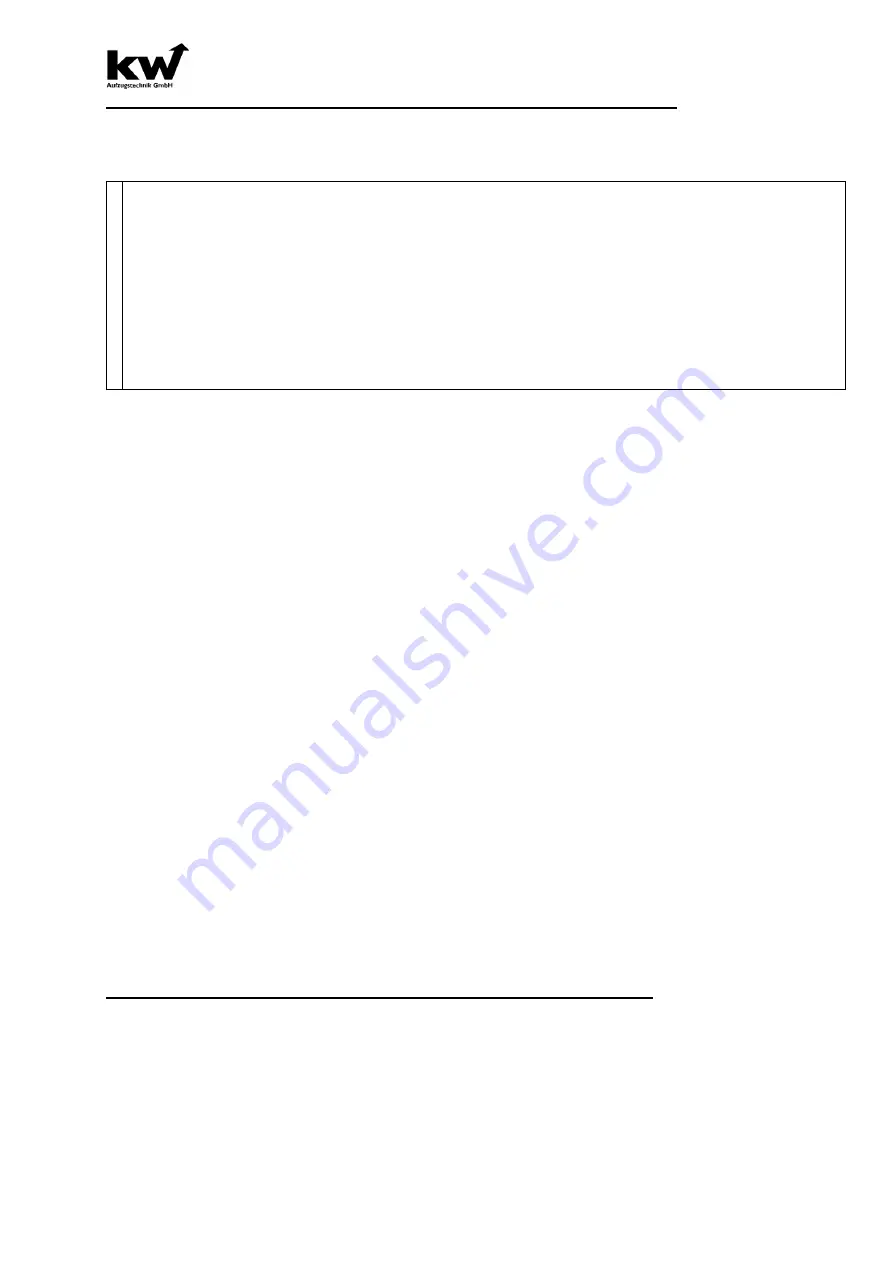
KW Aufzugstechnik GmbH Inbetriebnahme DAVID-613
DAVID-D613-Inbetriebnahme-V124-EE 18.02.2022 Seite - 81 -
4.16 Carrying out simulation- leaving the door zone with the door open EN81-20
In the submenu C416 Test UCM zone drive of the processor system DAVID-613 it is possible to simu-
late leaving the door zone with the door open according to EN 81-20/50 by switching on the return
control and the function UCM zone drive.
To initiate the journey from the zone, note the following:
1.) Stopping the elevator car flush with the bottom landing (top stop) .
2.) Turning the Return Motion Drive -> Close the doors.
3.) Function “UCM-zone drive” in the TÜV Menue-C416 activate
4.) Return Motion Drive UP (DOWN), until the security circuit SIS16-101 interrupt.
5.) Open the shaft door and measure the stopping distance.
6.) Close the shaft door
7.) In the C0 RESET menu error „F60 A3-case“ reset
8.) Cabin with Return Motion Drive downwards (top down) drive.
9.) Return Motion Drive off -> door opens -> normal operation
10.) Repeated process for the top stop on your way down zone -> () note entries!
General
According to the new standard EN 81-1:1998 + A3: 2009 resp. EN 81-2:1998 + A3: 2009 “protection of unintended
car movement away from the landing with the landing door not in the locked position and the car door not in the
closed position” the car must leave the door zone and must come to a halt within the legal stopping distance.
As a worst-case scenario here, the “Motor-driven exit” door opener in the zone with acceleration values of the
normal operation is considered.
Basically, the simulation of the process never done with an open door!
To facilitate this, a separation in the control terminal,is availabel a Relay “K69”, the safety circuit of the door lock of
SIS16-101 / feedforward separates drive contactors in the simulation case. In order to allow the elevator to the start
of the journey, is a software function in TüV menu of the control computer of the series D613, D912 and D2005
activates the security circuit for a drive, so that the drive and braking elements contactors are energized until they
leave the zone.
After leaving the zone, the drive is disconnected and so the car comes to a stop. You can now open
the landing door with the emergency release and determine the stopping distance, based on the hatch door to the
cabin doorway clamp.
Experation
The elevator car is parked in the lowest landing floor and turned on the Return Motion Drive. This will be the landing
and car door closed and a Call input over indoor and outdoor control is suppressed.
Please listen in with the local intercom in the cabin, if there are people in it. You can take the handheld terminal
HPG-60 in the control computer to the TÜV menu 416
th
UCM-zone drive. The
UCM-
zone
drive
is
set to ON
.
Now
you can start with the Return Motion Drive Switch UP holt the drive, which ends when you leave the zone. Auto-
matically increase the speed to rated speed and the acceleration was increased to 100% (in conjunction with
GOLIATH inverter).
The stopping distance is displayed in mm on the display. The system is locked with the error “F60 A3-case”. Op-
tionally, you can open the Landing door chess with the emergency release and measure the stopping distance
(Chess doorway to the cabin door threshold).
After re-closing the landing door and turning off the safety circuit fuse F7
.
Before switching on the safety fuse F7 in
the circuit,
C0 RESET menu
must be reset the A3 error then you can drive with the Return Motion Drive Switch
DOWN, the elevator car in the lowest station.
Repetition
The same process must now be repeated for the top stop. Therefore, the elevator car at the top station
is placed flush with the zone and performs way down.
4.17 Execution simulation- failure of the brake element according to EN81-20
In the
submenu C417 Test brake element
of the DAVID-613 processor system, it is possible to
switch off the monitoring of the brake element 1 or 2 or 3 for the purpose of software, in order to gen-
erate an error reaction. This corresponds to a physical interruption of the line of the respective brake
element. This is required for brake components requiring monitoring, in order to simulate a failure of a
brake element according to EN 81-20