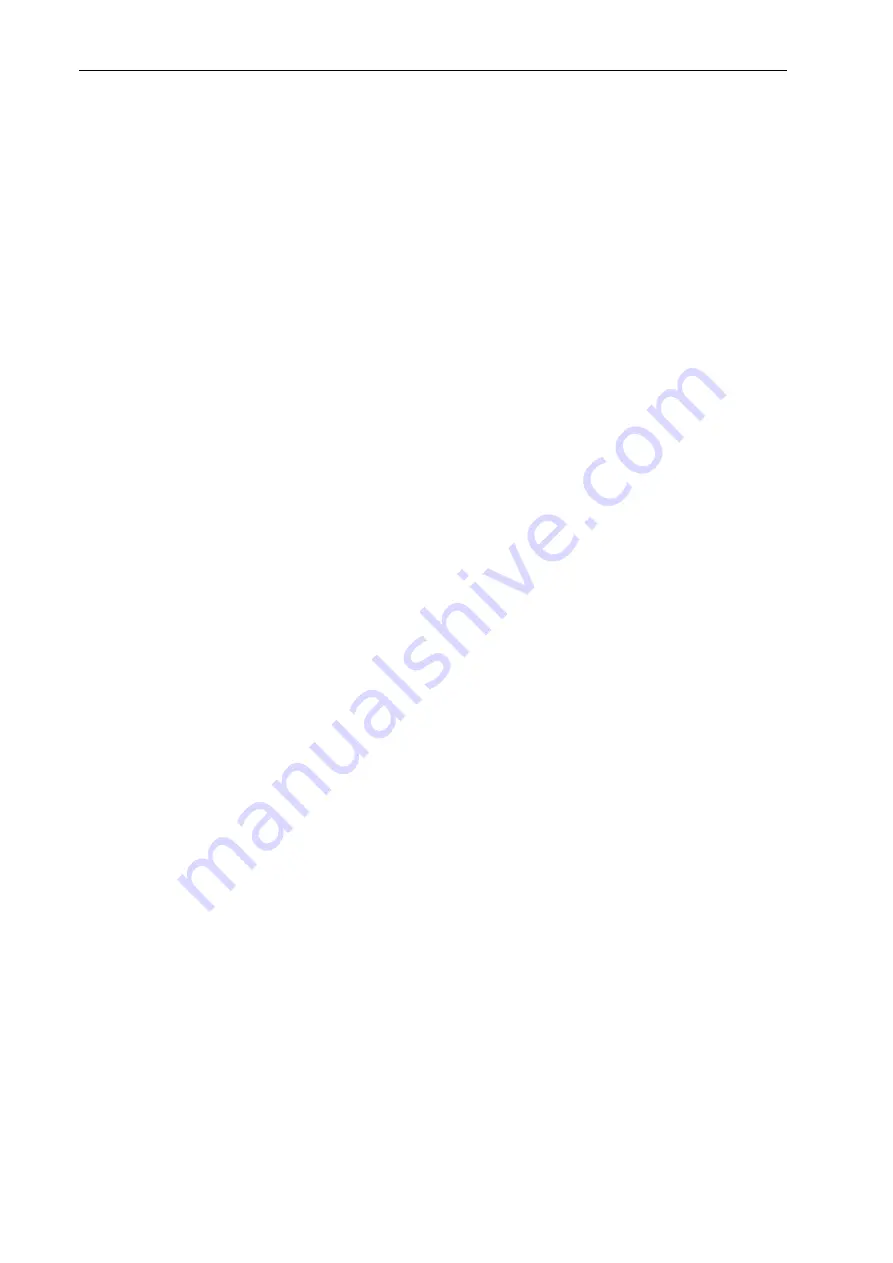
ACSetup programme
Positioning module IMD20, IMD40
of the axis acceleration (see “Acceleration dialogue box” on page 67) in order to go easy on the
mechanical a
run. In case of a referenc
al first the axis
moves after
offset without considering
r this the axis
m
eco
al.
l th
s
to the reference distance a
ro
o det
ind
st
you have to drive a reference r
thout index signal and then a reference run with index signal
(Dialog "Determine Index Offset" over button "Determine Index Offset ...")
r com
both reference runs the index offset is determined by the positions the refer
runs have
ched.
For this the difference position of the two reference runs is calculated. If
fference p
tion is
between 1/4 of the encoder resolution and 3/4 of the encoder resolution
dex offset
zero. If the difference position is out of this range the index offset is set t
encoder resolution.
With "Assume Index Offset" you can assume the set respectivly changed ind
g
"Reference Run".
T
ara
e
of the
ans
o
tio
efer
y
switch is us
d in which
direction the axis is to
order
eve a high precision of the machine’s zero point, a
combination with the ind
nal is p
provided the index signal is connected to the encoder.
Likewise, the speeds an
eference distance can be set here. Furthermore, there is the possibility
to test the reference run. You have to take into consideration that IMD20/IMD40 do not support a
reference switch, that mea
ser mu
ne a limit switch instead of a reference switch.
Internally, the module is switched to the Homing Mode – Reference run CanOpen mode of operation
for the execution of the reference run; then the reference run is started and, after its termination, the
p
ation is switched back to.
I
e run on one of the two limit switche
te that, during the reference run, the
output for the shunting of the limit switch (safety circui
s from
switching off, when the limi
case of a gantry axis, the master and slave axis may have different motion parameters and
der to adjust the deviation of position of both axes in the zero
point.
Object Directory dialogue box
T
irec
e view of all parameters (CanOpen objects) of the
d
Via
objects and read and / or write the
p
ord
ption of all objects can be found in the
c
CanOpen standards may use this dialogue box in
o
pa
hall realise the setting of parameters via the
“
ng”
f the Commissioning menu on page 43).
The tree view on the left side is su
), Device Profile (DS402) and
M
Spe
e characteristics and the content of the currently
s
ct ar
he <Assume> button, you can realise changes in the
c
eter
nfirms the current change and closes the dialogue box.
T
perm
urrently selected parameters
is
5 tim
e drive module (in case of an enabled online mode).
V
all
permanently store the currently set values
(set of pa
eters) in the d
rameters is not possible).
xis during the reference
switch off to the index
e run with index sign
the index signal. Afte
oves as long as it r
gnizes the index sign
nd then
the ze
After recognition of the
point of the axis. T
index signa
ermine the
e axis move
ex offset fir
sets
un wi
. Afte
pletion of the
ence
the di
rea
osi
the in
is set to
o 1/2
ex offset into the dialo
he dialogue box comprises
f <Type and direc
all p
n of the r
meters influ
ence run>,
ncing the execution
ou define e.g. which
reference run. By me
ed an
go. In
ex sig
to achi
ossible,
d the r
ns the u
st defi
revious mode of oper
n case of a referenc
s, no
t) is set in order to prevent the final stage
t switch is activated.
In
reference methods. Only the directions of the reference run have to be identical for both axes. On the
basis of the values indicated, the control calculates the optimum motion behaviour for both axes. The
reference distances can be used in or
he Object D
rive module.
tory dialogue box shows a tre
this structure, you can directly access all
arameter acc
ing to the respective characteristics. A descri
hapter on pa
88. Only users experienced in
rder to set
Commissioni
rameters. All other users s
dialogue box (see Commands o
bdivided into Com
cific Objects. On the right side, th
munication (DS301
anufacturer-
elected obje
e displayed. By means of t
urrent param
s. <OK> also co
he “
Update
anently
” option has the effect that the value of the c
read about
es per second from th
ia the “
Save
parameters in module
” button, you can
ing of individual pa
ram
rive module (the stor
76