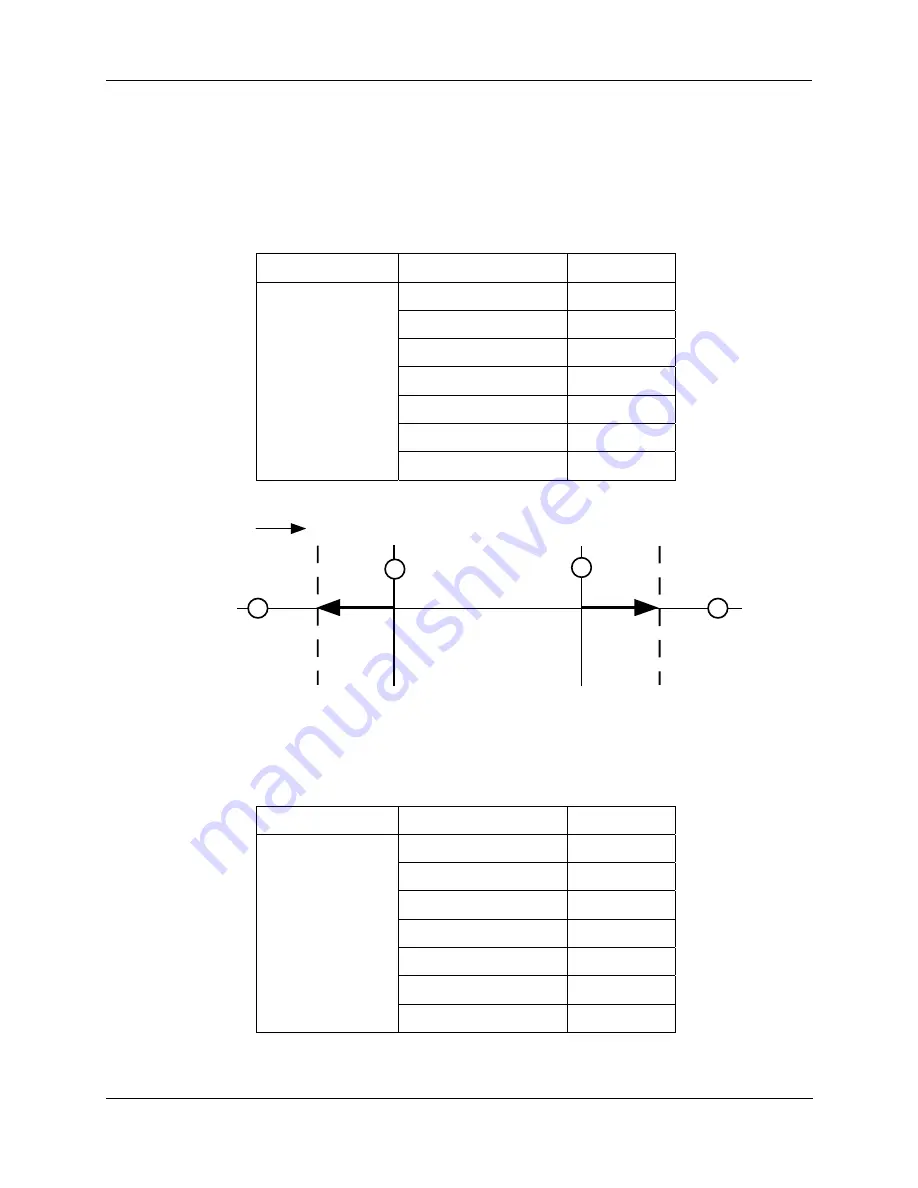
4. Set Up and Calibration Procedures - Relays Set Up Group
Revision 5
10260S HercuLine® Actuator Installation, Operation and Maintenance Manual
41
7/07
Relay Examples
Relay Type - Position Range
Selecting PosR relay type, you can cause the relay to energize when the actuator motor travels below 20%
of range and above 80% of range. Note in the example below that Relay 1 is set up to provide two trip
points. The first trip point (R11VAL) causes the relay to energize when the motor travels above 80%, the
second trip point (R12VAL) is set so the relay energizes when the motor travels below 20%.
Set Up Group
Parameter
Value
SET RELAY1
RTYP11
PosR
R11VAL
80.0
R11HL
HI
RTYP12
PosR
R12VAL
20.0
R12HL
LO
RLY1HY
0.0
The figure below shows the resulting action.
100%
0%
18
Closed
20%
80%
RELAY 1
Normally Open
Closed
Open
Motor
Position
17
18
17
Relay Type - Deviation
Setting up a relay to alarm (energize) when the motor position deviates 10% (+ or -) from the actuator
setpoint can be set up as follows.
Set Up Group
Parameter
Value
SET RELAY1
RTYP11
DEV
R11VAL
10.00
R11HL
HI
RTYP12
DEV
R12VAL
-10.00
R12HL
LO
RLY1HY
0.0
The resulting action is shown below.
Содержание HercuLine 10260S
Страница 10: ......
Страница 94: ......
Страница 121: ......
Страница 122: ...Honeywell Field Solutions Honeywell Inc 512 Virginia Drive Fort Washington PA 19034 ...