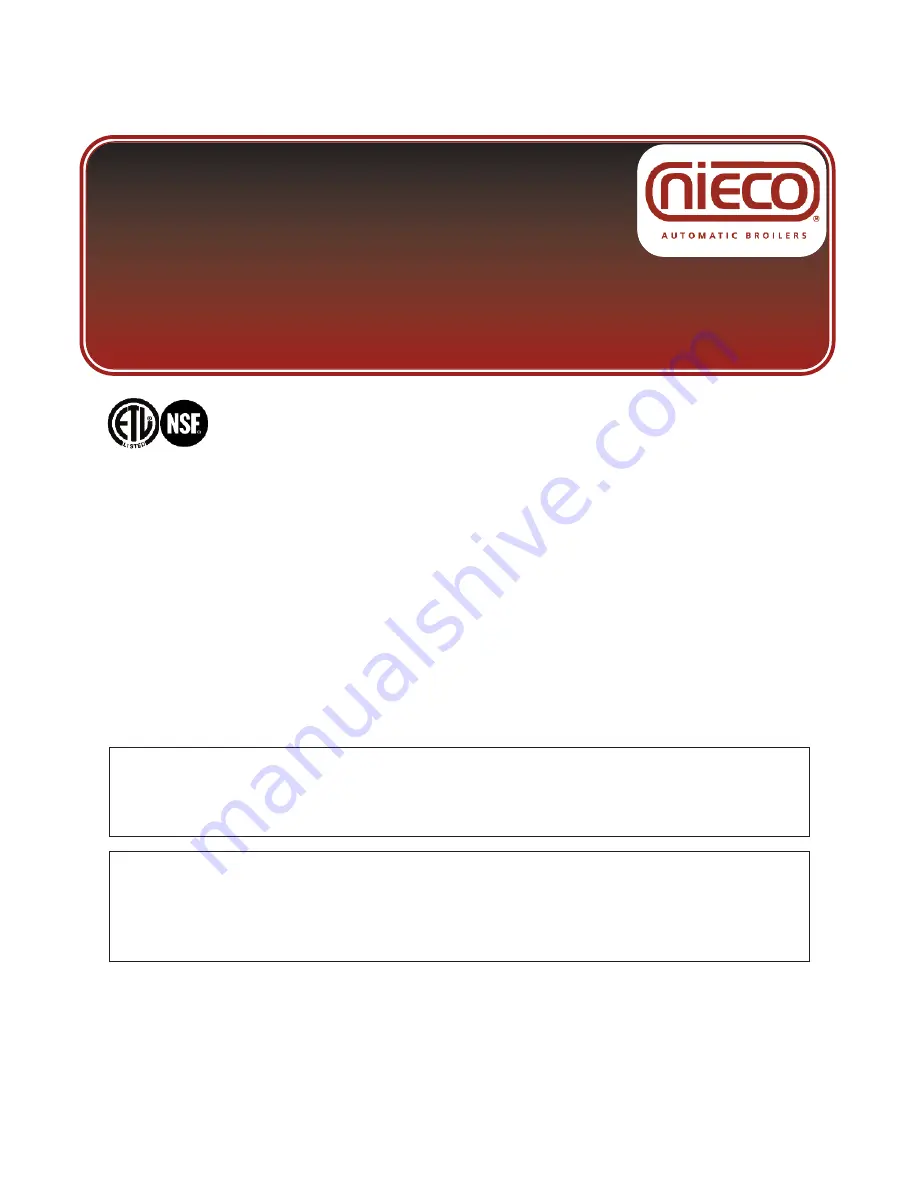
W A R N I N G :
Improper installation, adjustment, alteration, maintenance can cause property damage, injury, or death.
Read the installation, operating and maintenance instructions thoroughly before installing or servicing
this equipment.
F O R YO U R S A F E T Y:
Do not store or use gasoline or other flammable vapors or liquids in the vicinity of this or any other
appliance.
APPROVALS:
IMPORTANT: RETAIN THIS MANUAL IN A SAFE PLACE FOR FUTURE REFERENCE
Broiler area must be kept free of combustible materials, and the flow of combustion and ventilation air
must not be obstructed. Operating personnel must not perform any maintenance or repair
functions. Contact your Nieco Authorized Dealer.
Model JF63 Gas
Owner’s Manual
BroilVection
™