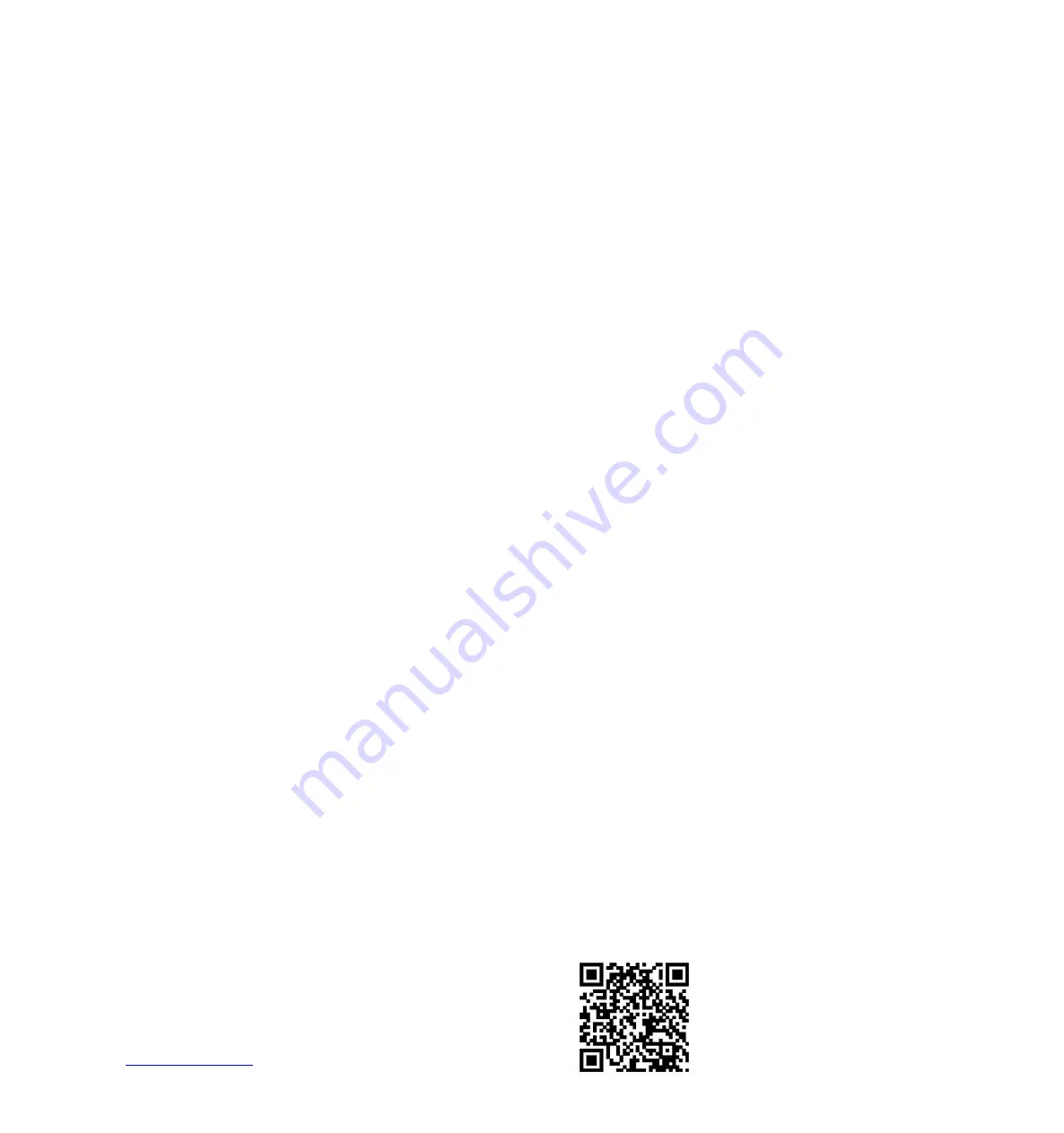
115
Version: V0.1
Thanks for choosing HNC product.
Any technique support, please feel free to contact our support team
Tel: 86(20)84898493 Fax: 86(20)61082610
URL: www.hncelectric.com
Email:
115
Version: V0.1
Thanks for choosing HNC product.
Any technique support, please feel free to contact our support team
Tel: 86(20)84898493 Fax: 86(20)61082610
URL: www.hncelectric.com
Email: