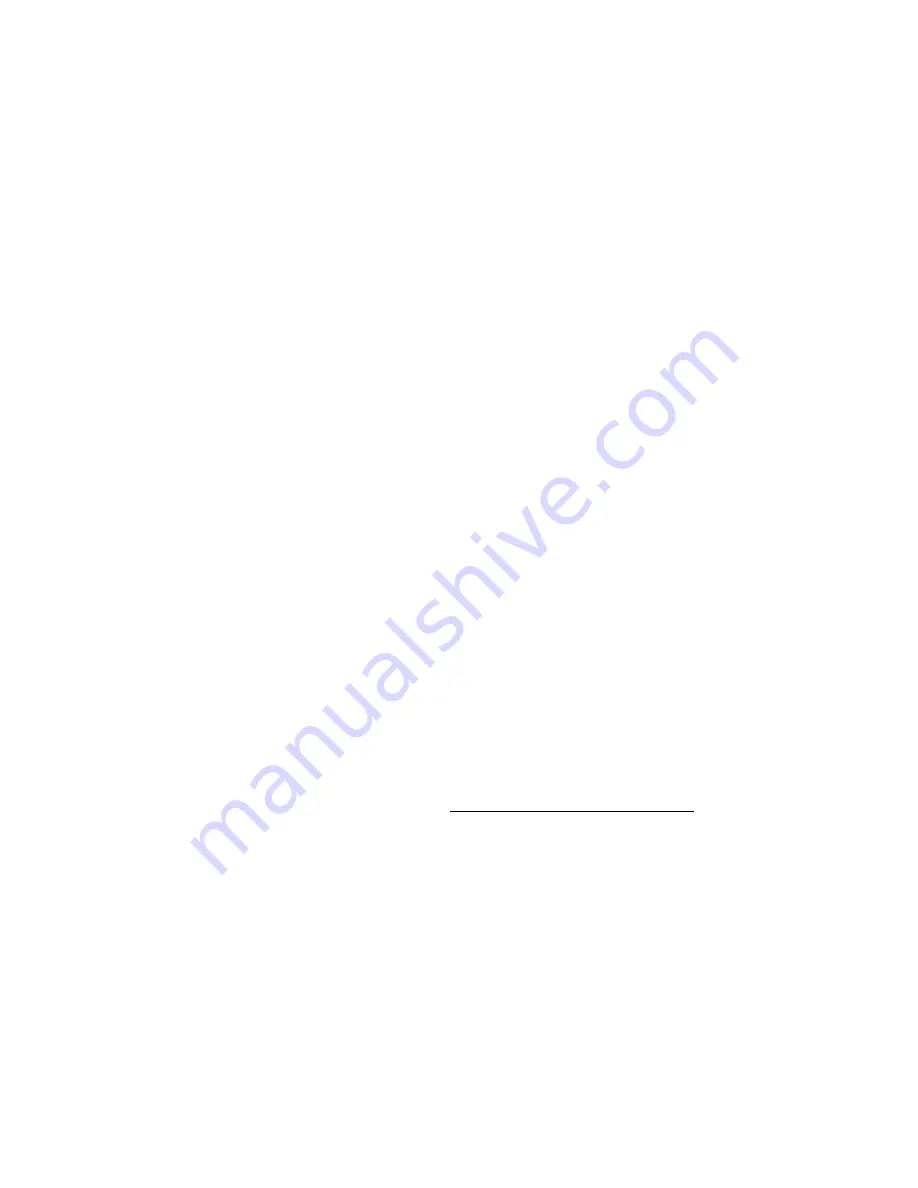
JOHNSON CONTROLS
114
FORM 160.10-O1
ISSUE DATE: 4/27/2018
SECTION 3 - OPTIVIEW DISPLAY MESSAGES
The chiller can be started after the temperatures are
within 3.0°F of one another and the compressor switch
is placed in the
STOP/RESET (O)
position.
Discharge – High Temperature
This message indicates the discharge temperature has
increased above 220.0°F. The chiller can be re-started
after the temperature decreases below 220.0°F and the
compressor switch is placed in the
STOP/RESET (O)
position.
