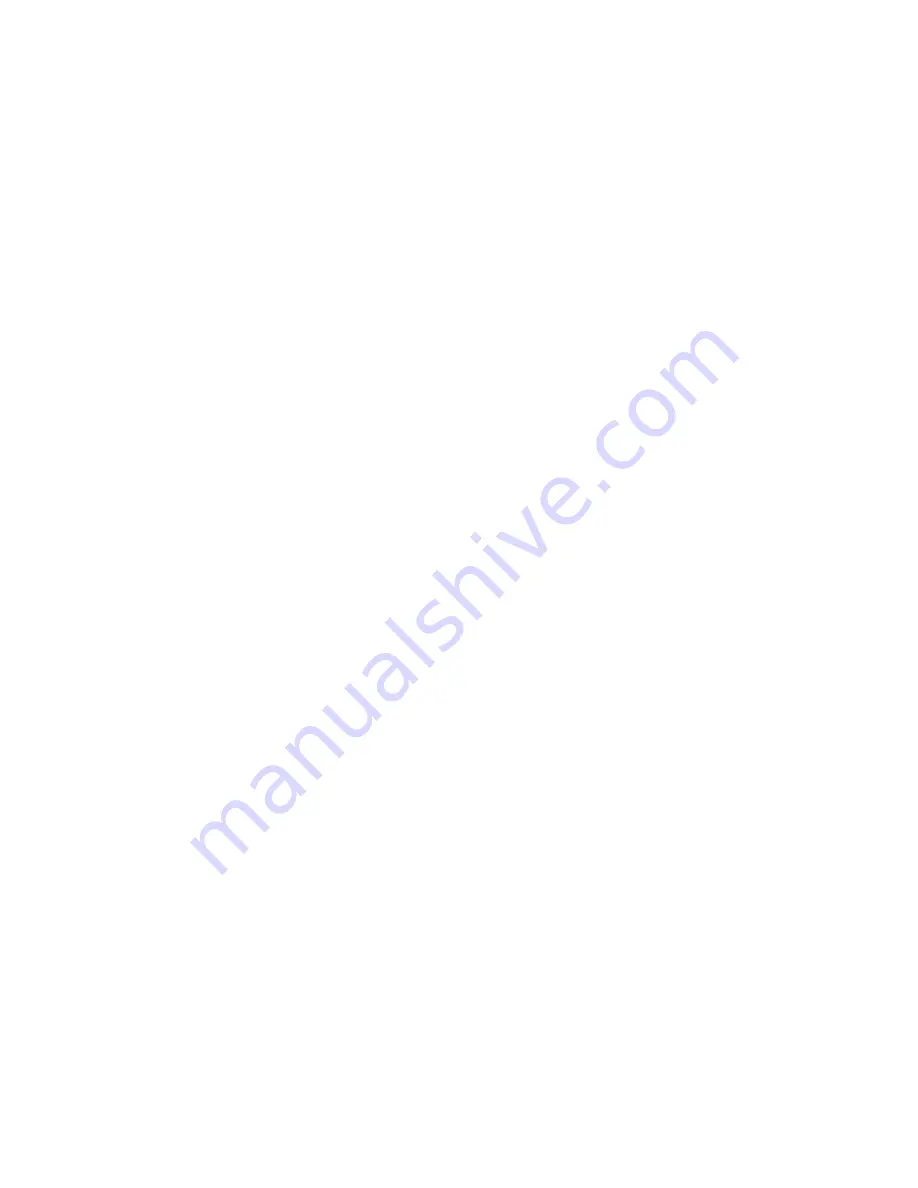
JOHNSON CONTROLS
3
FORM 160.10-O1
ISSUE DATE: 4/27/2018
EMERGENCY SHUTDOWN
In case an emergency of any type should arise while
the chiller is running, IMMEDIATELY switch the Op-
tiView compressor switch to the OFF position.
RESPONSIBILITY FOR SAFETY
Every effort has been made in the design and manufac-
ture of this kit to ensure the safety of personnel work-
ing on the chiller. However, the individual operating/
working on any equipment is ultimately responsible
for:
• Personal safety, the safety of other personnel, and
the machinery
• Correct utilization of the machinery in accordance
with the procedures detailed in the YORK and
Trane manuals
• Proper chiller maintenance
ABOUT THIS MANUAL
The contents of this manual include suggested best
working practices and procedures related to the service
and repair of this kit. These are issued for guidance
only; they do not take precedence over the above stated
individual responsibility and local safety regulation.
For information related directly to the chiller shells,
compressor and other components, refer to the specific
manual provided by the manufacturer of the chiller.
PROPER EQUIPMENT HANDLING
Proper Lock-Out / Tag-Out
To ensure safety, notify proper personnel of chiller
shutdown and then proceed to switch off the chiller and
lock-out / isolate all chiller power supply. Be sure to
tag the chiller as “Out of Operation”. Keep the lock-out
key on person to avoid accidental chiller restart.
Suitability for Application
The OptiView Retrofit Kit is intended to control and
operate competitive centrifugal chillers cooling water
or brine solutions and is not suitable for purposes other
than those specified in these instructions. Any use of
the equipment other than what is intended or operation
of the equipment contrary to the relevant procedures
may result in injury to the operator, or damage to the
equipment. Johnson Controls will NOT be responsible
for damage due to misuse.
The chiller must not be operated outside the design pa-
rameters specified in any of the manuals included with
the OptiView Retrofit Kit and the Trane unit.
Structural Support
Proper structural support of the OptiView Panel must
be provided as indicated in these instructions. Failure
to provide proper support may result in injury to the
operator or damage to the equipment and/or building.
Mechanical Strength
The OptiView Panel is not designed to withstand
loads or stresses from adjacent equipment, pipework
or structures. No other components may be mounted
on or to the OptiView Control Panel. Any extraneous
loads may cause failure and may result in injury to the
operator, or damage to the equipment.
Pressure Systems
The chiller contains refrigerant vapor and liquid under
pressure, which can be a hazardous and cause injury if
released. Care must be taken during installation, opera-
tion and maintenance of this kit to avoid damage to the
pressure system. No attempt should be made to gain
access to the component parts of the pressure system
other than by suitably trained and qualified personnel.
Electrical
The control center must be grounded. No installation
or maintenance work should be attempted on the elec-
trical equipment without first switching the equipment
OFF, then isolating and locking out the power supply.
Work on live equipment must only be carried out by
suitably trained and qualified personnel. Do not at-
tempt to gain access to the inside of the control panel
or electrical enclosures during normal operation of the
unit.
Refrigerants and Oils
Refrigerants and oils used in the unit are generally non-
toxic, non-flammable and non-corrosive, and pose no
special safety hazards. However, when an open flame
is applied to refrigerant, toxic gases are created. Never
subject refrigerant to an open flame. The possibility of
refrigerant vapor build up does pose a risk of asphyxi-
ation in confined or enclosed spaces and attention
should be given to provide good ventilation.
Use of gloves and safety glasses are required when
working with refrigerant and oil.
Содержание YORK OPTIVIEW CONTROL CENTER
Страница 12: ...JOHNSON CONTROLS 12 FORM 160 10 O1 ISSUE DATE 4 27 2018 THIS PAGE INTENTIONALLY LEFT BLANK...
Страница 118: ...JOHNSON CONTROLS 118 FORM 160 10 O1 ISSUE DATE 4 27 2018 THIS PAGE INTENTIONALLY LEFT BLANK...
Страница 140: ...JOHNSON CONTROLS 140 FORM 160 10 O1 ISSUE DATE 4 27 2018 THIS PAGE INTENTIONALLY LEFT BLANK...