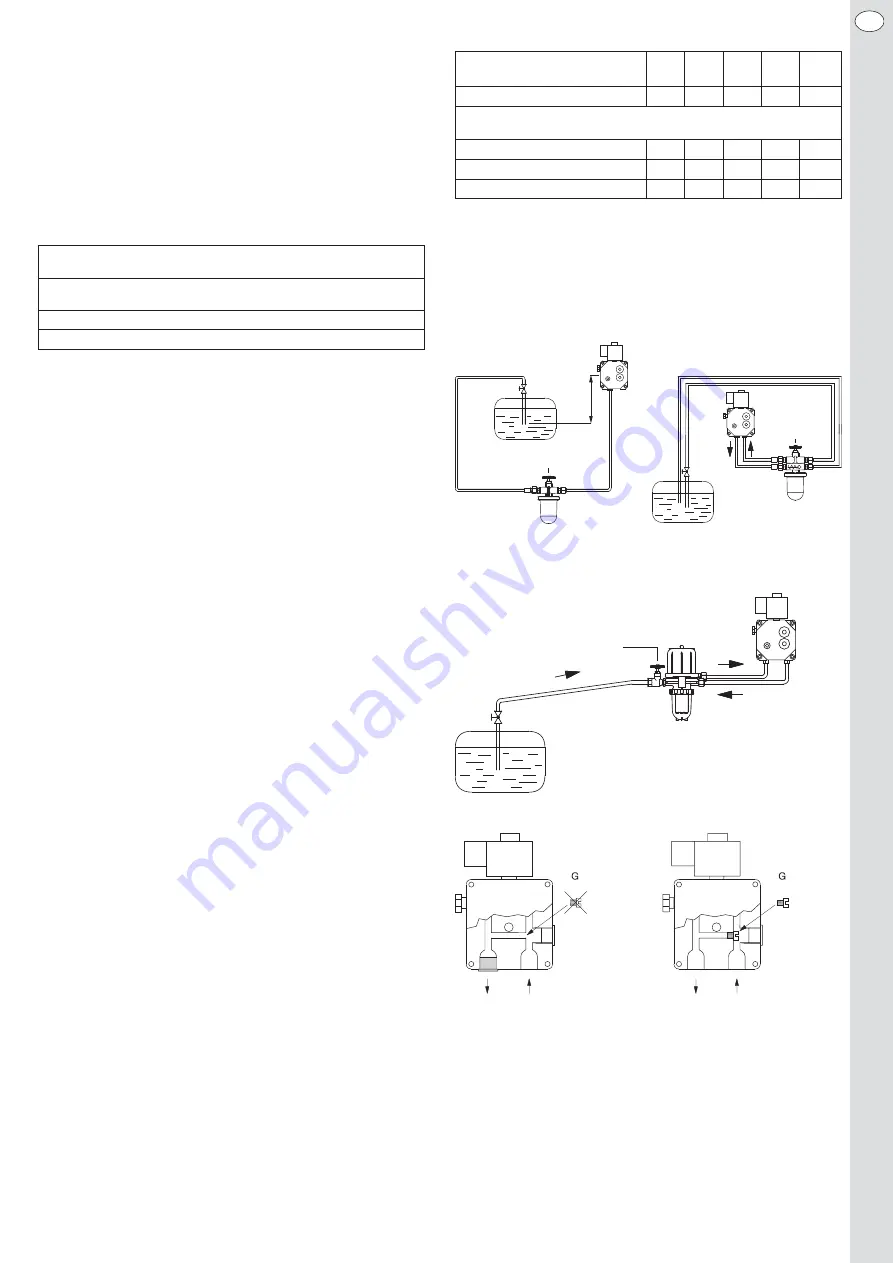
27
The burner must be connected in accordance with DIN 4791:1985-09
using a 7-pole Euro plug. Wiring details are provided in the wiring diagram
in chapter 6. The factory will deliver the burner together with the Euro
connector (female plug). The Euro connector male plug is not included in
the scope of delivery. For burners with cover hood, the cables are inserted
through a rubber grommet in the base plate, where the oil tubes are
inserted as well.
3.3 Combustion chamber - minimum dimensions
In order to ensure reliable operation and low pollutant emissions, the
geometry of the combustion chamber must meet the test flame tube
standards according to DIN EN 267:2011-11.
3.4 Exhaust gas system
The burner is designed for operation dependent on ambient air as well as
for operation independent of ambient air. For operation dependent on am-
bient air we recommend the installation of a draft limiter into the flue gas
system in order to ensure constant pressure in the combustion chamber.
The low pressure in the combustion chamber which can be adjusted on
the draft limiter should be –0.1mbar compared to the ambient pressure.
The flue draft to be adjusted for overpressure boilers is provided in the
boiler manual.
For operation independent of ambient air, the burner can be connected
to the air exhaust separator of an air exhaust system using optional air in-
take connection pieces (Ø 50mm and Ø 80mm). For operation indepen-
dent of ambient air, no draft limiter may be installed into the exhaust pipe.
Furthermore, you must ensure that the heating boiler used is suitable for
the selected exhaust gas system with regard to exhaust gas composition
and exhaust gas temperatures.
