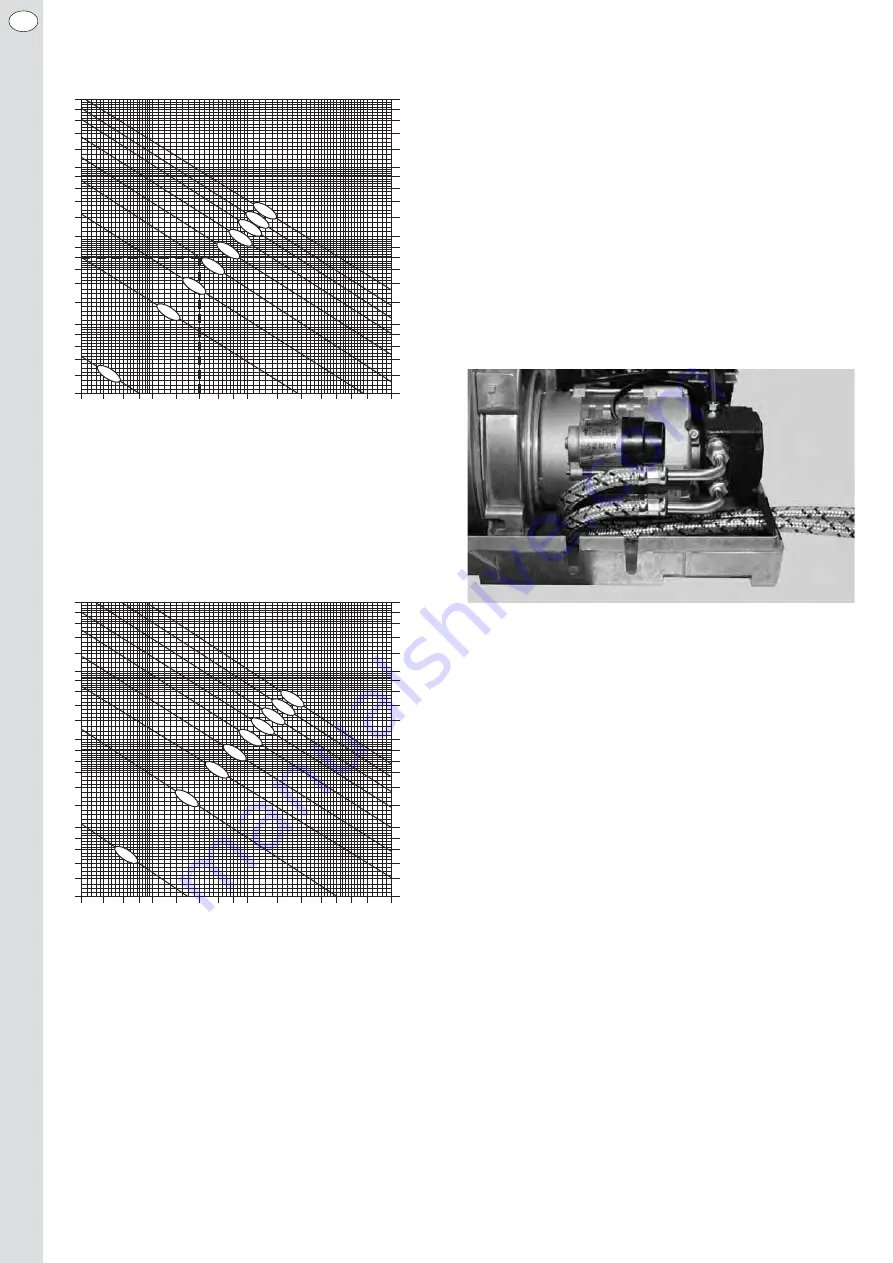
28
Reading sample:
Given:
Flow rate 4 l/h, intake height 1m
Wanted:
Max. possible uncoiled length of intake pipe
Solution:
From the diagram
14 m
+ = height of admission; − = height of intake
Note:
If the pipe dimensioning is not sufficient for intake operation (i.e. the intake
pipe is longer than indicated in the pipe dimensioning diagram), you
should use a booster pump. The oil pipe must not be enlarged.
