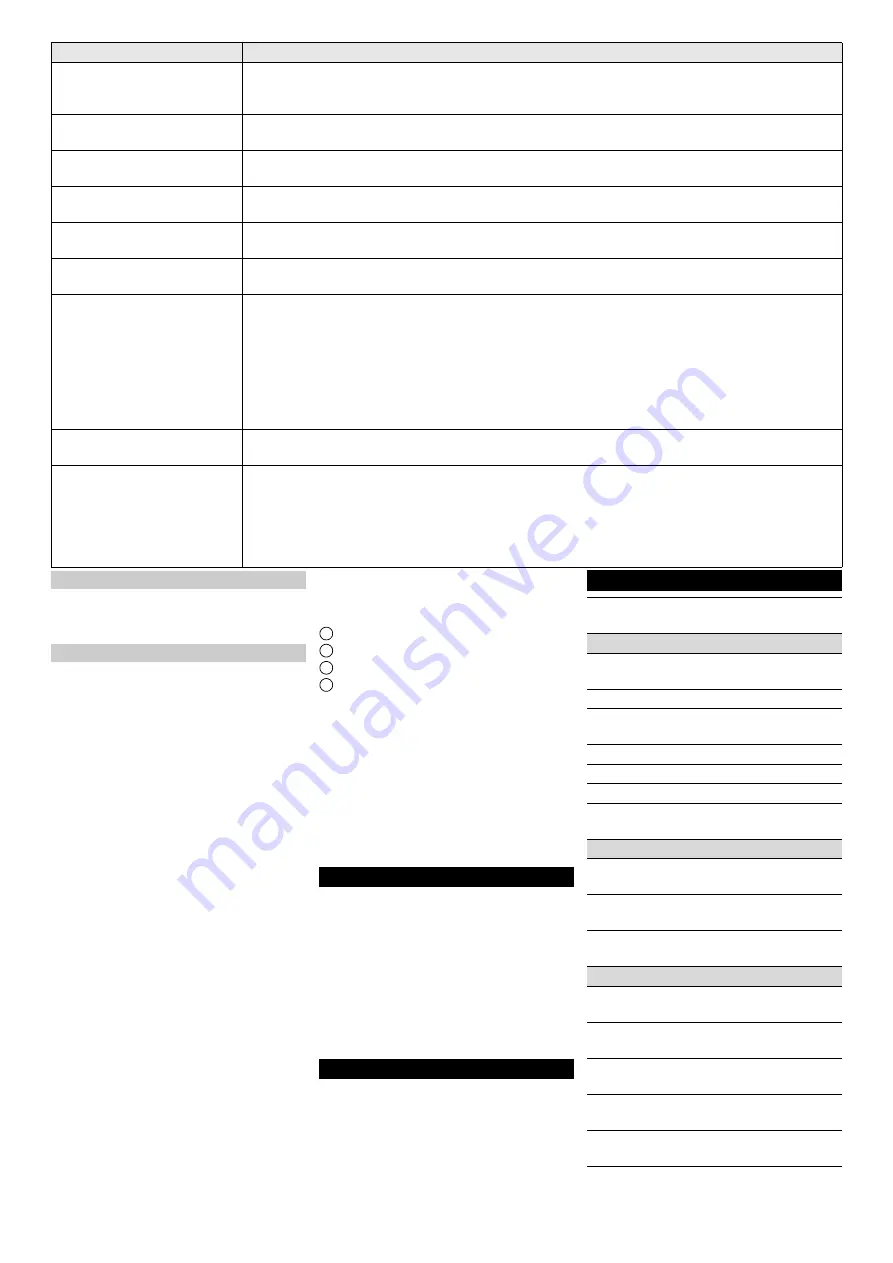
English
17
Performing a reset
1. Press the reset button inside the device
with a screwdriver.
Illustration O
Replacing the carbon dioxide filter
ATTENTION
Malfunctions
Contaminated carbon dioxide can cause
malfunctions.
When working on the carbon dioxide filter,
be careful not to get any dirt into the device.
ATTENTION
Malfunctions
Malfunctions due to contamination.
After each loosening or unscrewing of the
screw plug, the carbon dioxide filter and the
copper seal must be replaced. If this is not
done, particles can become detached from
the carbon dioxide filter and lead to mal-
functions.
Note
The carbon dioxide filter is backwashed
and cleaned as soon as the pressurised
cylinder connection is disconnected from
the carbon dioxide cylinder. Regular re-
placement of the carbon dioxide filter is
therefore not necessary.
1. Close the stop valve on the carbon diox-
ide bottle.
2. Operate the unit at the highest level for
about 1 minute to depressurise the car-
bon dioxide hose.
3. Unscrew the screw flange on the carbon
dioxide bottle.
4. Carefully unscrew the screw plug from
the screw flange. Let the hose flange
hang down to prevent dirt from entering
the carbon dioxide hose.
Illustration P
1
Screw flange
2
Carbon dioxide filter
3
Copper sealing ring
4
Screw plug
5. Remove the carbon dioxide filter.
6. Vacuum out the screw plug and the
screw flange.
7. Carefully press the new carbon dioxide
filter onto the screw plug by hand.
8. Replace the copper seal.
9. Tighten the screw plug, holding the wide
hexagon of the screw flange with an
open-end wrench.
