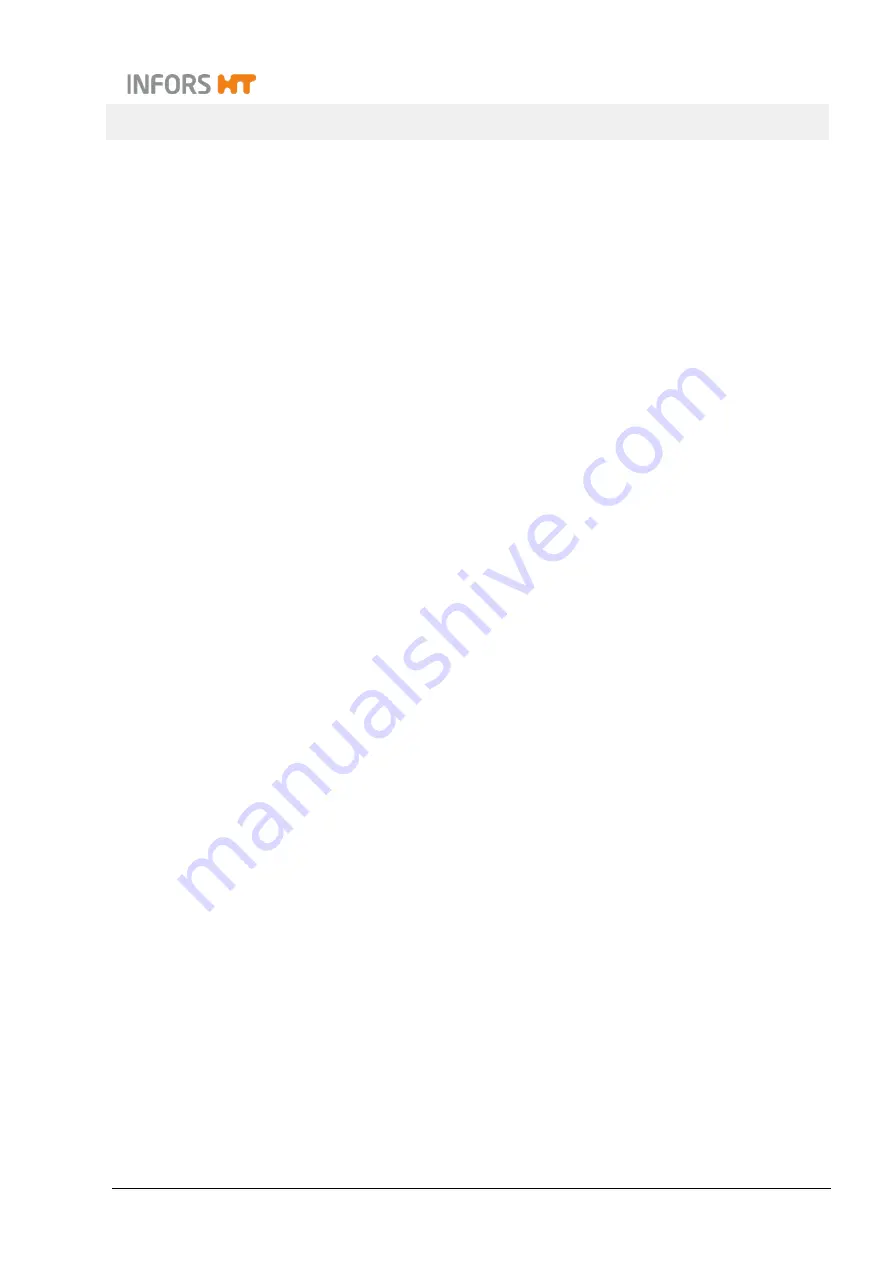
Minifors 2 - Benchtop Bioreactor
Table of Contents
07 February 2019
Page
1
of
214
1
General Information ............................................................... 9
1.1
About this Manual .......................................................... 9
1.2
Explanation of Special Notices ...................................... 9
1.2.1
Warning Notices ............................................. 9
1.2.2
Other Notices................................................ 10
1.3
Equipment Identification (Standard Identification Plate)
..................................................................................... 10
1.4
Declaration of Conformity ............................................ 11
1.5
Customer Service and Services .................................. 11
2
Safety and Responsibility ................................................... 12
2.1
Intended Use, Incorrect Use and Misuse .................... 12
2.2
Qualified Personnel ..................................................... 13
2.2.1
Provider ........................................................ 13
2.2.2
User .............................................................. 13
2.2.3
Operator ....................................................... 14
2.3
Unauthorised Persons ................................................. 15
2.4
Responsibility of the Provider ...................................... 15
2.5
General Hazards .......................................................... 15
2.5.1
Electrical Current .......................................... 16
2.5.2
Unauthorised Spare Parts and Accessories 16
2.6
Particular Hazards ....................................................... 16
2.6.1
Hot Surfaces ................................................. 17
2.6.2
Dangerous Gases ........................................ 17
2.6.3
Flammable or Explosive Substances ........... 17
2.6.4
Corrosive or Toxic Substances .................... 17
2.6.5
Bioactive Substances or Pathogenic
Organisms .................................................... 18
2.6.6
Overpressure or Vacuum ............................. 18
2.7
Warning Symbols on the Equipment ........................... 18
2.8
Declaration of Decontamination................................... 19
3
Setup and Function.............................................................. 20
3.1
Basic Unit ..................................................................... 20
3.1.1
Main Switch .................................................. 21
3.1.2
LED Strip ...................................................... 21
3.1.3
Pumps .......................................................... 21
3.1.4
Identification Plate ........................................ 22
3.1.5
Power Connection ........................................ 23
3.1.6
Water Connections ....................................... 23
3.1.7
Gas Connections .......................................... 23
3.1.8
Signal Connections ...................................... 24
3.1.9
Motor Cable Connection ............................... 24
Содержание Minifors 2
Страница 1: ...Operating Manual 2019 02 07 Minifors 2 Benchtop Bioreactor Dok ID 75623 V 03 00 Original...
Страница 217: ......