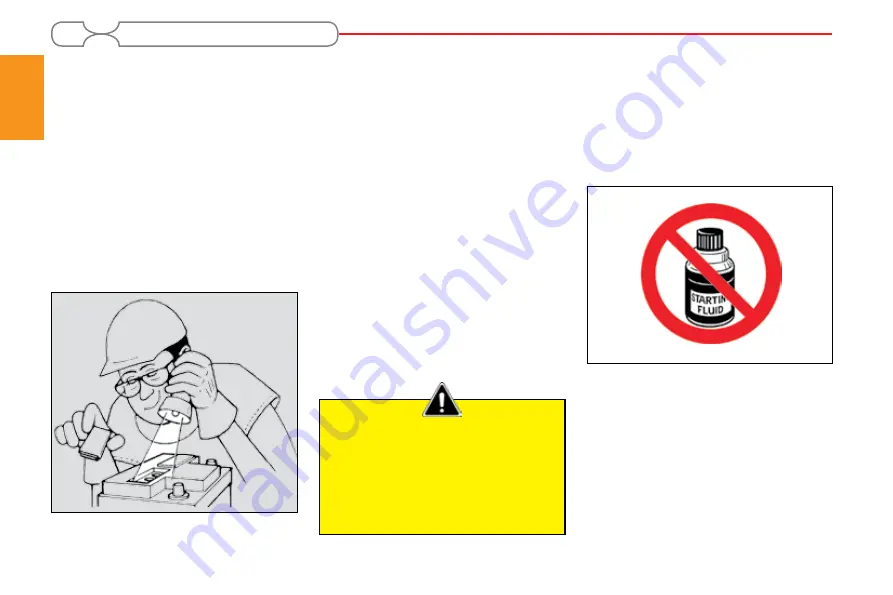
General information
1
8
thermostart cold starting device. If aerosol
cans of starting fluid, or ether start-aid,
are to be used the thermostart must be
disconnected. Remove the wire from the
thermostart unit which will be found on
the induction manifold. Tape the end of the
wire to prevent an electrical short circuit.
Fig. 13: .
Handle starting fluid as directed by the
manufacturer. Starting fluid must only be
used when an ether-start aid is fitted as
original equipment by the manufacturer or
when installed by a Dealer as an acces-
sory. In cases of tractors being fitted with
glow plugs or thermostart, these must
be removed prior to the installation of an
ether start-aid (Fig. 13).
mediately and show label.
9. Do not use a naked flame to check the
electrolyte level; always use a voltme-
ter or hydrometer to check the state
of charge.
10. Keep sparks flames and cigarettes
away, use a flashlight to check the bat-
tery electrolyte level if necessary.
11. Do not produce sparks with cable
clamps when charging the battery or
starting the tractor engine with a slave
battery.
12. Ensure vent plugs are correctly in-
stalled and tight.
13. Always remove the negative (-) cable
first.
Starting Fluid
Warning
DO NOT use aerosol cans of starting
aid on tractors with the thermostart
connected to the electrical system. Ether
combined with thermostart can cause
an explosion with damage to engine,
personal injury, or both.
Your tractor has been fitted with a
1. Corrosive substance.
2. Irritating to eyes and skin.
3 Keep out of the reach of children.
4. Avoid contact with skin and eyes.
5. Wear suitable protective clothing,
gloves and eye protection.
6. In case of contact with eyes rinse
immediately with plenty of water and
seek medical attention.
7. When charging the battery, charge in
a well ventilated place and ALWAYS
switch off at the mains before dis-
connecting the terminals.
Fig. 12: Check the state of charge of battery.
8. If swallowed seek medical advice im-
Содержание ITM 475
Страница 1: ...Iran Tractor Industrial Group OPERATOR INSTRUCTION BOOK Tractor Models ITM 475 2WD 4WD ITM 485 2WD 4WD...
Страница 3: ......
Страница 5: ......
Страница 23: ...General information 1 16 Safety decal location Both side Both side Both side...
Страница 24: ...1 General information 17 General decal location...
Страница 25: ......
Страница 37: ......
Страница 116: ...5 Specifications 109 Wiring diagram ITM 475 ITM 485...
Страница 117: ......