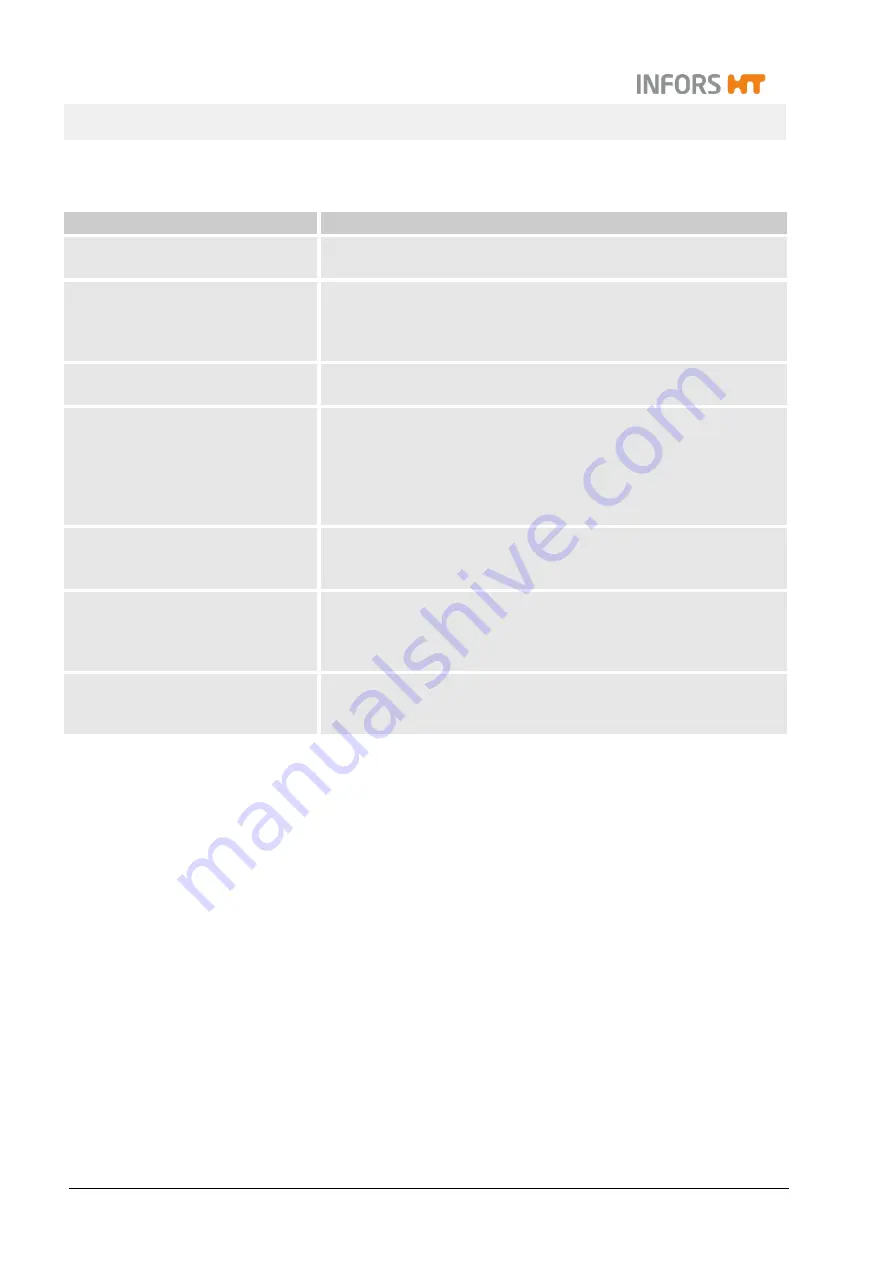
Minifors 2 - Benchtop Bioreactor
Operation
Page
180
of
214
07 February 2019
10.9.1 Table with Setting Values for PID Controller
Setting value
Description
P (Prop. Term)
Proportional factor: The greater the discrepancy between the set-
point value and the actual value the greater the controller output
I (Integ. Term [1/s] )
The integral factor aggregates all errors over the time. If the setpoint
is not achieved using the proportional factor, the integral factor ad-
justs the output successively until the setpoint value is achieved. An
integral factor set too high will lead to oscillation of the control loop.
D (Diff Term [s]
The differential quotient calculates the change in the actual value
over the time and counteracts this change to limit any overshoot.
Neg. Factor
The negative factor can be used to add weighting to two-sided con-
trol (+100 to -100 %) (e.g. heavy acid, light alkali). In the process 1 is
the balance and 0.5 or 2 equate to the half or double the controller
output accordingly. Example: Nitrogen influences the pO
2
value less
than oxygen, thus a negative factor of 2 can compensate for the re-
action of the controller.
Deadband
If a dead band is entered, no control is implemented within this value
at either side of the setpoint value (symmetrically, + / -). I.e. the con-
troller output is = 0. The dead band is used for pH control.
I Limit (Integ. Limit [%])
The integral influence is used to ensure that the integral factor can-
not increase over an indefinite period. This limits erroneous accumu-
lation. The integral influence is set between 0 and 100 % of the con-
troller output.
Eval Time [s]
The evaluation time determines the intervals in seconds at which the
PID value is recalculated. The controller speed is defined this way. A
scanning time of 10 seconds is a good average value.
10.9.2 Useful Information for Changing PID Controller Settings
To adjust the PID controller settings, proceed as follows:
Procedure
1.
For readjustment of a PID controller, start with the setting for
the proportional factor. Select a proportional band width as
large as possible.
2.
Reset the integral factor and the differential quotient to zero.
3.
Increase the proportional factor until the controller causes the
actual value to oscillate.
4.
Measure the oscillation duration, e.g. with the bioprocess plat-
form software eve® from the manufacturer.
5.
Halve the proportional factor and vary the integral factor be-
tween the reciprocal value of the doubled and quadrupled os-
cillation duration.
Содержание Minifors 2
Страница 1: ...Operating Manual 2019 02 07 Minifors 2 Benchtop Bioreactor Dok ID 75623 V 03 00 Original...
Страница 217: ......