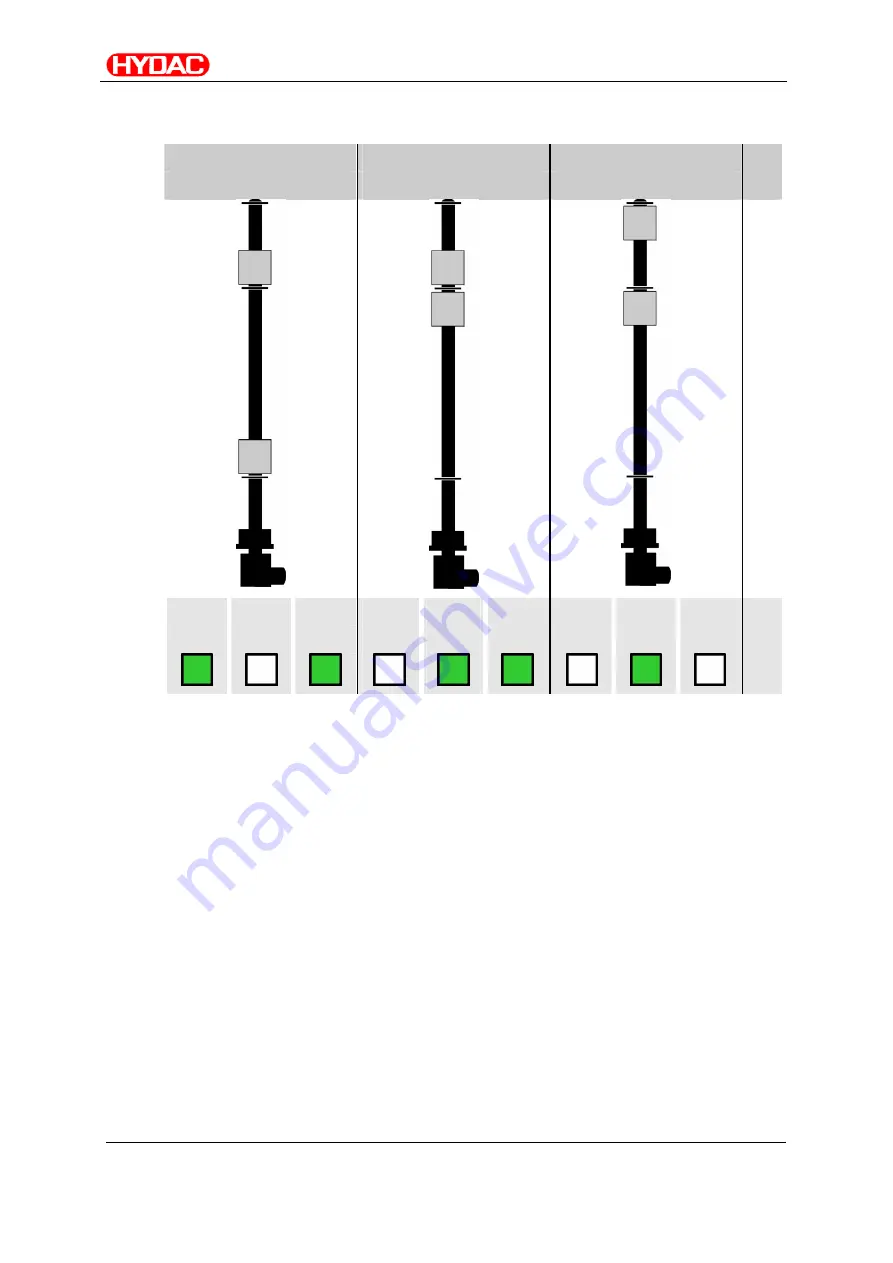
Performing Maintenance
FAM 25/45/60/75/95
en(us)
Page 115/160
BEWA FAM25-95 3402054f en(us) 2013-06-13
2013-06-13
Switching Status - Level Sensor Vacuum Column/PLC
[01]
[02]
[03]
Minimum
Maximum
Maximum E-STOP
Level
Level sensor
I0.3
I0.4
I0.5
I0.3
I0.4
I0.5
I0.3
I0.4
I0.5
ON
OFF
ON
OFF
ON
ON
OFF
ON
OFF
PLC