Applicable for:
Extra light fuel oil, up to 700m above sea level; maximum
pipe length: 30m
The diagram includes:
1 filter, 1 check valve, 6x 90° bends, 40mbar
De-aeration of the oil supply system
For the de-aeration of the oil supply system we recommend the con-
nection of an intake pump at the low pressure measuring connection of
the pump. If only low amounts of air are present in the oil supply, there is
no need of de-aeration with an external intake pump. Instead, you must
run the burner with slightly opened lock screw for the pressure measure-
ment connection until de-aerated and thus foam-free oil escapes from
[l/h]
20
18
16
14
12
10
9
8
7
6
5
4,5
4
3,5
3
2,5
2
1,8
1,6
1,4
1,2
1
6 7 8 9 10 12
14
16 18 20
25 30 40
50 60 [m]
[m/s]
0,442
0,398
0,354
0,310
0,243
0,221
0,199
0,177
0,155
0,133
0,111
0,100
0,088
0,077
0,066
0,055
0,044
0,039
0,035
0,030
0,026
0,022
+4 m
+3 m
+2 m
+1 m
+/-0m
–1 m
–2 m
–3
m
–4 m
Uncoiled length of intake pipe
Dimensioning diagram for intake pipes, dimension Ø 4/6 mm
Range of application: 1-10 liters/h, oil temperature: > 0-10 °C (indoor tank)
[l/h]
20
18
16
14
12
10
9
8
7
6
5
4,5
4
3,5
3
2,5
2
1,8
1,6
1,4
1,2
1
6 7 8 9 10 12
14
16 18 20
25 30 40
50 60 [m]
[m/s]
0,442
0,398
0,354
0,310
0,243
0,221
0,199
0,177
0,155
0,133
0,111
0,100
0,088
0,077
0,066
0,055
0,044
0,039
0,035
0,030
0,026
0,022
+4 m
+3 m
+2 m
+1 m
+/-0m
–1 m
–3
m
–4 m
Uncoiled length of intake pipe
Dimensioning diagram for intake pipes, dimension Ø 4/6 mm
Range of application: 1-10 liters/h, oil temperature: 0-10 °C (outdoor tank)
–2 m
there. In order to avoid contamination caused by undefined escaping oil,
we recommend using a special de-aeration fitting (see chapter 10.3). If no
flame is generated after the starting sequence, you should repeat this pro-
cess by eliminating the lockout of the firing unit. In order to avoid the over-
loading of the ignition unit as well as damage to the pump by trapped air,
you should eliminate the lockout of the burner no more than 3 times in a
row. If the complete de-aeration of the oil supply is not possible this way,
we recommend the use of an external suction pump for de-aeration.
3.6 Oil supply connection to the burner
For cover hood versions, the oil tubes mounted to the pump can optionally
be led out from the burner through a recess at the left or right side of the
base plate.
To this end, the oil tubes are inserted in a perforated rubber grommet
which is inserted in the recess of the base plate. The recess of the base
plate which is not used must be sealed with an unpunched grommet
(blank grommet). Tubes for cover hood versions are led out from the
burner through the right recess in the base plate as a standard. The tube
connection at the oil supply side is designed as a 3/8" spigot nut with
conical nipple.
Oil tube conduit
Attention:
The sealing plugs of the oil tubes must be removed before commissioning
the burner. Make sure to observe the arrow marking for flow direction at
the connecting ends of the oil tubes when connecting them to the oil
supply.
3.7 General checks
The following checks must be carried out prior to burner commissioning:
– Is mains voltage applied?
– Is oil supply ensured?
– Are all sealing plugs removed from the oil tubes?
– Are the oil tubes correctly connected (feed / return flow)?
– Is combustion air supply ensured?
– Was the burner correctly mounted and the boiler door professionally
closed?
– Is the boiler filled with water?
– Is the tightness of boiler and exhaust gas conduit ensured?
3.8 Burner setting
Each burner is preset by the factory in accordance with the basic adjust-
ment table (see chapter 5). The basic factory adjustment for air volumes
results in excess air depending on the combustion chamber and nozzle
tolerance. In order to achieve low-emission combustion values, the air vo-
lume setting must always be adjusted. Therefore, it is absolutely neces-
sary for the commissioning of the burner to measure the CO
2
content as
well as the soot number. We recommend to operate the burner at a CO
2
content between 12 and 13%. Make sure not to exceed a soot value of
Rz
0.5.
Combustion air flow
The combustion air flow is determined by the existing combination of baf-
fle plate and burner pipe (A/B/E/F), the distance between oil nozzle and
baffle plate, the set position of the baffle plate in the cone-shaped burner
pipe and the position of the air regulator.
EN
Содержание HL 60 ALV.2
Страница 15: ...15 DE 7 Explosionszeichnung mit Ersatzteilliste...
Страница 20: ...20 DE 9 Brennerabmessungen HL 60 ALV 2 BLV 2 Schiebeflansch HL 60 ALV 2 BLV 2 Unitflansch...
Страница 21: ...21 DE 9 Brennerabmessungen HL 60 ELV 2 S FLV 2 S Schiebeflansch HL 60 ELV 2 S FLV 2 S Unitflansch...
Страница 33: ...33 EN 7 Expanded view with spare parts list...
Страница 38: ...38 EN 9 Burner dimensions HL 60 ALV 2 BLV 2 sliding flange HL 60 ALV 2 BLV 2 unit flange...
Страница 39: ...39 EN 9 Burner dimensions HL 60 ELV 2 S FLV 2 S sliding flange HL 60 ELV 2 S FLV 2 S unit flange...
Страница 51: ...51 FR 7 Vue clat e avec liste des pi ces de rechange...
Страница 56: ...56 FR 9 Dimensions du br leur HL 60 ALV 2 BLV 2 Bride coulissante HL 60 ALV 2 BLV 2 Bride unitaire...
Страница 57: ...57 FR 9 Dimensions du br leur HL 60 ELV 2 S FLV 2 S Bride coulissante HL 60 ELV 2 S FLV 2 S Bride unitaire...
Страница 69: ...69 IT 7 Disegno esploso con elenco parti di ricambio...
Страница 74: ...74 IT 9 Dimensioni bruciatore HL 60 ALV 2 BLV 2 Flangia scorrevole HL 60 ALV 2 BLV 2 Flangia unitaria...
Страница 75: ...75 IT 9 Dimensioni bruciatore HL 60 ELV 2 S FLV 2 S Flangia scorrevole HL 60 ELV 2 S FLV 2 S Flangia unitaria...