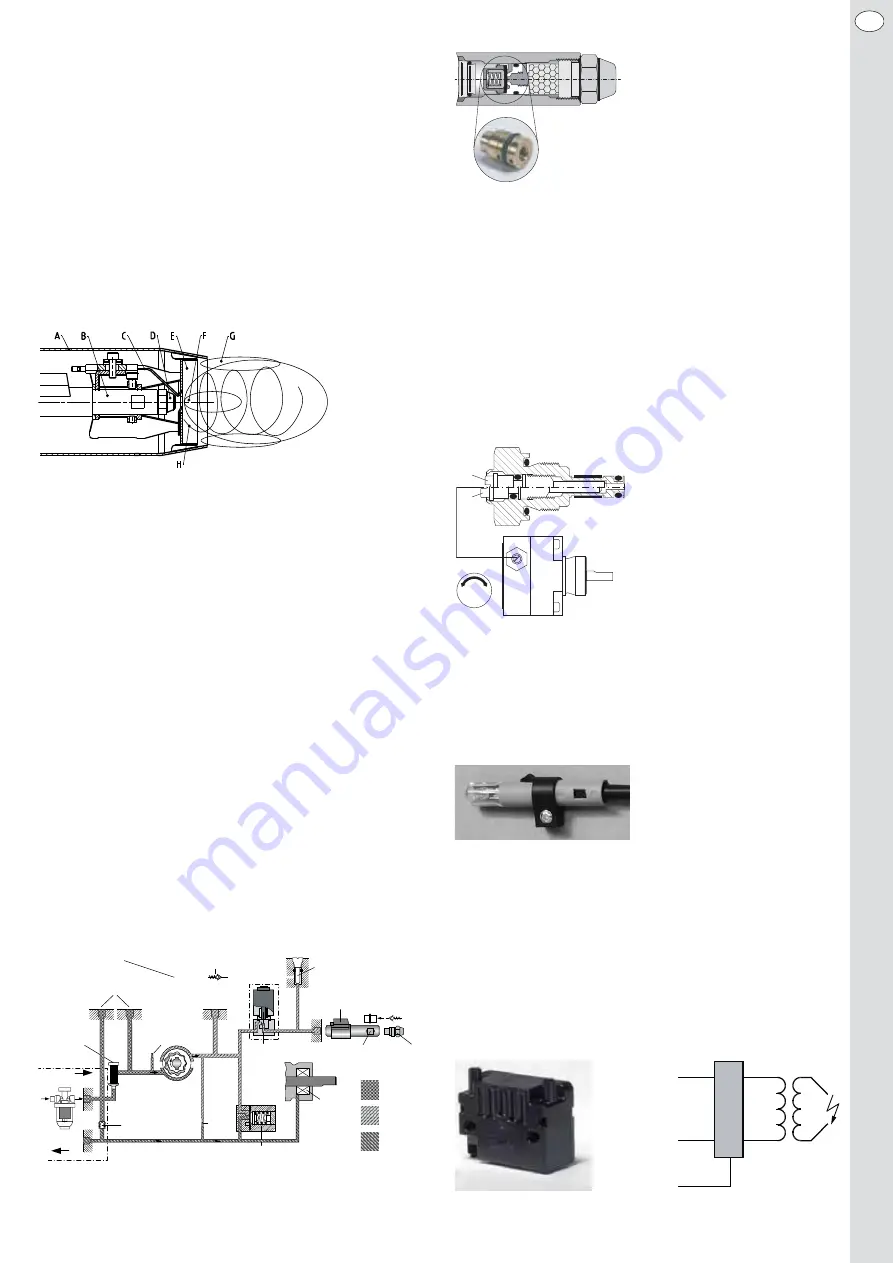
25
In this process, the baffle plate separates the combustion air into three
air flows. The centrally flowing primary air supplies the flame root with
combustion air. Secondary air is made rotate by radially arranged and po-
sitioned slots in the baffle plate in order to provide the continuous mixing
and distribution of combustion air with finest fuel fog. The third air flow
through the circular orifice between burner tube and baffle plate supplies
combustion air to the flame coat.
The flow speed as well as the back pressure in the mixing unit, among
others, can be influenced by adjusting the pressure panel position in the
burner tube.
