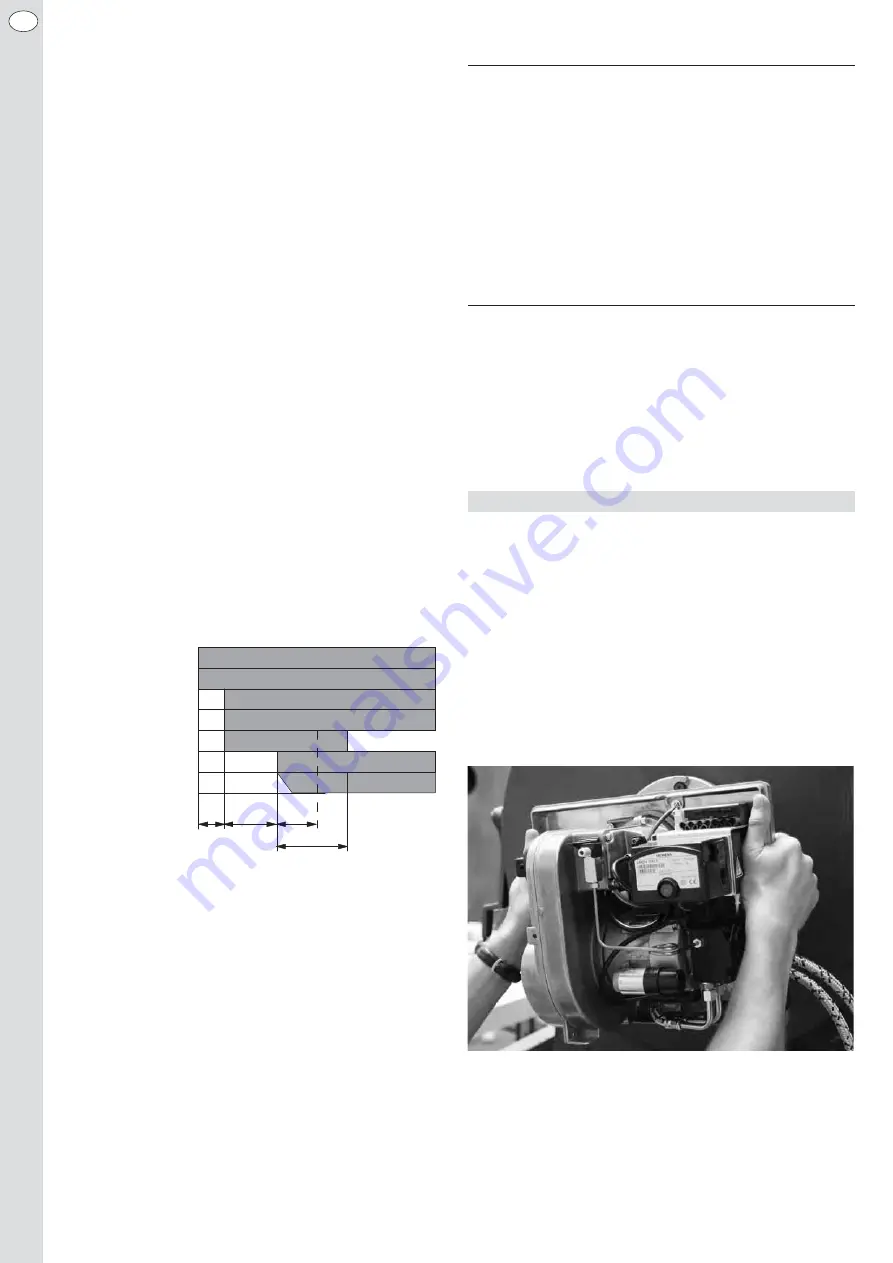
26
2.6 Oil firing unit
For the control and monitoring of the burner operation, the electromag-
netic firing unit Siemens LOA 24 (approval according to DIN EN 230:1991)
or the electronic firing unit Siemens LMO 14 (approval according to DIN
EN 230:2005) is used. Both firing units can be combined with the above
mentioned flame monitoring devices Danfoss LDS blue and Danfoss LDS
red. The main difference of the program sequence of both firing units is
the program time. The advantages of electronic firing units compared to
electromechanical firing units is the convenient display of status and error
messages using a flashing code, as well as the optional electrical remote
unlocking.
The starting sequence of the burner begins once the boiler thermostat
is closed and voltage is applied to terminal T2 of the Euro connector. In
this switching state, the oil pre-heater is supplied with voltage through
terminal 8 (see chapter 6). As soon as the pre-heating phase (release
time at an output temperature of 31°C: 145 s) is completed, the thermo-
stat in the oil pre-heater closes; now voltage is applied at terminal 3 and
the motor starts. At the same time, the firing unit starts the pre-aeration
time with pre-ignition. If there is no flame after the pre-aeration phase,
the control device opens the magnetic valve of the oil pump and fuel is
injected. However, if there is a flame or extraneous light after the pre-
aeration phase, the device is switched off and the the firing unit is
locked. Electromechanical firing units (Siemens LOA 24) can only be
unlocked after the bimetal has cooled down (approx. 50s after fault shut-
down). There is no such waiting time for electronic firing units (Siemens
LMO 14).
From fuel release, the ignition remains activated for a further period of
time (retarded ignition). In case of normal start-up, the flame is generated
within the safety period. The burner remains switched on until the boiler
thermostat opens and the voltage at terminal T2 drops. However, if no
flame is generated within 10s after fuel release (safety time) or it
extinguishes within this period of time, the magnetic valve of the fuel
pump is closed and the burner is locked. There is no automatic restart.
