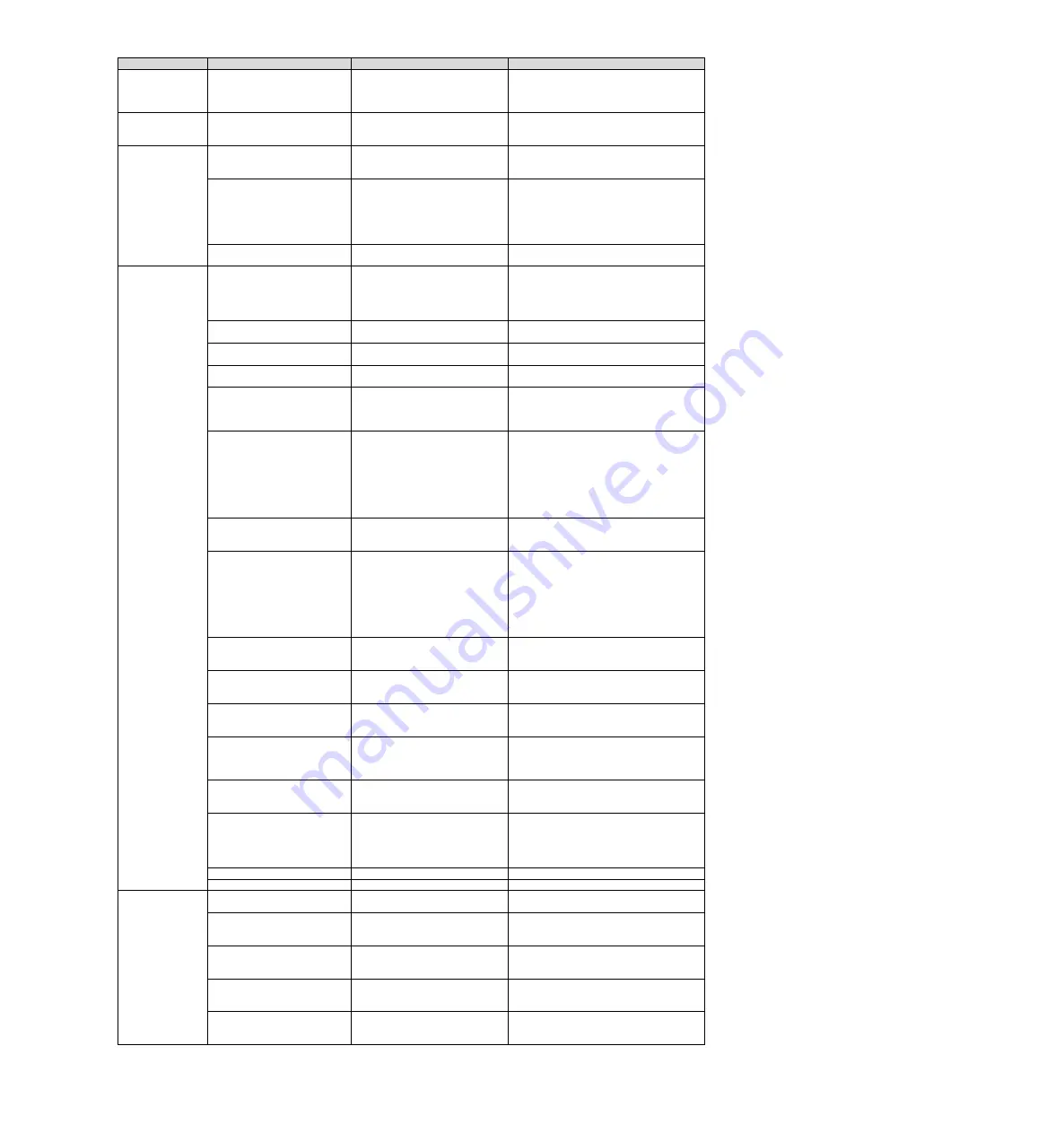
81
Fault contents
Reason
Confirmation method
The treatment measures
The action of servo
motor is not stable
Poor cable connection of servo
motor
The connector connection of
power line (U, V, W phase) and
encoder or serial conversion unit
may be unstable. Confirm wiring.
Looseness of fastening terminals or
connectors and correct wiring.
Servo
motor
running
without command
Servo drive failure
Check whether the directions
match.
Replace the servo drive
Dynamic
brake
(DB)
does
not
operate
Pn00 = n.
X (stop method
when servo OFF and Gr.1
alarm occurs) is improperly set
Confirm the set value of Pn001 =
n.