Depending on the combustion capacity, a 4-slot or 12-slot baffle plate
is provided for the mixing device. For standard burner models, these
baffle plates are combined with a burner tube with a conically shaped
nozzle piece (mixing system A and B). Nitrogen oxide emissions are
further reduced by additionally swirling the tertiary air flowing in through
the outer edge of the baffle plate. To this end, the burner tube is provided
with slanted guide arms at the conical nozzle piece. Moreover, the air
flow is guided via an air-flow breakaway edge which is positioned
vertically to the direction of flow. Such a burner tube combined with both
baffle plates makes up the mixing systems E and F.
A
Burner tube
B Oil
pre-heater
C Ignition elec -
trodes
D Oil
nozzle
E baffle
plate
F Initial air to the
flame root
G Tertiary air to
the flame coat
H Secondary
air
swirled for
mixing
2.2 Combustion air blower
Combustion air is delivered through a patented hybrid blower which
features extremely high compressive strength. This ensures the start-up
of the burner without pulsation and delays, in particular in the case of
high combustion chamber backpressures. In comparison with con -
ventional blower solutions, the high degree of efficiency of the blower
results in the significant reduction of electric energy consumption.
For operation dependent on ambient air, the protective cover at the
blower inlet can be replaced by a intake air silencer which is available
as an accessory. Intake ports with Ø 50mm or Ø 80mm are available for
operation independent of ambient air. Moreover, a pivoted intake port
with Ø 50mm is offered which can be combined with an upstream
silencer.
2.3 Fuel pump and nozzle closing system
A gear wheel pump is used as fuel pump. The picture shows the hydrau-
lic diagram of a 1-stage fuel pump. The gear wheel set of the pump
delivers fuel from a storage tank of the the oil supply system through a
cartridge filter to the oil nozzle. The required injection pressure is adjus-
ted with a pressure control valve. A magnetic valve is provided for the
control of the injection process. If no power is applied, the magnetic
valve is closed. In this switching status, the whole fuel flows back
through the pressure control switch to the storage tank. For fuel
injection, power is supplied to the magnetic valve and it opens up. Now
fuel flows to the nozzle with the pressure set at the pressure control
valve.
In order to reduce start-up and switch-
off emissions, burner models with mixing
units E and F are equipped with a Dan-
foss nozzle closing system (LESystem)
as a standard. To this end, a spring-
loaded diaphragm valve is installed in
the oil pre-heater which opens at an oil
pressure of approximately 5 bar and is
closed by spring force at approximately
3 bar. In order to accelerate the closing
process of the valve when switching off the burner and to prevent the
increase of pressure in the nozzle line by external influences (e.g. fuel pre-
heating for burner start-up, combustion chamber radiation after burner
switch-off), respectively, the LE oil pump is equipped with a bypass
channel between pressure and intake side for pressure release. A spring-
loaded pressure relief valve with an opening pressure of 2 bar is integrated
in the bypass channel. Due to temperature-related volumetric expansion,
the pressure in the oil pre-heater increases. As soon as the pressure
exceeds 2 bar, the pressure relief valve in the bypass channel of the pump
opens. However, the diaphragm valve in the pre-heater remains closed
due to the higher opening pressure thus preventing fuel from escaping.
After the pre-heating phase, the burner motor is started resulting in
pressure generation within the pump up to the value set at the pressure
controller. After pre-aeration, the magnetic valve is opened. The injection
pressure which builds up in the oil pre-heater opens the diaphragm valve.
Thus, the injection process is started in a controlled way at the opening
pressure given by the diaphragm valve. As the pressure drop at the dia-
phragm valve can be neglected, the pressure at the oil nozzle is equivalent
to the pressure measured at the pump. In order to keep the partial flow
through the bypass during the operation
of the burner as low as possible, an ad-
ditional cover plate is integrated in the
bypass channel. As soon as the burner
switches off, the magnetic valve closes
and the injection pressure is relieved
through the nozzle. As soon as the pres-
sure falls below 3 bar, the diaphragm
valve in the oil pre-heater is closed. This
ensures the controlled end of the in-
jection process without delayed dripping.
The LE oil pump can also be used as
standard oil pump. The LE system can
be activated and/or deactivated by tur-
ning the setting screw (see illustration).
2.4 Flame monitoring
Flame monitoring for HL60 A/B/E/F is implemented with flame sensors of
different degrees of sensitivity especially suited for oil burners with yellow
flame.
