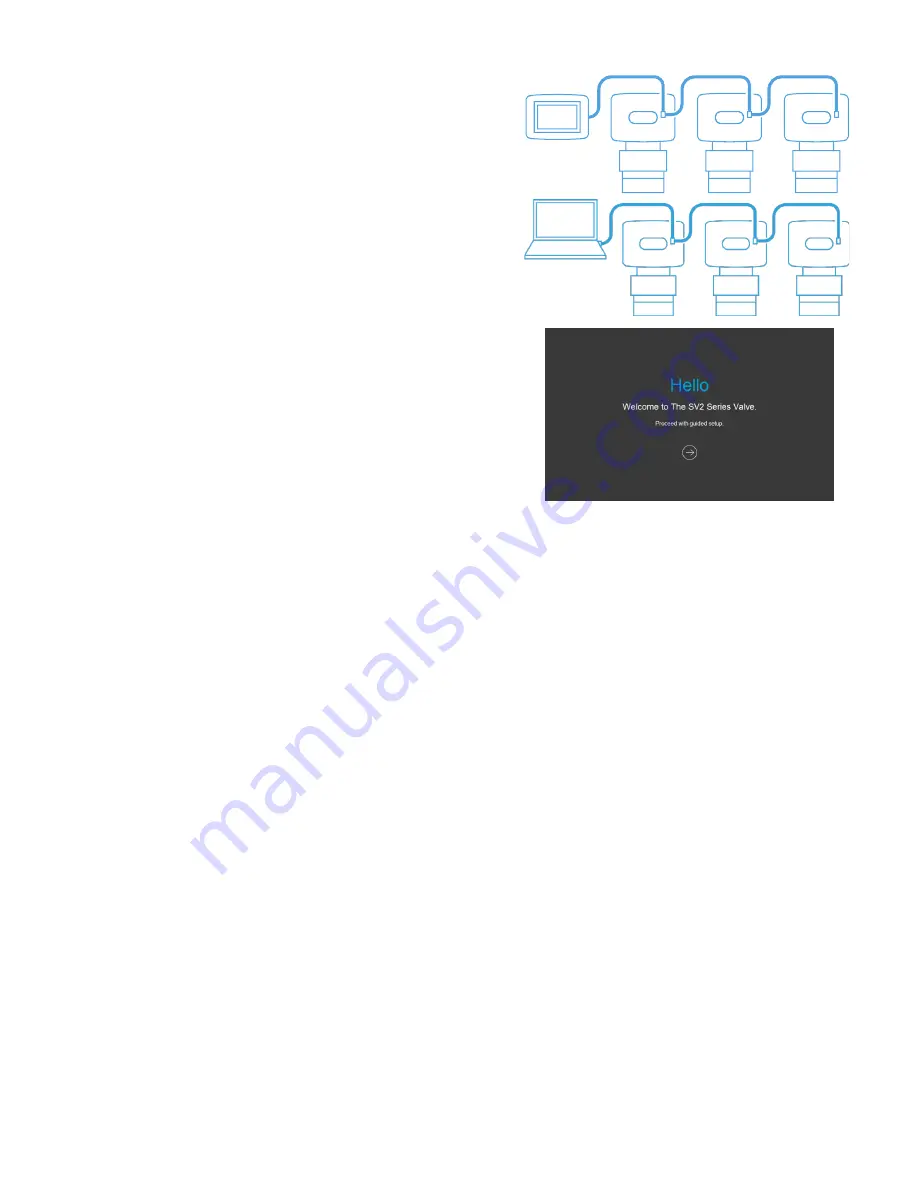
SV2 Series Safety Shut-off Valves
47
V2F, V2V
SV2 SERIES SAFETY SHUT-OFF VALVES USER MANUAL
Programming Tools
There are two available models of programming tools for use with the
SV2 Series valves with intelligent features. There is an HMI (human
machine interface) version and a PC (personal computer) version
available.
Either tool is required to complete initial setup of any intelligent valve
features before the valve will be operational.
For further details on the use of the HMI and PC Tools and
specifications, refer to the
APPENDIX of this manual for the detailed
Modbus addressing information and CHAPTER 4 : ACCESSORIES,
FIELD REPLACEMENTS AND INTELLIGENT FEATURES
section of this
document as well as the reference documents.
Up to 8 valves may be wired to a single HMI or PC Tool in daisy chain
fashion. Refer to the Connectivity Notes section that follows for
important information
Connectivity Notes
From the factory, the default Modbus address for all valves is 1. If the intent is to connect more than 1 valve to the programming
tool or external Modbus master, make sure each connected valve is given a unique Modbus address. Once The HMI or PC Tool is
connected to the valve and communicating, the Modbus address may be changed. Modbus addresses can be from 1 to 247.
This manual provides an overview of connectivity to the valve, HMI Tool, PC Tool and an external Modbus master. Detailed
wiring, setup and connectivity information is provided in the reference documents listed below. When attempting connectivity
and valve programming activities, referencing these documents is imperative.
IMPORTANT
• When intending to connect more than 1 valve to the HMI or PC Tool or an external Modbus master, each valve must be
individually connected and programmed first with each valve given a unique Modbus address. Once this is complete, all
valves may be wired in a daisy chain fashion to a single HMI Tool port, PC Tool USB to RS485 converter or a Modbus master
single port.
• From the factory, the default baud rate for all valves and the HMI or PC Tools is 38400 bps. Both baud rates may be changed
AFTER CONFIGURATION IS COMPLETE FOR THE PROGRAMMING TOOL AND ALL VALVES. The baud rate selections are
9600, 19200, 38400 or 57600 bps. Communication must first be established with the valve at the default 38400 bps rate
with the programming tool, then the valve baud rate may be changed, followed by the programming tool baud rate. For
detailed information, refer to the HMI / PC Tool User Manual listed below.
• For best HMI communication performance, use shielded cable with two twisted pairs (Belden 9842 or equivalent). Connect
the + and – to one twisted pair and C to both wires of the other twisted pair. Connect the shield to earth ground at the end of
the connected external device. Do not connect C to the shield. Refer to the HMI or PC Tools Installation Instructions listed
below for detailed wiring information.
• Use the provided clamp filters with the HMI Tool to protect against conducted and radiated transient noise for the 24VAC
and COM connections.
• Separate line and low voltage wiring to avoid signal interference. If using conduit, run line voltage and low voltage wiring in
separate conduit. Route any noise producing wires as far away from the HMI as possible.