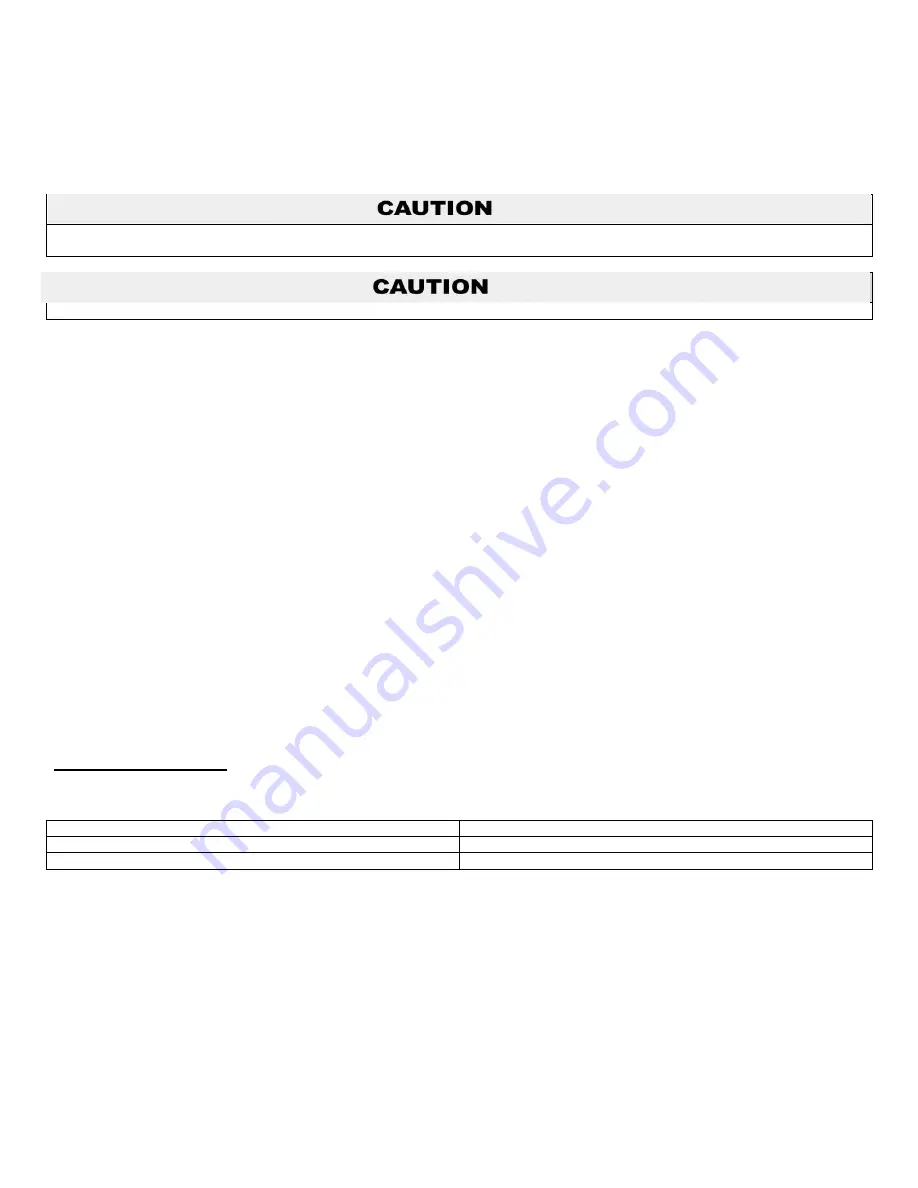
18
LP- 428 REV. 9.2.14
Freeze protection for new or existing systems must use glycol specifically formulated for this purpose. This glycol must include
inhibitors that will prevent it from attacking metallic system components. Make certain that the system fluid is checked for the correct
glycol concentration and inhibitor level. The system should be tested at least once a year and as recommended by the producer of the
glycol solution. Allowance should be made for the expansion of the glycol solution in the system piping. Example: 50% by volume glycol
solution expands 4.8% in volume for the temperature increase from 32
o
F to 180
o
F, while water expands 3% over the same temperature
rise.
Never use dielectric unions or galvanized steel fittings when connecting to a stainless steel storage tank or boiler. Failure to follow this
instruction can lead to premature failure of the boiler system. Such failures ARE NOT covered by warranty.
The boiler should not be operated as a potable hot water heater. The boiler should not be used as a direct hot water heating device.
Basic steps are listed below that will guide the installation of the boiler.
1. Connect the system return marked “Boiler Return”.
2. Connect the system supply marked “Boiler Supply”.
3. Install purge and balance valve or shut off valve and drain on system return to purge air out of each zone.
4. Install a back flow preventer on the cold feed make-up water line.
5. Install a pressure reducing valve on the cold feed make-up water line (15 PSI nominal on the system return). Check temperature and
pressure gauge when operating. It should read a minimum pressure of 12 PSI.
6. Install a circulator as shown in piping details (this section). Make sure the circulator is properly sized for the system and friction loss.
7. Install an expansion tank on the system supply. Consult the tank manufacturer’s instructions for specific information relating to
expansion tank installation. Size the expansion tank for the required system volume and capacity.
8. Install an air elimination device on the system supply.
9. Install a drain valve at the lowest point of the system.
NOTE:
The boiler cannot be drained completely of water without purging the
unit with an air pressure of 15 PSI.
10. The relief valve is installed at the factory. A pipe discharge line should be installed to discharge 6” above the drain in the event of
pressure relief. The pipe size must be the same size as the relief valve outlet.
NEVER BLOCK THE OUTLET OF THE SAFETY
RELIEF VALVE.
G. CIRCULATOR SIZING
In addition, the boiler heat exchanger has a minimum total water volume that must be taken into account when sizing the circulator.
Minimum boiler flow rates are listed in the table below.
MODEL
MINIMUM BOILER FLOW RATE (GPM)
MODCON1000
66
MODCON1700
109
Table 3
– Minimum Boiler Flow Rates
The boiler heat exchanger does have a pressure drop which must be considered in system design. Refer to the graph in Figure 5 for
pressure drop through the boiler heat exchanger.
Содержание MODCON1000
Страница 40: ...40 LP 428 REV 9 2 14 E GAS VALVE Figure 22 Mod Con 1000 Gas Valve ...
Страница 46: ...46 LP 428 REV 9 2 14 Figure 25 Figure 26 Cascade Resistor Plug Installation Detail ...
Страница 47: ...47 LP 428 REV 9 2 14 Figure 27 Mod Con Cascade Master and Follower Wiring ...
Страница 48: ...48 LP 428 REV 9 2 14 Figure 28 Mod Con Internal Connection Diagram LP 428 K ...
Страница 70: ...70 LP 428 REV 9 2 14 Figure 31 MOD CON 1000 External Parts Blowout ...
Страница 71: ...71 LP 428 REV 9 2 14 Figure 32 MOD CON 1700 External Parts Blowout ...
Страница 72: ...72 LP 428 REV 9 2 14 Figure 33 ...
Страница 73: ...73 LP 428 REV 9 2 14 Figure 34 LP 445 S ...
Страница 74: ...74 LP 428 REV 9 2 14 Figure 35 LP 428 V ...
Страница 75: ...75 LP 428 REV 9 2 14 Figure 36 ...
Страница 78: ...78 LP 428 REV 9 2 14 ...
Страница 79: ...79 LP 428 REV 9 2 14 ...
Страница 80: ...80 LP 428 REV 9 2 14 MAINTENANCE NOTES ...