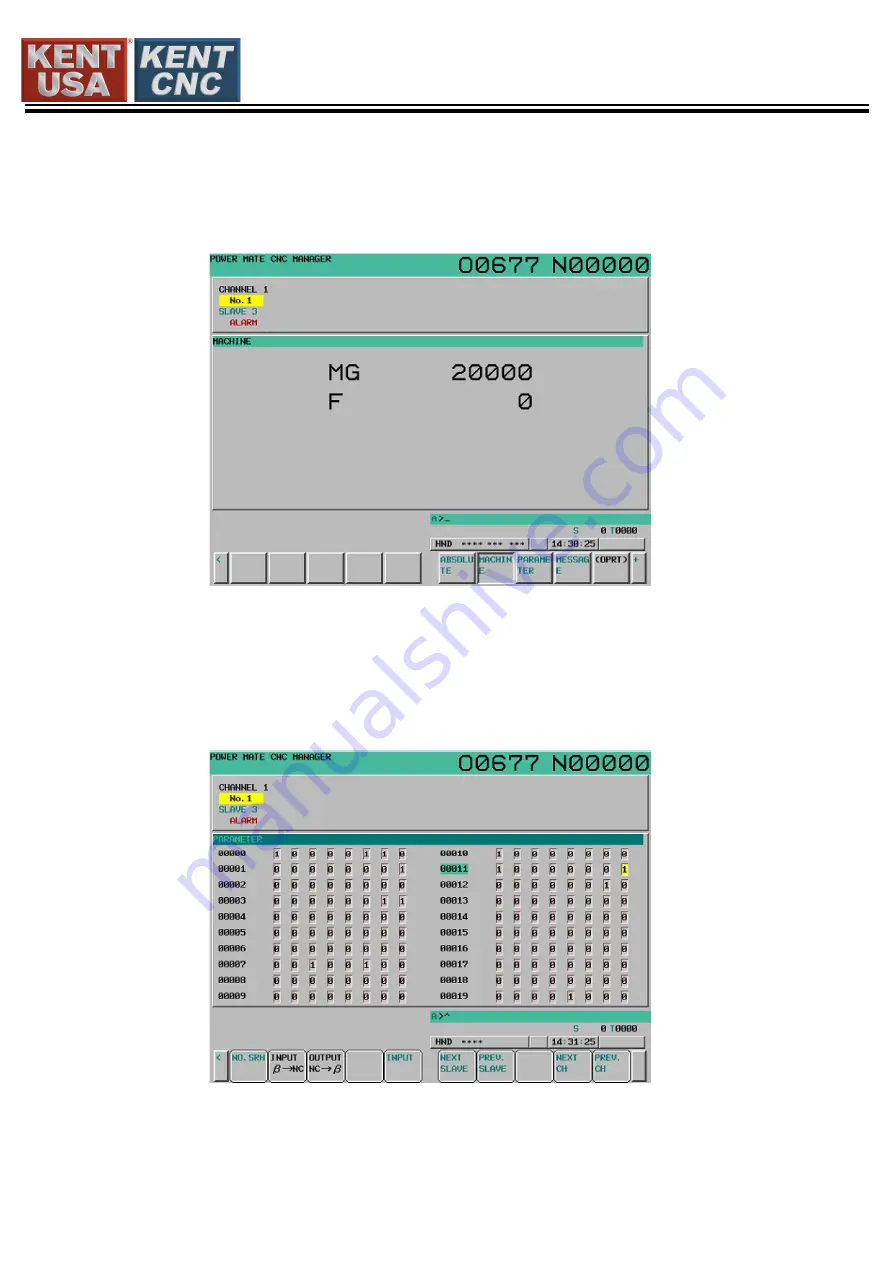
R AD AR
66
In Manual mode, push door and manual key
(5)
Push MAG C.W. key
(6)
Move NO. 1 position
(8)
Setting 0011 # 0 to 1
(9)
MG change display number
(7)
Power off, and power on
(10)
Figure 5.26
5.
Adjustment
5.
Adjustment
5.
Adjustment
5.
Adjustment
5.
Adjustment
5.
Adjustment
5.
Adjustment
5.
Adjustment
Figure 5.27
Property
of
Kent
Industrial
USA
Do
Not
Reproduce