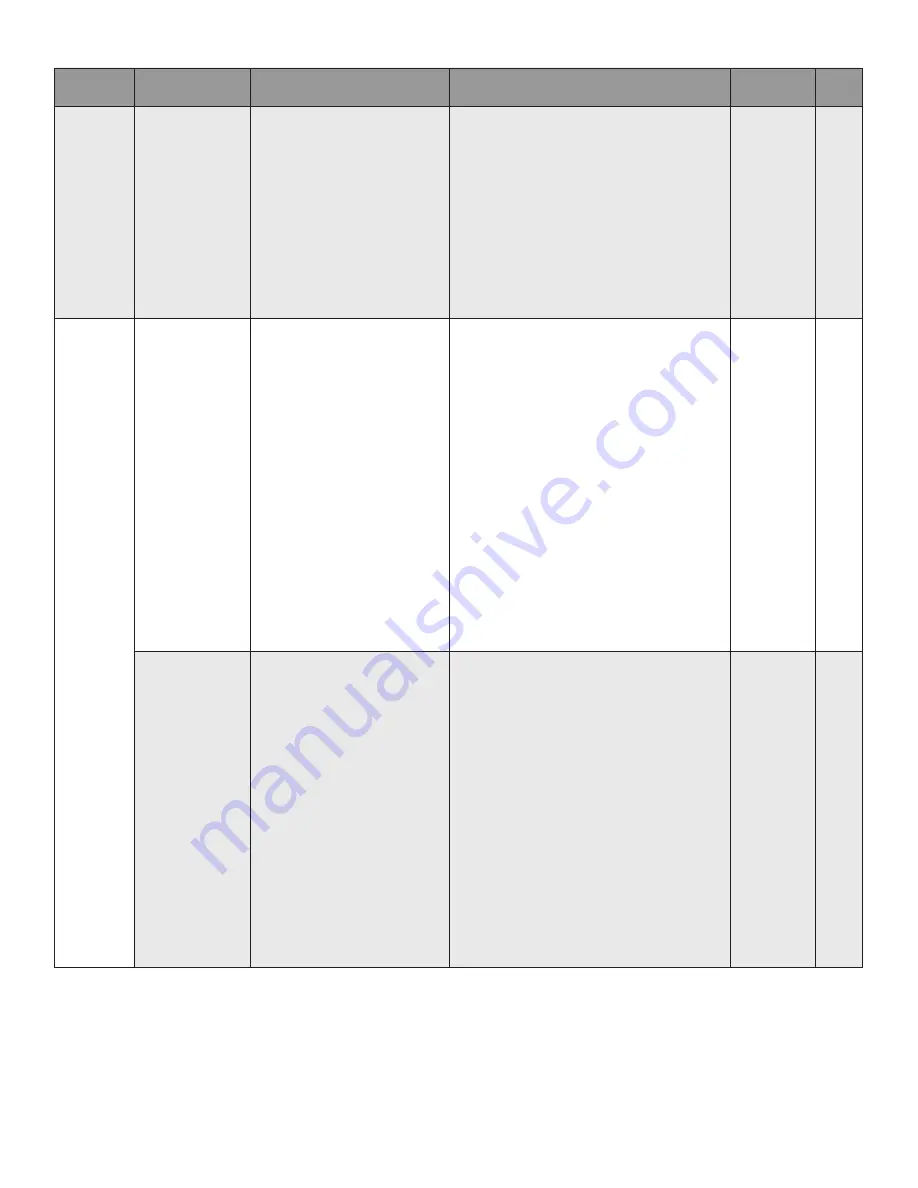
SV2 Series Safety Shut-off Valves
198
32-00029—02
Fault
Category
Fault
Description
Detailed Description
Remediation Steps
Comments Fault
#
Phase
Incoming
voltages out of
phase
Valve incoming L1 VAC to
POC or VPS or L1 VAC from
burner management system
to valve ILK IN, MV1 / MV2 is
out of phase.
1.) Reset valve and burner management
system, monitoring for proper operation.
2.) Check the valve power supply to make
sure that both frequency and voltage meet
the specifications.
3.) Verify that the valve, burner
management system and associated
devices are fed from the same phase. If a
VFD (variable frequency drive) is present,
ensure that it does not share a common
neutral or ground.
Warning
indication
for SV2
valve.
15
POC
POC (proof
of closure)
switch(es)
signal fault
Valve POC (proof of closure)
switch(es) signal is not valid.
Frequency or duty is out of
expected range.
Remove power and shut-off gas supply as
necessary.
1.) Remove valve front electrical enclosure
and inspect L1, Neutral, and POC wiring
connection for proper seating, pin
engagement and cleanliness. Correct any
errors.
2.) Check the valve power supply to make
sure that both frequency and voltage meet
the specifications.
3.) Replace cover and restore power and
gas. Reset valve and burner management
system, monitoring for proper POC
operation in conjunction with valve LEDs
and burner management system inputs.
4.) If fault persists, replace valve main
electronics.
10
POC output
signal mis-
match
Valve POC (proof of closure)
output terminal to burner
management control
energized while internal POC
relay is not energized.
Or POC output terminal to
burner management control
not energized while POC
relay is energized.
Possible internal fault,
malfunction of relay or
external mis-wiring of valve.
Remove power and shut-off gas supply as
necessary.
1.) Remove valve front electrical enclosure.
2.) Inspect external wiring between
valve POC terminal and burner
management system for proper seating,
pin engagement and cleanliness. Ensure
the valve POC terminal is not externally
powered. Correct any errors.
3.) Replace cover and restore power and
gas. Reset valve and burner management
system, monitoring for proper POC
operation in conjunction with valve LEDs
and burner management system inputs.
4.) If fault persists, replace valve main
electronics.
74