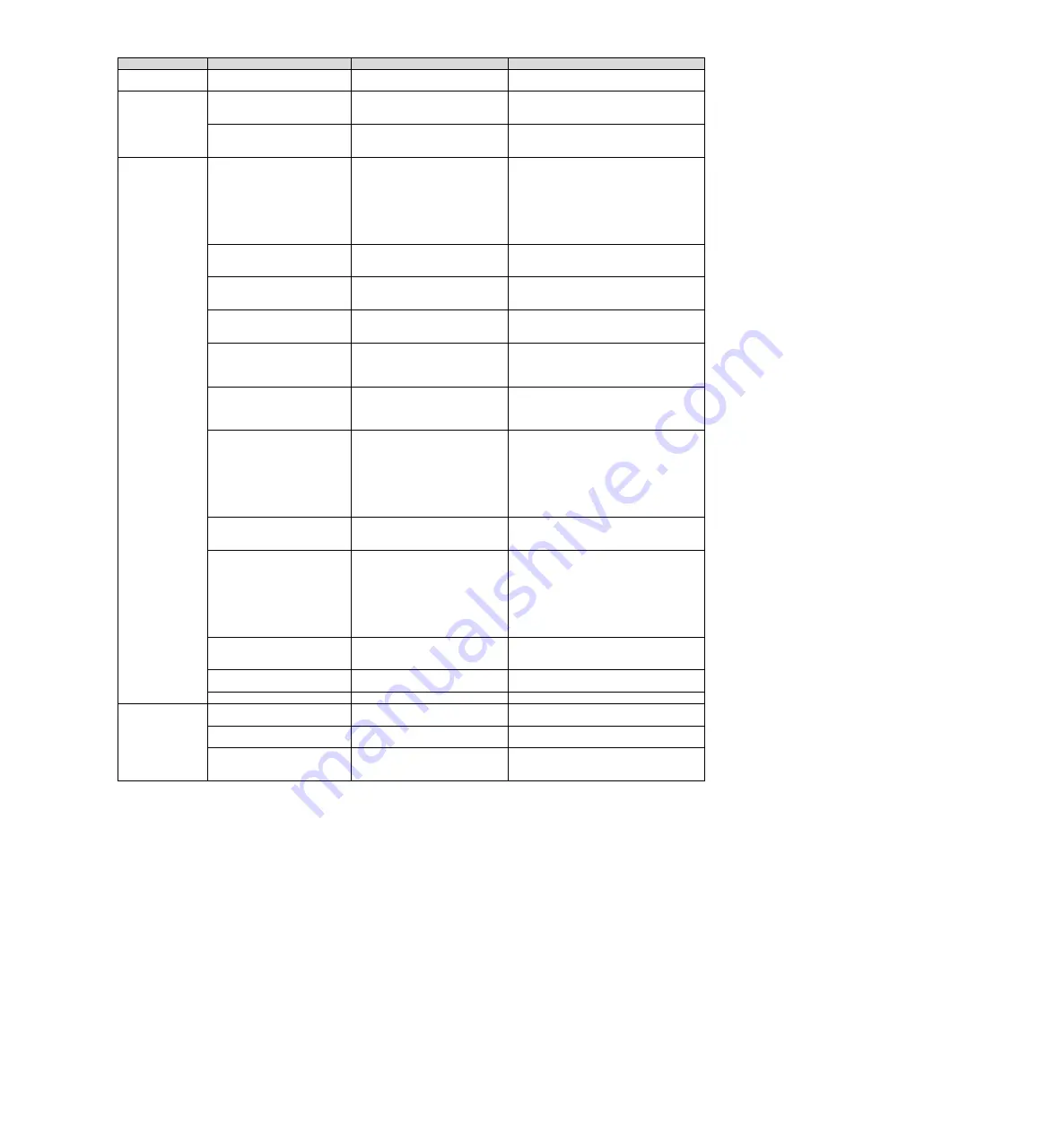
83
Fault contents
Reason
Confirmation method
The treatment measures
torque control (Pn001 = n.
X,
or Pn001 = n.
X
).
than free running stop.
Incorrect
stop
position due to
over travel (OT)
The position of the limit switch
and the length of the toggle
joint are improper
-
Set the limit switch at the appropriate
position.
The position of the overtravel
limit switch is shorter than the
inertia operation amount
-
Set the overtravel limit switch at the
appropriate position.
Position deviation
occurs (No alarm)
Mutual interference occurred
due to incorrect specifications
of cables used for encoders
Confirm whether the cable for
encoder meets the specification
The cable specification: double
stranded shielded wire or double
stranded unified shielded wire with
core wire of more than 0.12mm
2
and tinned soft copper stranded
wire.
Use cables that meet specifications.
Because the encoder cable is
too long, mutual interference
occurs
Confirm the cable length for
encoder.
Set the length of encoder cable within 50m.
Due to encoder cable damage,
mutual interference occurs
Confirm whether the encoder
cable is clamped and the cladding
is damaged.
Replace encoder cable and change cable
laying environment.
Excessive mutual interference
on encoder cable
Verify that the encoder cable is
tied together or too close to the
high current wire.
Change the laying environment of encoder
cables so as not to be affected by surge
voltage of high-current wires.
The potential of FG changes
due to the influence of servo
motor-side equipment (welding
machine, etc.)
Confirm the grounding status of
servo motor side equipment
(forget
grounding,
incomplete
grounding).
Properly ground the servo motor side
equipment to prevent shunt to encoder side
FG.
Error in calculation of servo
drive pulse due to mutual
interference
Confirm whether there is mutual
interference between encoder or
serial conversion unit and signal
line.
Anti-interference measures shall be taken
for the connection of encoder or serial
conversion unit.
Encoder
is
affected
by
excessive vibration impact
Confirm
whether
mechanical
vibration occurs. Confirm the
installation state of servo motor
(precision of installation surface,
fixed
state,
eccentric
core).
Confirm the installation state of
linear encoder (installation surface
precision, fixing method).
Reduce mechanical vibration. And the
installation state of the servo motor or the
linear encoder is improved.
Coupling failure of machine
and servo motor
Verify that the coupling between
the machine and the servo motor
is misaligned.
Correctly fix the coupling of the machine
and servo motor.
Due to the wrong specifications
of the cables used for input and
output
signals,
mutual
interference occurred
Confirm whether the cables for
input and output signals meet the
specifications.
The
cable
specification: double stranded
shielded wire or double stranded
unified shielded wire with core
wire of more than 0.12mm
2
and
tinned soft copper stranded wire.
Use cables that meet specifications.
Due to the long cable used for
input and output signals,
mutual interference occurs.
Confirm the length of cable for
input and output signals.
Make the length of cable for input and
output signals within 3m.
Encoder
failure
(pulse
unchanged)
-
Replace the servo motor or encoder.
Servo drive failure
-
Replace the servo drive.
Servo
motor
overheating
Ambient temperature is too
high
Measure the ambient temperature
of the servo motor.
Set the ambient temperature below 40°C.
Dirty surface of servo motor
Visual inspection confirms motor
surface smudges.
Remove dirt, dust and oil stains on the
motor surface.
The servo motor is overloaded. Confirm the load status through
the monitor.
If overload occurs, reduce the load or
replace it with servo drive and servo motor
with larger capacity.