Discharge – Low Temperature
This message indicates the discharge temperature has
decreased below 30.0°F. The chiller can be re-started
after the temperature increases above 30.0°F and the
compressor switch is placed in the
STOP/RESET (O)
position.
Oil – High Temperature
The oil temperature, as sensed by the oil temperature
thermistor, is above 180.0°F. The chiller can be started
after the temperature decreases below 180.0°F and the
compressor switch is placed in the
STOP/RESET (O)
position.
Oil – High Differential Pressure
Indicates the differential oil pressure increased above
60.0 PSID (159.0 PSID, if equipped with an auxil-
iary oil pump) while the oil pump was running. The
differential oil pressure is the difference between the
output of the sump oil pressure transducer (system
low pressure) and the output of the pump oil pressure
transducer (system high pressure). The chiller can be
started after the differential oil pressure decreases be-
low 60.0 PSID and the compressor switch is placed in
the
STOP/RESET (O)
position.
Oil – Low Differential Pressure
This message indicates the differential oil pressure is
below the low pressure cutout setpoint while the chiller
was running or dropped to less than 5.0 PSID above the
low pressure cutout by the last five (5) seconds of the
SYSTEM PRELUBE period. The differential oil pres-
sure is the difference between the output of the sump
oil pressure transducer (system low pressure) and the
output of the pump oil pressure transducer (system high
pressure). The chiller can be started after the compres-
sor switch is placed in the
STOP/RESET (O)
position.
Auxiliary Safety – Contacts Closed
The auxiliary safety shutdown contacts, connected to
I/O board TB4-31 have closed, initiating a safety shut-
down. This input is connected to the electromechanical
low differential oil pressure switch (LOPCO) installed
on chillers retrofitted with the OptiView panel. The
chiller can be started after the safety contacts open and
the compressor switch is placed in the
STOP/RESET
(O)
position.
Control Panel – Power Failure
A control panel power failure has occurred. If the power
failure duration was less than the duration of the pro-
grammed SYSTEM COASTDOWN period, the re-
mainder of the coastdown is performed upon restoration
of power. The chiller can be started after the compres-
sor switch is placed in the
STOP/RESET (O)
position.
The control center indicates a cycling shutdown when
this message is displayed in orange characters; a safety
shutdown when displayed in red characters. The control
center can be configured for auto-restart or manual re-
start after power failure by a qualified Service technician
following instructions in the
OptiView Control Center
Retrofit Kit - Trane Service Manual (Form 160.10-M1).
Motor or Starter – Current
Imbalance
The three phase compressor motor current imbalance
was higher than 30% continuously for 45 seconds. The
imbalance is not checked until the chiller has been run-
ning for at least 45 seconds and the average of the three
phases of motor current is greater than 80% of the pro-
grammed 100% chiller Full Load Amps. The average
is calculated as: Iave = (Ia+Ib+Ic) / 3. The imbalance
is calculated as:
(Ia-Iave)+(Ib-Iave)+(Ic-Iave)] x 100
2(Iave)
The Mod “B” Solid State Starter detects the imbalance
condition and transmits the condition to the OptiView
Control Center microboard via serial communica-
tions. The Variable Speed Drive returns the 3-phase
motor current values to the OptiView Control Center
microboard where the unbalance calculation is per-
formed. This safety shutdown is not performed on
electromechanical starter applications.
Motor – High Winding Temperature
This message indicates that a motor winding for cur-
rent phase A, B, or C has exceeded the programmed
winding cutout temperature, initiating a chiller shut-
Содержание YORK OPTIVIEW CONTROL CENTER
Страница 12: ...JOHNSON CONTROLS 12 FORM 160 10 O1 ISSUE DATE 4 27 2018 THIS PAGE INTENTIONALLY LEFT BLANK...
Страница 118: ...JOHNSON CONTROLS 118 FORM 160 10 O1 ISSUE DATE 4 27 2018 THIS PAGE INTENTIONALLY LEFT BLANK...
Страница 140: ...JOHNSON CONTROLS 140 FORM 160 10 O1 ISSUE DATE 4 27 2018 THIS PAGE INTENTIONALLY LEFT BLANK...