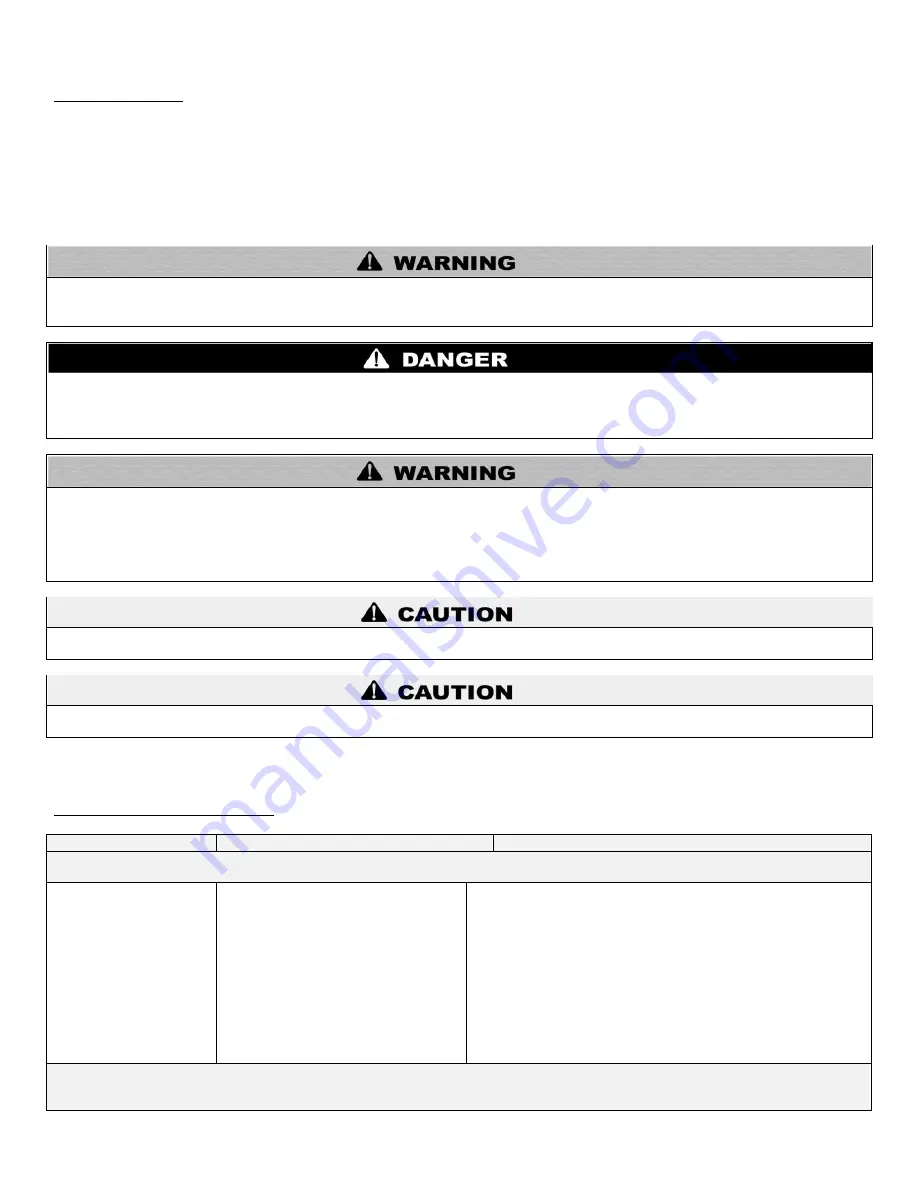
62
LP- 428 REV. 9.2.14
C. BOILER FAULT
1.
When a fault condition occurs, the controller will illuminate the red “FAULT” indication light and display a fault message in the screen.
The alarm output will also activate. Most fault conditions cause the CH pump to run in an attempt to cool the boiler.
2. Note the fault message displayed and refer to Part D in this section for an explanation of the message along with several suggestions
for corrective actions.
3. Press the reset key to clear the fault and resume operation. Be sure to observe the operation of the boiler for a period of time to
assure correct operation and no reoccurrence of fault message.