The relevant applicable local provisions regarding the exhaust gas system
must also be taken into consideration.
3.5 Oil supply system, oil pipe dimensions
The burner can optionally be operated as a pure one-line system, a one-
line system with filter-aspirator combination (the pump is operated simi-
larly to a two-line system), or a two-line system.
The burner is preset for a two-line system as a standard. When converting
the pump to one-line operation, make sure to seal the return piece with a
sealing plug and remove the shift screw in the junction canal between the
pressure and intake side.
In order to avoid any malfunction of the burner caused by the oil supply
system, we recommend operating the burner in a pure one-line system
with filter-aspirator combination. The following points should be con -
sidered:
• Maximum intake height without booster pump: 3.5m
• Up to a nominal thermal output of the boiler of 50kW, we recommend
an oil pipe with an internal diameter of 4mm for the one-line system
with filter-aspirator combination.
• The pipes should be arranged such that the boiler together with the bur-
ner can be swiveled out by 90°.
• Upstream of the flexible oil pipes, you must install a valve at the end of
the rigid oil pipe (already integrated in commercial filter-aspirator com-
binations).
• A filter-aspirator combination must be installed upstream of the burner.
Insert of sintered plastic 20-75 μm for boiler capacities of up to 40 kW,
for boiler capacities >40 kW sieve with 100-150 μm of fineness.
• The highest point of the oil pipe should not exceed 3.5m above the end
of the intake pipe of the tank.
• The pipes must be installed in such a manner that no liquid may be
allowed to escape (raise) from the container.
• If the highest level of the fuel in the oil tank is above the oil pump of the
burner, you must install an anti-lifter valve at the highest point of the oil
pipe and as close as possible to the oil tank.
• The oil pipe and the connection to the burner must meet the current
provisions. It is absolutely imperative that you check the existing oil
supply as from the time of oil tapping from the oil tank.
Combustion chamber minimum dimensions according to
DIN EN 267:2011-11
Oil flow
Diameter or
Depth from the
height and width
baffle plate
1.0 - 2.0 kg/h
Ø 225 mm
250 - 350 mm
2.0 - 6.0 kg/h
Ø 300 mm
350 - 612 mm
* H = max. intake height in m (low sulphur fuel oil EL, oil temperature
>10 °C, up to 700 m above sea level, 1 filter, 1 check valve, 6x 90 °
bends).
For other system requirements (intake height, pipe lengths and nominal
thermal output of the boiler), you should consider the following diagrams
for pipe dimensioning.
Oil supply system
One-line system Pure two-line system
One-line system with filter-de-aerator combination
Setting at the fuel pump for one-line and two-line system
Absperreinrichtung
Filter-Entlüfter -
Kombination
Einstrang-
system
Zweistrang-
system
Absperreinrichtung
Filter
Absperr-
einrichtung
Filter
H
max
=
3,5 m
EN
Nominal thermal output of the
boiler in kW
16
20
25
35
50
Internal pipe Ø in mm
4
4
4
4
4
H* in m
max. zulässige
Leitungslänge in m:
0
30
30
30
30
20
1
30
30
30
23
15
2
30
28
23
16
10
Valve system
Valve system
Valve system
One-line
system
Two-line
system
Filter-de-aerator
combination
Содержание HL 60 ALV.2
Страница 15: ...15 DE 7 Explosionszeichnung mit Ersatzteilliste...
Страница 20: ...20 DE 9 Brennerabmessungen HL 60 ALV 2 BLV 2 Schiebeflansch HL 60 ALV 2 BLV 2 Unitflansch...
Страница 21: ...21 DE 9 Brennerabmessungen HL 60 ELV 2 S FLV 2 S Schiebeflansch HL 60 ELV 2 S FLV 2 S Unitflansch...
Страница 33: ...33 EN 7 Expanded view with spare parts list...
Страница 38: ...38 EN 9 Burner dimensions HL 60 ALV 2 BLV 2 sliding flange HL 60 ALV 2 BLV 2 unit flange...
Страница 39: ...39 EN 9 Burner dimensions HL 60 ELV 2 S FLV 2 S sliding flange HL 60 ELV 2 S FLV 2 S unit flange...
Страница 51: ...51 FR 7 Vue clat e avec liste des pi ces de rechange...
Страница 56: ...56 FR 9 Dimensions du br leur HL 60 ALV 2 BLV 2 Bride coulissante HL 60 ALV 2 BLV 2 Bride unitaire...
Страница 57: ...57 FR 9 Dimensions du br leur HL 60 ELV 2 S FLV 2 S Bride coulissante HL 60 ELV 2 S FLV 2 S Bride unitaire...
Страница 69: ...69 IT 7 Disegno esploso con elenco parti di ricambio...
Страница 74: ...74 IT 9 Dimensioni bruciatore HL 60 ALV 2 BLV 2 Flangia scorrevole HL 60 ALV 2 BLV 2 Flangia unitaria...
Страница 75: ...75 IT 9 Dimensioni bruciatore HL 60 ELV 2 S FLV 2 S Flangia scorrevole HL 60 ELV 2 S FLV 2 S Flangia unitaria...