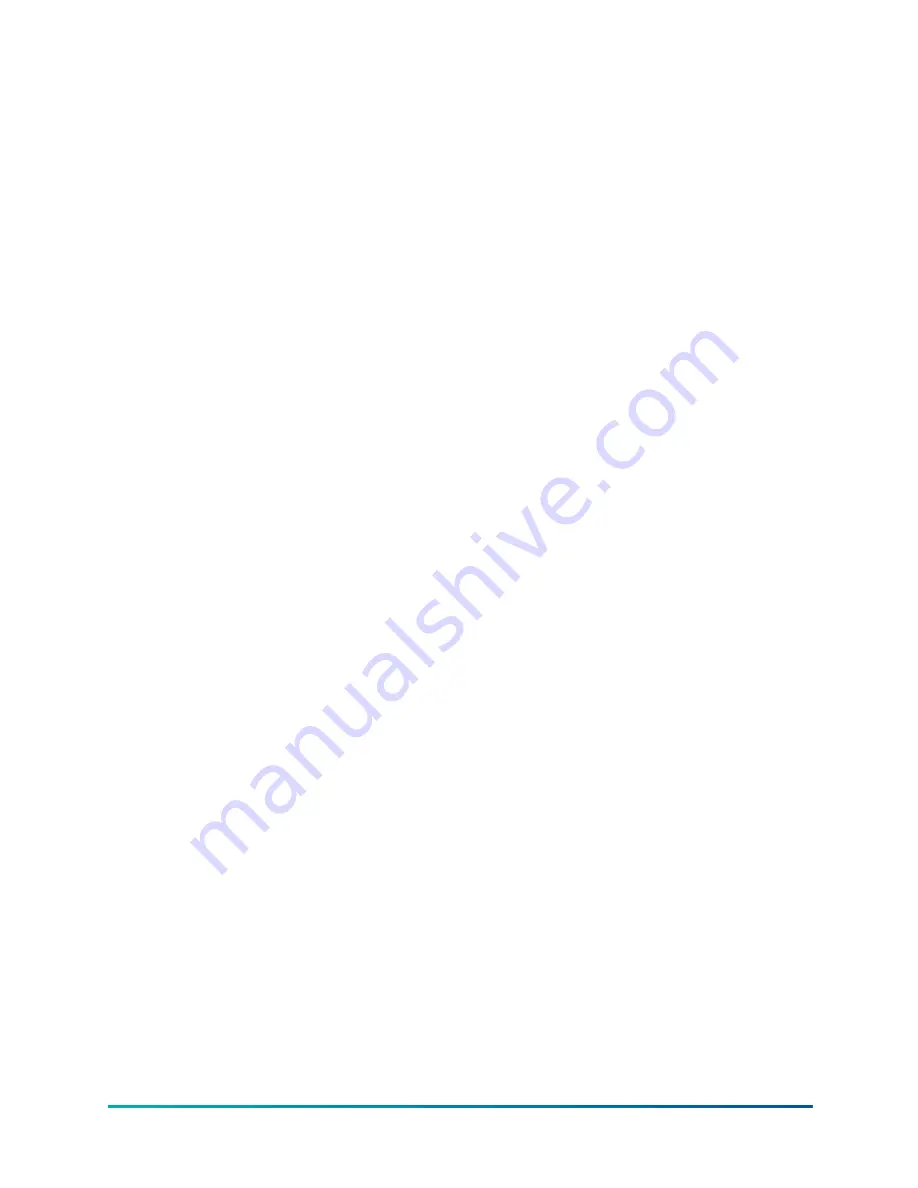
Annually
Perform the following checks annually or more often, if necessary:
1. Evaporator and condenser:
a. Inspect and clean the water strainers.
b. Inspect and clean the tubes as required.
c. Inspect the end sheet.
2. Condenser:
a. Inspect and clean the coil sections as required.
b. Inspect the condenser fans for correct operation.
3. Compressor drive motor:
- Measure the motor winding insulation resistance.
4. Check all enclosure door gaskets for any signs of leakage or damage that might cause a leak.
This should include the VGD actuator shaft bellows.
5. Replace all vapor emitters in the variable speed drive and any other locations where they are
present.
6. Inspect and service the electrical components as necessary.
7. Perform refrigerant analysis.
8. Verify the unit heater operation.
Checking system for leaks
Leak testing
The refrigerant side of the system is carefully pressure tested and evacuated at the factory.
After the system has been charged, the system must be carefully leak tested with a refrigerant-
compatible leak detector to ensure that all joints are tight. The acceptable limit for a 100% pure
R-134a system is 0.1 oz/year at DWP.
If any leaks are indicated, they must be repaired immediately. At times, leaks can be stopped by
ensuring that face seal nuts and flange bolts are correctly torqued. However, for any major repair,
the refrigerant charge must be removed and the system leak checked using reliable methods like a
pressure test.
See
Removing the refrigerant charge for service
.
Leak testing during operation
After the system has been charged, the system must be carefully leak tested with a compatible leak
detector to ensure that all joints are tight. The acceptable limit for a 100% pure R-134a system is 0.1
oz/year at DWP.
If any leaks are indicated, they must be repaired immediately. Usually, leaks can be stopped by
tightening the O-ring face seal (ORFS) fitting, flare nuts, or flange bolts. However, for any major
repair, the refrigerant charge must be removed.
Vapor connection locations
To be able to correctly evacuate, leak test, and charge the YVAM system, the three vapor
connections must be aligned correctly to conduct a proper system service. See Figure 50 for these
locations.
123
YVAM Control Center
Содержание YORK YVAM 0350
Страница 2: ...2 YVAM Control Center...
Страница 10: ...Figure 4 Variable speed drive nomenclature YVAM Control Center 10...
Страница 15: ...Figure 8 System piping and instrumentation diagram P ID 15 YVAM Control Center...
Страница 118: ...Figure 47 Drive logic board Callout Component Callout Component A U35 B U38 C U37 D U36 YVAM Control Center 118...
Страница 154: ...Figure 62 Sample printout status or history YVAM Control Center 154...
Страница 155: ...Figure 63 Sample printout status or history continued 155 YVAM Control Center...
Страница 156: ...Figure 64 Sample printout setpoints YVAM Control Center 156...
Страница 157: ...Figure 65 Sample printout setpoints continued 157 YVAM Control Center...
Страница 158: ...Figure 66 Sample printout schedule YVAM Control Center 158...
Страница 159: ...Figure 67 Sample printout sales order 159 YVAM Control Center...
Страница 160: ...Figure 68 Sample printout security log report YVAM Control Center 160...