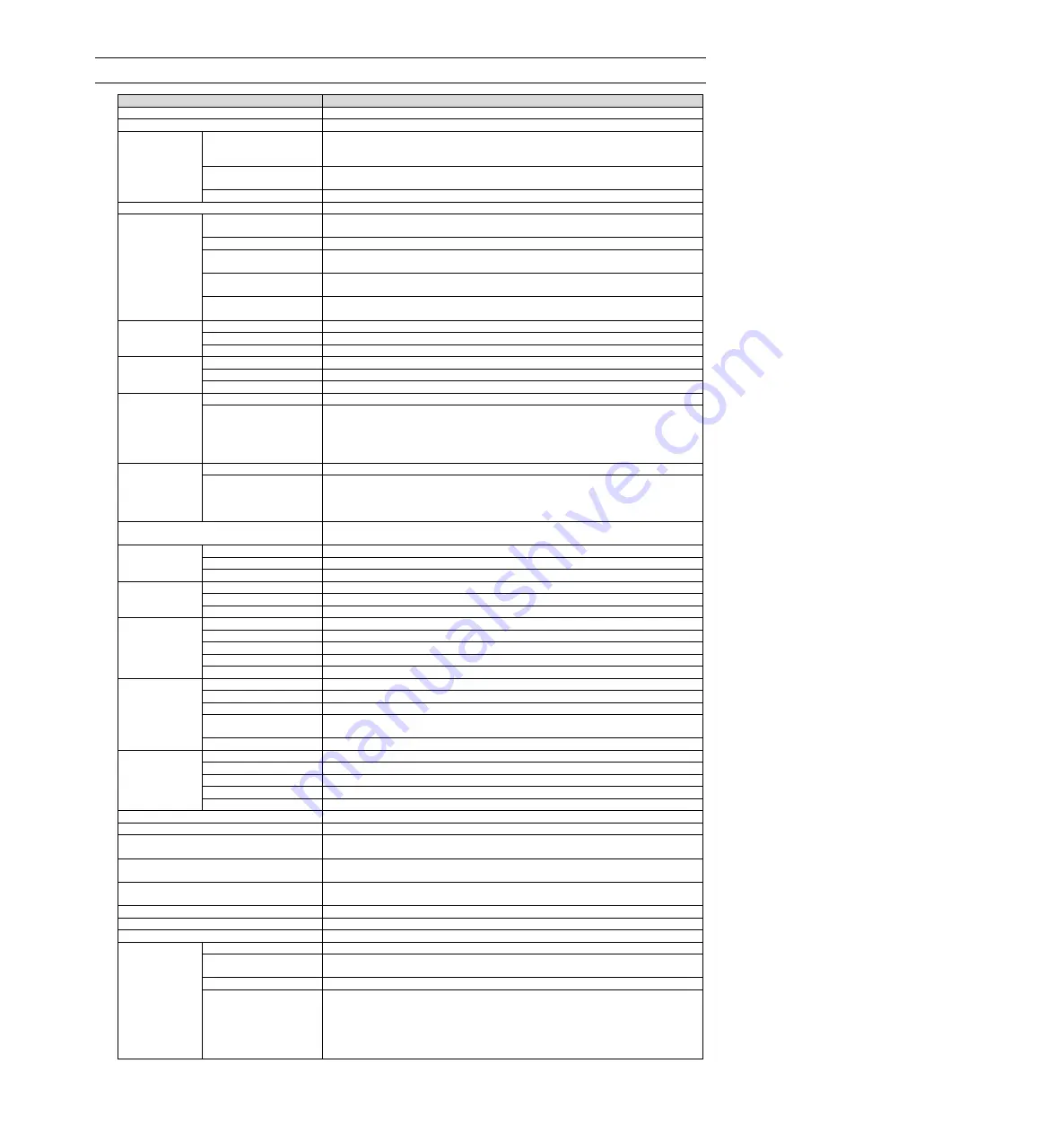
4
2.1.2 Specification table
Item
Specifications
Control model
Position control, JOG operation, Speed contacts, etc.
