluid, at a temperature of 15.5°C
(60°F).
Replacing an Injector
If the injector sealing washer has been used more
than once it will become compressed and may
adversely affect combustion. Care should be taken
to ensure two washers are not fitted.
1.Examine the oil seal ring for damage or cuts,
replace if necessary.
2.Ensure the injector sealing washer has been
removed and the seating in the cylinder head is
clean and smooth.
3.Lightly smear a very small amount of high melting
point grease to one side of a new injector sealing
washer and place it over the injector nozzle,
greased side first.
4.Replace the leak-off pipe to the injector.
5.Fit the injector into the cylinder head.
TS/TR Engines:
6.Replace the clamp and leave the Alien screw
finger tight.
7.Replace the fuel pump to injector pipe - do not
tighten.
8.Replace the leak-off pipe into the fuel tank.
9.Torque the clamp screw to 21.0Nm(15.5lbf ft).
10.Torque all fuel pipe nuts to 28.5Nm (21.0lbf
ft) and the leak-off pipe swivel union to 4.0Nm
(3.0lbf ft).
11.Replace the cylinder head covers.
12.After the initial run following an injector
replacement re-torque the injector clamp screw.
TX Engines:
13.Replace the clamp and leave the nuts finger
tight.
14.Replace the fuel pump to injector pipe - do not
tighten.
15.Push the leak-off pipe onto the injector.
16.Torque the clamp screw to 8.0Nm (6.0Ibf ft).
17.Torque all fuel pipe nuts to 28.5Nm (21.0lbf ft).
18.Replace the leak-off pipe into the fuel tank.
Figure 2.26.3 Typical Injector Test Rig
If a rig is not available it becomes necessary to replace the
complete injector by a new or serviced one which has a clean
nozzle and has been correctly set.
All sprays should have the same appearance and the same
length of penetration in the air. If one spray is shorter or
weaker than the others this means that the corresponding
hole is partially blocked and best results will not be obtained.
If one hole is totally blocked or the nozzle dribbles it must be
replaced.
When a new nozzle is fitted the injector must be reset on a test
rig. After testing and resetting the injector top plug must be
torque loaded to 27.1 Nm (20.0lbf ft).
Note:
Injector setting pressures can be found in 'Technical Data" in the relevant engine
section.
WARNING
Under no circumstances allow unprotected skin to come
into contact with the spray as the fuel may enter the
blood stream with fatal results.
Injector Back Pressure
The leak-off rate is 6-27 seconds between 172-142bars (170-
140atmos) on an injector tester using Calibration C fluid, at a
temperature of 15.5°C (60°F).
Replacing an Injector
If the injector sealing washer has been used more than
once it will become compressed and may adversely affect
combustion. Care should be taken to ensure two washers
are not fitted.
1. Examine the oil seal ring for damage or cuts, replace if
necessary.
2. Ensure the injector sealing washer has been removed and the
seating in the cylinder head is clean and smooth.
3. Lightly smear a very small amount of high melting point
grease to one side of a new injector sealing washer and place
it over the injector nozzle, greased side first.
4. Replace the leak-off pipe to the injector.
5. Fit the injector into the cylinder head.
TS/TR Engines
6. Replace the clamp and leave the Alien screw finger tight.
7. Replace the fuel pump to injector pipe - do not tighten.
8. Replace the leak-off pipe into the fuel tank.
9. Torque the clamp screw to 21.0Nm(15.5lbf ft).
10. Torque all fuel pipe nuts to 28.5Nm (21.0lbf ft) and the leak-
off pipe swivel union to 4.0Nm (3.0lbf ft).
11. Replace the cylinder head covers.
12. After the initial run following an injector replacement re-
torque the injector clamp screw.
TX Engines
13. Replace the clamp and leave the nuts finger tight.
14. Replace the fuel pump to injector pipe - do not tighten.
15. Push the leak-off pipe onto the injector.
16. Torque the clamp screw to 8.0Nm (6.0Ibf ft).
17. Torque all fuel pipe nuts to 28.5Nm (21.0lbf ft).
18. Replace the leak-off pipe into the fuel tank.
2.27 The Fuel Pump
The individual fuel pumps are located at the side of the engine
between the push rods and are secured to the crankcase by two
bolts. Early TS engines were fitted with a long headed bolt fitted
to the inside hole in the pump mounting flange.
Removing the Fuel Pumps
1. Drain the fuel tank or isolate the fuel supply.
2. Disconnect the fuel feed pipes at the pumps.
3. Remove the fuel pipes from the pumps to injectors taking care
to hold the fuel pump delivery valve holder with a spanner
to prevent it turning.
4. Remove the fuel pump inspection doors.
5. Release the spring tension of the speeder spring by
unscrewing the speed adjusting screws on the side of the
crankcase.
6. Using long nose pliers disconnect the speeder spring from
its spigot.
It may be necessary to turn the spigot until the hole axis is
parallel to the camshaft before removing the spring.
7. Disconnect the governor and pump interconnecting linkage
at the pumps.
Содержание TS/TR1
Страница 1: ...P027 08270 edition 8 April 2021 TS TR TX Engines Workshop Manual T SERIES ...
Страница 80: ...TS TR TX engines workshop manual 80 T SERIES ENGINES WORKSHOP MANUAL 90 ct ical Wiring i g ...
Страница 81: ...TS TR TX engines workshop manual 81 T SERIES ENGINES WORKSHOP MANUAL 91 Elect i al Wiring Diagram ...
Страница 82: ...TS TR TX engines workshop manual 82 T SERIES ENGINES WORKSHOP MANUAL 92 ctr ca Wi ing Diagrams ...
Страница 83: ...TS TR TX engines workshop manual 83 T SERIES ENGINES WORKSHOP MANUAL 93 Electrical Wiring iagram ...
Страница 84: ...TS TR TX engines workshop manual 84 T SERIES ENGINES WORKSHOP MANUAL 94 ect ica Wiring Diagrams ...
Страница 85: ...TS TR TX engines workshop manual 85 T SERIES ENGINES WORKSHOP MANUAL 95 ...
Страница 99: ...TS TR TX engines workshop manual 99 ...