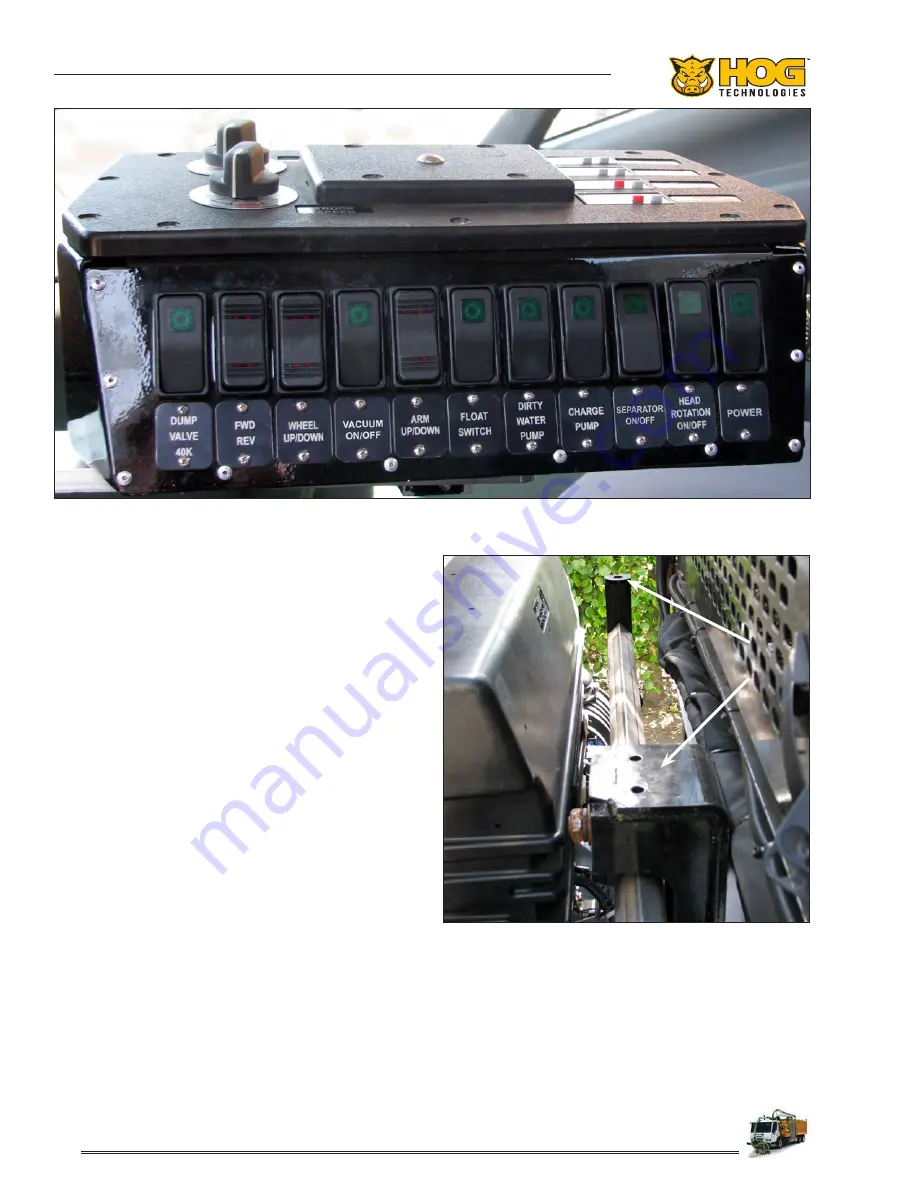
66
Operation
3.4 Water Blasting System Startup
The Procedure to shift the truck and skid from
transport mode to work mode and activate the
water blasting systems is the same for trucks with
a manual or automatic transmission.
Make sure the truck is maneuvered into position
and aligned at the starting point of the removal
job before configuring the truck for work mode.
Truck startup and configuring the Hog Arm,
Hog Head and vacuum separator for work
mode:
1. Be sure the truck transmission is in NEUTRAL
and the park brake is set.
2. Turn the skid main circuit breaker ON.
3. Remove the lock pin in the Hog Arm slide track
and pull the arm and slide assembly OUT to
the full out/work position.
4.
Align the hole in the fitting on the track with
the hole in the frame boss and insert the lock
pin to secure the arm and slide assembly in
work position.
5. Make sure all switches and speed dials are in
the OFF position or set at 0.
6. Start truck engine and allow the engine to run
at idle speed.
OPERATE
MODE
Console Switch Panel
Track Fitting & Frame Boss Safety Pin Holes
7. Turn the truck PTO switch ON to activate the
hydraulic system. Verify the red LED light in
the PTO switch panel is lit.
8. Activate the POWER switch on the console
switch panel. Verify the Green LED light in the
switch is lit.
Содержание Stripe Hog SK2000
Страница 2: ...2...
Страница 6: ...6 NOTES...
Страница 142: ...142 NOTES...
Страница 147: ...147 Appendix 2 Tools Spare Parts...
Страница 148: ...148 Tools Spare Parts...
Страница 149: ...149 Appendix 3 Daily Report Pre Op Checklist 1 877 HOG ROAD WWW STRIPEHOGSUPPORT COM 60...
Страница 157: ...157 Spray Bar Nozzle Configuration 1 877 HOG ROAD WWW STRIPEHOGSUPPORT COM 68 Nozzle Calculation Sheet...
Страница 158: ...158 NOTES...
Страница 165: ......