X.
Properly set Pn001 = n.
X.
DB resistor disconnection
Confirm the moment of inertia,
speed and frequency of use of DB.
It may be that the moment of
inertia, speed, frequency of use of
DB is too large or DB resistance is
broken.
Replace the servo drive. In addition, in
order to prevent disconnection, measures
can be taken to reduce the load state.
DB drive circuit failure
-
DB loop component failure. Replace the
servo drive.
Abnormal sound
from servo motor
When
using
the
adjustment-free
function
(factory setting), the servo
motor vibrates greatly
Confirm the waveform of motor
speed.
Reduce the load below the allowable
rotational inertia ratio or allowable mass
ratio, or increase the load value set without
adjustment value to reduce the rigidity
value.
Poor mechanical installation
Confirm the installation status of
servo motor
Re-tighten the mounting screws.
Poor mechanical installation
Confirm whether the coupling is
eccentric.
Align the core of the coupling.
Internal bearing failure
Confirm the sound and vibration
near the bearing.
Replace the servo motor.
The
vibration
source
is
cooperating with the machine
Confirm whether the moving parts
on the machine side have foreign
bodies entering or damaged or
deformed.
Please contact the machine manufacturer.
Due to the wrong specifications
of the cables used for input and
output
signals,
mutual
interference occurred
Confirm whether the cables for
input and output signals meet the
specifications.
The
cable
specification: double stranded
shielded wire or double stranded
unified shielded wire with core
wire of more than 0.12 mm
2
and
tinned soft copper stranded wire.
Use cables that meet specifications.
Due to the long cable used for
input and output signals,
mutual interference occurs
Confirm the length of cable for
input and output signals.
Make the length of cable for input and
output signals within 3 m.
Due to the wrong specification
of cable for encoder, mutual
interference occurs
Confirm whether the cables for
input and output signals meet the
specifications.
The
cable
specification: double stranded
shielded wire or double stranded
unified shielded wire with core
wire of more than 0.12 mm
2
and
tinned soft copper stranded wire.
Use cables that meet specifications.
Because the encoder cable is
too long, mutual interference
occurs
Confirm the cable length for
encoder.
Set the length of encoder cable within 50m.
Due to encoder cable damage,
mutual interference occurs
Confirm whether the encoder
cable is clamped and the cladding
is damaged.
Replace encoder cable and change cable
laying environment.
Excessive mutual interference
on encoder cable
Verify that the encoder cable is
tied together or too close to the
high current wire.
Change the laying environment of encoder
cables so as not to be affected by surge
voltage of high-current wires.
The potential of FG changes
due to the influence of servo
motor side equipment (welding
machine, etc.)
Confirm the grounding status of
servo motor side equipment
(forget
grounding,
incomplete
grounding).
Properly ground the servo motor side
equipment to prevent shunt to encoder side
FG.
Pulse calculation error of servo
drive
caused
by
mutual
interference
Confirm whether there is mutual
interference between encoder and
signal line
Properly ground the servo motor side
equipment to prevent shunt to encoder side
FG.
Encoder
is
affected
by
excessive vibration and shock
Confirm
whether
mechanical
vibration occurs. Confirm the
installation state of servo motor
(precision of installation surface,
fixed state, eccentric core).
Reduce mechanical vibration. Improve the
installation state of servo motor.
Encoder failure
-
Replace the servo motor
Serial conversion unit failure
-
Replace the serial conversion unit.
When the
frequency is about
200
~
400Hz, the
motor
vibrates
Improper matching of servo
gain
Confirm whether gain adjustment
has been implemented.
Perform automatic adjustment (no upper
command).
The speed loop gain (Pn100) is
set too high.
Confirm the setting value of speed
loop
gain
(PN100).
Factory
setting: Kv = 40.0 Hz
Set the correct speed loop gain (Pn100)
setting.
The set value of the position
loop gain (Pn102) is too high
Confirm the set value of position
ring gain (Pn102). Factory setting:
Kp = 40.0/s
Set the correct setting value of position
loop gain (Pn102).
The speed loop integration
time parameter (Pn101) is not
set correctly
Confirm the set value of integral
time parameter (Pn101) of speed
loop. Factory setting: Ti = 20.0 ms
Set the correct speed loop integration time
parameter (Pn101) setting value.
The setting value of rotational
inertia ratio or mass ratio
(Pn103) is incorrect
Confirm the set value of the
moment of inertia ratio or mass
ratio (Pn103)
Set the correct moment of inertia or mass
ratio (Pn103).