Optical flame detectors, LDS blue and LDS red
The Danfoss light-depending resis-
tance sensor (photo conductive cell)
LDS is used for flame monitoring. If
constant voltage is applied, a
changing current depending on the in-
tensity of flame radiation can be mea-
sured which is referred to as photoelectric current. There are two designs
depending on sensitivity. The low-sensitive Danfoss flame sensor LDS red
(red sensor housing) is used for flames with intensive yellow colour and
thus with a high degree of radiation for the mixing devices A and B. The
more transparent flames of the emission-optimised mixing devices E and
F require the use of the high-sensitive Danfoss flame sensor LDS blue
(blue sensor housing).
2.5 Ignition device
The ignition of the mixture by means of a separate ignition device (Danfoss
EBI 4). An earth connection is provided in the primary connection socket
to achieve low electromagnetic interference emissions, i.e. the connection
socket has 3 poles (phase, neutral wire and earth).
Blue, N
Secondary
voltage:
15 kV
Brown, voltage
supply, L1
Ignition
"On": 230 V AC
"Off": 0 V
PE, earthing
50/60 Hz
20 kHz
EN
Ì>iÊÃ`i
*ÀiÃÃÕÀiÊÃ`i
,iÌÕÀÊvÜ
Þ«>ÃÃÊV >i
i>ÃÕÀ}Ê«ÕÌÊ>ÌÊ
Ì
iÊ«ÀiÃÃÕÀiÊÃ`i
i>ÃÕÀ}Ê«ÕÌÊ>ÌÊ
Ì
iÊÌ>iÊÃ`i
ÛiÀÊ«>Ìi
ÛiÀÊ
«>Ìi
>ÀÌÀ`}iÊvÌiÀ
-iÌÌ}ÊÃVÀiÜÊvÊÌ
iÊ
ÊÃÞÃÌi
"Ê«Ài i>ÌiÀ
"Êââi
>«À>}ÊÛ>ÛiÊ
«ÊrÊxL>À
- >vÌÊÃi>
*ÀiÃÃÕÀiÊÛ>Ûi
*ÀiÃÃÕÀiÊÀiivÊÛ>ÛiÊ«ÊrÊÓL>À
>}iÌVÊÛ>Ûi
V}ÊÃVÀiÜÊvÀÊ
ÃÜÌV
}ÊvÀÊiiÊ
«iÀ>ÌÊÌÊÌÜiÊ
«iÀ>Ì
iVÌÊ
ÊÃÕ««ÞÊ
Hydraulic diagram of 1-stage oil pumps
Mixing device
ON
OFF
ON
OFF
LE
Activation / deactivation
of the LE system
LE
diaphragm
valve
Содержание HL 60 ALV.2
Страница 15: ...15 DE 7 Explosionszeichnung mit Ersatzteilliste...
Страница 20: ...20 DE 9 Brennerabmessungen HL 60 ALV 2 BLV 2 Schiebeflansch HL 60 ALV 2 BLV 2 Unitflansch...
Страница 21: ...21 DE 9 Brennerabmessungen HL 60 ELV 2 S FLV 2 S Schiebeflansch HL 60 ELV 2 S FLV 2 S Unitflansch...
Страница 33: ...33 EN 7 Expanded view with spare parts list...
Страница 38: ...38 EN 9 Burner dimensions HL 60 ALV 2 BLV 2 sliding flange HL 60 ALV 2 BLV 2 unit flange...
Страница 39: ...39 EN 9 Burner dimensions HL 60 ELV 2 S FLV 2 S sliding flange HL 60 ELV 2 S FLV 2 S unit flange...
Страница 51: ...51 FR 7 Vue clat e avec liste des pi ces de rechange...
Страница 56: ...56 FR 9 Dimensions du br leur HL 60 ALV 2 BLV 2 Bride coulissante HL 60 ALV 2 BLV 2 Bride unitaire...
Страница 57: ...57 FR 9 Dimensions du br leur HL 60 ELV 2 S FLV 2 S Bride coulissante HL 60 ELV 2 S FLV 2 S Bride unitaire...
Страница 69: ...69 IT 7 Disegno esploso con elenco parti di ricambio...
Страница 74: ...74 IT 9 Dimensioni bruciatore HL 60 ALV 2 BLV 2 Flangia scorrevole HL 60 ALV 2 BLV 2 Flangia unitaria...
Страница 75: ...75 IT 9 Dimensioni bruciatore HL 60 ELV 2 S FLV 2 S Flangia scorrevole HL 60 ELV 2 S FLV 2 S Flangia unitaria...