Tightening torque: 80 Nm.
Warranty
The warranty conditions issued by our rele-
vant sales company apply in all countries.
We shall remedy possible malfunctions on
your appliance within the warranty period
free of cost, provided that a material or
manufacturing defect is the cause. In a war-
ranty case, please contact your dealer (with
the purchase receipt) or the next author-
ised customer service site.
(See overleaf for the address)
Accessories
ABS residual pressure valve
Order number 2.574-006.0
Necessary when using carbon dioxide bot-
tles with a residual pressure valve.
Technical data
The pellet production fault in-
dicator lights up
Allow the device to thaw out. Check the carbon dioxide filter and change it if necessary. Then per-
form a reset.
If the malfunction occurs repeatedly, replace the carbon dioxide bottle.
The pellet metering fault indi-
cator lights up
Switch the device off and back on again.
If the fault indicator remains lit, contact the customer service.
The pellet metering fault indi-
cator flashes
Allow the metering motor to cool down. Position the device so that air can flow into the device from
below. Contact Customer Service if necessary.
The voltage supply indicator
light does not light up
Plug the mains plug into the socket.
Check the on-site voltage supply.
The compressed air indicator
light does not light up
Connect a compressed air hose to the device.
Open the stop valve in the on-site compressed air supply.
The device does not work
Check the indicator lights and fault indicators.
Perform a reset.
Poor cleaning performance
Turn the program switch to a higher level.
Increase the jet pressure.
Check the filling level of the carbon dioxide bottle.
Do not use a heated carbon dioxide bottle. Protect the carbon dioxide bottle from heat radiation.
The effectiveness of the pellet production drops sharply if the temperature of the carbon dioxide is
above 31 °C.
Allow the abrasive hose and the jet gun to thaw to clear any blockages. Then increase the jet pres-
sure.
Pellet dosage too low
Turn the program switch to a higher level.
Replace the carbon dioxide filter between the carbon dioxide bottle and the device.
Recurring interruptions in the
dry ice stream
Turn the programme switch to a lower level or increase the jet pressure.
If the jet nozzle is clogged:
a Immediately close the carbon dioxide bottle.
b Allow the unit to thaw for 30 minutes.
c Increase the jet pressure.
d Start the appliance with the carbon dioxide bottle closed to remove pellet residues.
Fault
Rectification
IB 10/
8 L2P
Electrical connection
Mains voltage
V
220...
230
Phase
~
1
Frequency
Hz
50...6
0
Power rating
kW
1,0
Degree of protection
IPX4
Leakage current, typical
mA
<3,5
Residual current device
delta I,
A
0,03
Compressed air connection
Compressed air hose,
nominal width (min.)
Inches 0,5
Pressure (max.)
MPa
(bar)
1,0
(10)
Compressed air consump-
tion, max.
m
3
/
min
0,8
Device performance data
Jet pressure, max.
MPa
(bar)
1,0
(10)
Jet pressure, min. level 1 MPa
(bar)
0,07
(0,7)
Jet pressure, min. level 2 MPa
(bar)
0,14
(1,4)
Jet pressure, min. level 3 MPa
(bar)
0,28
(2,8)
Carbon dioxide consump-
tion
kg/h
20...6
0
Содержание IB 10/8 L2P
Страница 2: ...A...
Страница 3: ...B C D E F G H I J K L M N O P...
Страница 85: ...85 300 m 3 5 7 10 K RCHER 79 C EN 511 Pellet...
Страница 90: ...90 K RCHER 1 2 100 1 500 1 2 1 2 DGUV R 100 500 1 1 1 N 1 2 3 4 K rcher...
Страница 100: ...100 10 300 3 5 7 10 K RCHER 79 C EN 511...
Страница 105: ...105 L 1 2 3 4 10 11 12 13 1 2 3 4 2 5 M K RCHER 1 2 100 1 500 1 2 1 2 DGUV R 100 500 1 1 1...
Страница 106: ...106 N 1 2 3 4 K rcher 1 O 31 C a b 30 c d...
Страница 166: ...166 K RCHER CO2 2 5 99 5 H2O 250 ppm NVOC 2 ppm 79 C 700 REACH www kaercher com REACH 10 300 m 3 5 7 10 K RCHER 79 C...
Страница 172: ...172 K RCHER 1 2 100 1 500 1 2 1 2 DGUV R 100 500 1 1 1 N 1 2 3 4 K rcher...
Страница 173: ...173 1 O 1 2 1 3 4 P 1 2 3 4 5 6 7 8 9 80 Nm ABS 2 574 006 0 31 C a b 30 c d...
Страница 196: ...196 REACH www kaercher com REACH 10 300 3 5 7 10 K RCHER 79 EN 511...
Страница 201: ...201 12 13 1 2 3 4 2 5 M K RCHER 1 2 100 1 500 1 2 1 2 DGUV R 100 500 1 1 1 N 1 2 3 4...
Страница 202: ...202 K rcher 1 O 1 2 1 3 4 P 1 2 3 4 5 6 31 C a b 30 c d...
Страница 210: ...213 12 13 1 2 3 4 5 M K RCHER 1 2 100 1 500 1 1 2 DGUV R 100 500 1 1 1 N 1 2 3 4 K rcher...
Страница 215: ......