When servicing or replacing any components of this boiler, be certain that:
The gas is off.
All electrical power is disconnected.
When servicing or replacing components that are in direct contact with boiler water, be certain that:
There is no pressure in the boiler. (Pull the release on the relief valve. Do not depend on the pressure gauge reading.
The boiler water is not hot.
The electrical power is disconnected.
DO NOT USE THIS BOILER IF ANY PART HAS BEEN SUBMERGED IN WATER.
Immediately call a qualified service technician. The
boiler MUST BE replaced if it has been submerged. Attempting to operate a boiler that has been submerged could create numerous
harmful conditions, such as a potential gas leakage causing a fire and/or explosion, or the release of mold, bacteria, or other harmful
particulates into the air. Operating a previously submerged boiler could result in property damage, severe personal injury, or death.
NOTE:
Boiler damage due to flood or submersion is considered an Act of God, and IS NOT covered under product warranty.
Observe the position of each wire and label before removing. Wiring errors may cause improper and dangerous operation. Verify proper
operation after servicing.
If overheating occurs, or the gas supply fails to shut off, do not turn off electrical power to the circulating pump. This may aggravate the
problem and increase the likelihood of boiler damage. Instead, shut off the gas supply to the boiler at the gas service valve.
NOTE:
If system return temperatures are maintained below the dew point, condensation will form on the inside of the boiler cabinet and
cause some internal sheet metal components to rust.
D. USER INTERFACE DISPLAY
Cascade Control FAULT Codes
SCREEN
DESCRIPTION
POSSIBLE REMEDY
Fault Code EO3
System Sensor Failure
SYS SUPPLY SENSOR
PUMP OFF E03
This screen shows that there is a problem
with the system sensor circuit. The circuit
could be open or shorted. Possible reasons
for this error are:
There is no system sensor connected to the
Master Boiler.
The system sensor is faulty.
There is a short circuit in the system sensor
wiring; possibly from a staple placed
through the wire, or damage to the wire
causing both conductors to touch.
The system sensor wiring is open due to
defect or damage.
Disconnect the system sensor from the wiring and measure the
resistance of it. Compare the measured resistance to the table in this
manual to see if it corresponds to the temperature of the sensor. If the
resistance does not agree with the sensor, replace the sensor. If the
sensor is OK, disconnect the sensor wiring from both the boiler and the
sensor and check continuity using an ohmmeter. Repair or replace as
necessary.
If this error is present, all boilers in the cascaded group will run and ignite
simultaneously when there is a heat demand. Each boiler will modulate
to maintain set point temperature on its own supply sensor. This code
will reset automatically when repair is complete. This code will not
display if system setting function ERROR SYSTEM SENS is set to OFF.
Содержание MODCON1000
Страница 40: ...40 LP 428 REV 9 2 14 E GAS VALVE Figure 22 Mod Con 1000 Gas Valve ...
Страница 46: ...46 LP 428 REV 9 2 14 Figure 25 Figure 26 Cascade Resistor Plug Installation Detail ...
Страница 47: ...47 LP 428 REV 9 2 14 Figure 27 Mod Con Cascade Master and Follower Wiring ...
Страница 48: ...48 LP 428 REV 9 2 14 Figure 28 Mod Con Internal Connection Diagram LP 428 K ...
Страница 70: ...70 LP 428 REV 9 2 14 Figure 31 MOD CON 1000 External Parts Blowout ...
Страница 71: ...71 LP 428 REV 9 2 14 Figure 32 MOD CON 1700 External Parts Blowout ...
Страница 72: ...72 LP 428 REV 9 2 14 Figure 33 ...
Страница 73: ...73 LP 428 REV 9 2 14 Figure 34 LP 445 S ...
Страница 74: ...74 LP 428 REV 9 2 14 Figure 35 LP 428 V ...
Страница 75: ...75 LP 428 REV 9 2 14 Figure 36 ...
Страница 78: ...78 LP 428 REV 9 2 14 ...
Страница 79: ...79 LP 428 REV 9 2 14 ...
Страница 80: ...80 LP 428 REV 9 2 14 MAINTENANCE NOTES ...