Encoder feedback
Serial data encoder: 17-bit or 23-bit (single or multiple turns)
Conditions of use
Operating ambient
temperature/storage
temperature
Operating ambient temperature: 0~+50
℃
, storage temperature: -20~+85
℃
Ambient humidity/storage
humidity
Below 90%RH (no freezing or condensation)
Vibration/impact strength
4.9m/s
2
/
19.6m/s
2
Structure
Base mounting type
Performance
Speed control range
1:10000 (the lower limit of the speed control range is stable operation without crawling under rated
load)
Speed response
3.1KHz
Speed Volatility (Load
Change)
0 ~ 100% load: Under ±0.01%(at rated speed)
Velocity fluctuation rate
(voltage change)
Rated voltage ±10%: 0% (at rated speed)
Velocity fluctuation rate
(temperature change)
25±25
℃
:
Below ±0.1%
(
at rated speed
)
Analog speed
command input
Command voltage
DC±10V
Input impedance
Around 20KΩ
Circuit time parameter
47μs
Analog torque
command input
Command voltage
DC±10V
Input impedance
Around 20KΩ
Circuit time parameter
47μs
Sequential control
input signal
Point
8 points
Function (assignable)
Servo ON (/S-ON), P action (/P-CON), prohibition of forward rotation side drive (P-OT), prohibition
of reverse rotation side drive (N-OT), alarm reset (/ALM-RST), forward rotation side torque limit
(/P-CL), reverse rotation side torque limit (/N-CL), position deviation reset (/CLR), internal set
speed switching, etc.
Distribution of the above signals and change of positive/negative logic can be performed
Sequential control
output signal
Point
6 points
Function (assignable)
Servo Alarm (ALM), Positioning Complete (/COIN), Speed Consistent Detection (/V-CMP), Servo
Motor Rotation Detection (/TGON), Servo Ready (/S-RDY), Torque Limit Detection (/CLT), Brake
(/BK), Encoder Zero Output (PGC)
Distribution of the above signals and change of positive/negative logic can be performed
Encoder frequency division pulse output
Phase A, phase B, phase C: linear drive output; Frequency division pulse number: can be
arbitrarily set
RS-485
communication
Communication protocol
MODBUS
1: N communication
The maximum can be N = 127 stops.
Axis address setting
Through parameter setting
CAN communication
Communication protocol
CANOpen (DS301+DS402 line gauge)
1: N communication
The maximum can be N = 127 stops.
Axis address setting
Through parameter setting
MECHATROLINK-
Ⅱ
Bus
Communication protocol
MECHATROLINK-II
Set slave address
41 to 5F (hexadecimal) (maximum number of slave stations supported: 30), via parameter setting
Baud rate
10 Mbps, 4 Mbps, via parameter setting
Transmission period
250 microseconds or 0.5 milliseconds to 4.0 milliseconds (multiples of 0.5 milliseconds)
Number of bytes transferred There are 17 or 32 bytes for each site and the same is set by parameters
MECHATROLINK-
Ⅲ
Bus
Communication protocol
MECHATROLINK-III
Set slave address
03 to EF (hexadecimal) (maximum number of slave stations supported: 62), via parameter setting
Baud rate
100 Mbps
Transmission period
250 microseconds, 500 microseconds, 750 microseconds, or 1.0 milliseconds to 4.0 milliseconds
(multiples of 0.5 milliseconds)
Number of bytes transferred There are 16, 32 or 48 bytes for each site and the same is set by parameters
EtherCAT bus
Communication protocol
CoE (CANOpen over EtherCAT)
Control model
csp, pp, hm, csv, cst, pv, tq
Zero return mode
1-14, 17-30, 33, 34, 35, 37
Synchronization mode
DC, SM2, FreeRun
Minimum command cycle
125 μs
Display function
CHARGE Indicator, 7-segment Digital Tube 5-bit
Regeneration treatment
Internal Regenerative Resistor or External Regenerative Resistor (Optional)
Overtravel (OT) prevention function
Dynamic brake (DB) stops, deceleration stops or free running stops when P-OT and N-OT input
actions are performed.
Protection function
Overcurrent, overvoltage, undervoltage, overload, overspeed, regeneration fault, encoder
feedback error, etc.
Monitoring function
Revolving speed, current position, command pulse accumulation, position deviation, motor
current, running state, input and output signals, etc.
Auxiliary function
Gain adjustment, alarm recording, JOG operation, origin search, inertia detection, etc.
Intelligent function
Built-in Gain Auto Tuning
Applicable load inertia
Less than 5 times of motor inertia
Position control
Feedforward compensation
0 ~ 100% (set unit 1%)
Type of input pulse
pulse sequence, CW+CCW pulse sequence, 90 °phase difference two-phase pulse
(phase A+phase B)
Input pulse form
Support linear drive, open collector
Maximum input pulse
frequency
Linear drive
pulse sequence, CW+CCW pulse sequence: 500K pps
90° phase difference two-phase pulse (phase A+phase B): 500K pps
Open collector
pulse sequence, CW+CCW pulse sequence: 200K pps
90° phase difference two-phase pulse (phase A+phase B): 200K pps