For restart, the reset push-button of the firing unit must be pressed.
However, if the flame extinguishes after the end of the safety time, the
firing unit makes a restart with pre-aeration and pre-ignition.
The oil firing unit is protected against low voltage. If mains voltage falls
below 165V, the burner is not started, or a fault shut-down is triggered
during operation. A minimum voltage of 175V is required to initialise the
starting sequence.
Program sequence for firing units
In case of fault shut-down, all outputs for fuel valves, burner motor and
ignition device are immediately (<1s) switched off. After fault shut-down,
the firing unit remains locked and the fault warning light is permanently
red. This condition also remains if the voltage is disconnected from the
mains.
The electronic firing unit LMO14 is also equipped with a visual operating
display and fault cause diagnosis which is indicated by the multi-coloured
LED (red/yellow/green) on the unlocking button.
Heat request
Oil pre-heater
Oil pre-heater thermostat
Burner motor
(blower/pump)
Ignition
Magnet valve
Flame signal
th
ts
tpoi
tprp,tpri
Siemens
Siemens
LMO 14
LOA 24
th
Heating time of the oil pre-heater –
–
tprp Pre-aeration
15 s
13 s
tpri Pre-ignition
15
s
13
s
tpoi Retarded ignition
10 s
20 s
ts
Safety time
10 s
10 s
Operating mode
LED flashing code
Waiting time
off
Oil pre-heater is heating up
yellow
permanently
Ignition phase, ignition controlled
yellow
flashing
Operation, flame OK
green
permanently
Operation, poor flame
green
flashing
Extraneous light after burner start
green-red
flashing
Low voltage
yellow-red flashing
Fault, alarm
red
permanently
Issue fault code
red
flashing
PC interface diagnosis (specialist)
red
flickering
After the fault shut-down of the electronic firing unit LMO14 and when the
fault warning light LED is permanently red, the visual fault cause diagnosis
can be activated by pressing the unlocking button >3s. During the fault
cause diagnosis, the control outputs are de-energised and the burner re-
mains switched off.
Fault cause
LED flashing code
No flame generation at the end of the
safety time
red
2x flashing
Extraneous light after burner start
red
4x flashing
Flame interruption during operation too
frequently (repetition limit)
red
7x flashing
Time monitoring of oil pre-heater
red
8x flashing
Wiring error or internal error,
permanent error of output contacts,
other errors
red
10x flashing
Quit the fault cause diagnosis and restart the burner by briefly pressing
the unlocking button once for approx. 1s (<3s).
3.
Commissioning
3.1 Assembly of the burner
Sliding flange version:
– Mount sliding flange including sealing onto the heat generator using the
supplied M8 screws. The clamping screw of the sliding flange must be
positioned upwards.
– Insert burner with burner pipe into the flange until the burner pipe is
flush with the inside of the combustion chamber. Observe special
instructions of the heat generator manufacturer, if any.
– Tighten the clamping screw of the flange clamp.
Unit flange version:
– Mount unit flange with burner pipe including sealing onto the heat
generator using the supplied M8 screws. Position the wedge-shaped
unit flange such that the thicker side points downwards.
– Insert burner without burner pipe into the flange and fix it with a service
screw.
3.2 Electricity supply
The relevant provisions of VDE (Association of German Electrical Engi-
neers), SEV (Swiss Association of Electrical Engineers) and/or ÖVE (Aus-
trian Association of Electrical Engineers) must be observed for the elect-
rical installations. Power supply: 230V~ 50Hz 10A. An all-phase load
switch according to VDE, SEV, ÖVE with a contact opening of at least
3mm must be used as main switch S1.
EN
Содержание HL 60 ALV.2
Страница 15: ...15 DE 7 Explosionszeichnung mit Ersatzteilliste...
Страница 20: ...20 DE 9 Brennerabmessungen HL 60 ALV 2 BLV 2 Schiebeflansch HL 60 ALV 2 BLV 2 Unitflansch...
Страница 21: ...21 DE 9 Brennerabmessungen HL 60 ELV 2 S FLV 2 S Schiebeflansch HL 60 ELV 2 S FLV 2 S Unitflansch...
Страница 33: ...33 EN 7 Expanded view with spare parts list...
Страница 38: ...38 EN 9 Burner dimensions HL 60 ALV 2 BLV 2 sliding flange HL 60 ALV 2 BLV 2 unit flange...
Страница 39: ...39 EN 9 Burner dimensions HL 60 ELV 2 S FLV 2 S sliding flange HL 60 ELV 2 S FLV 2 S unit flange...
Страница 51: ...51 FR 7 Vue clat e avec liste des pi ces de rechange...
Страница 56: ...56 FR 9 Dimensions du br leur HL 60 ALV 2 BLV 2 Bride coulissante HL 60 ALV 2 BLV 2 Bride unitaire...
Страница 57: ...57 FR 9 Dimensions du br leur HL 60 ELV 2 S FLV 2 S Bride coulissante HL 60 ELV 2 S FLV 2 S Bride unitaire...
Страница 69: ...69 IT 7 Disegno esploso con elenco parti di ricambio...
Страница 74: ...74 IT 9 Dimensioni bruciatore HL 60 ALV 2 BLV 2 Flangia scorrevole HL 60 ALV 2 BLV 2 Flangia unitaria...
Страница 75: ...75 IT 9 Dimensioni bruciatore HL 60 ELV 2 S FLV 2 S Flangia scorrevole HL 60 ELV 2 S FLV 2 S Flangia unitaria...