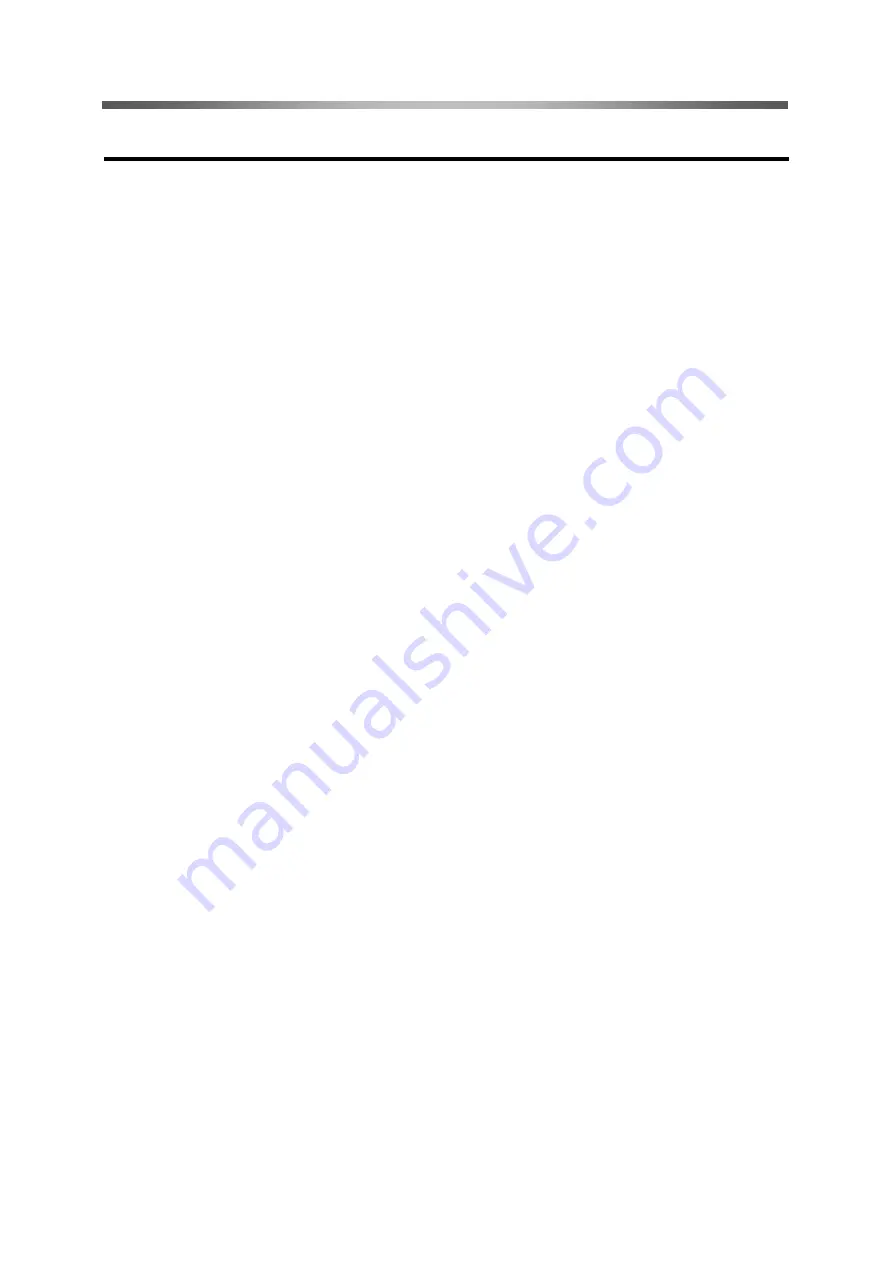
Chapter 7 Troubleshooting
H
- 113 -
Deviation counter overflow
(Alarm clear: available)
●
Description
The alarm occurs when the value of the deviation counter exceeds the parameter setting value
(PSF-520 No.21 Allowable position deviation). This alarm can be reset by inputting an ON signal to
“CN2 Alarm Clear: ALM-CLR” after inputting an ON signal to “CN2 Clear: CLEAR” or “CN2 Deviation
Clear: DEV-CLR.”
●
Diagnostic tips
(1) If the alarm occurs when the power is turned on:
◆
Cause 1: Main circuit was turned ON while inputting command pulse. The power was applied
while the actuator was driving.
⇒
Remedy: Stop command pulse or the actuator, and turn on the power, again.
◆
Cause 2: HA-680 driver control circuit failure
⇒
Remedy: Contact Harmonic Drive Systems,Inc. (Replace the HA-680 driver)
(2) If the alarm occurs during acceleration or deceleration:
◆
Cause 1: Gain is too low.
⇒
Remedy: Adjust gains in [parameter]
→
[00: position loop gain], [01: Speed loop
proportional gain], [02: speed loop integral gain] and [03: Speed loop
derivative gain] proportional according to the load.
◆
Cause 2: Parameters of the [Command pulse input factor] are wrong.
⇒
Remedy: Set the parameter correctly in [parameter]
→
[23: Command pulse input
factor-numerator], [24: Command pulse input factor-denominator], again.
◆
Cause 3: [Command pulse frequency] is too large.
⇒
Remedy: Decrease the [Command output pulse frequency] setting of the higher-level
system. The appropriate frequency is normal rotation speed of actuator
(r/min)
×
60 or less.
◆
Cause 4: The load inertia is too large.
⇒
Remedy 1: Reduce the load inertia.
⇒
Remedy 2: Modify the command pulse frequency of the host to accelerate and
decelerate more slowly.
(3) If the speed does not increase according to the command and the alarm occurs
after a while:
◆
Cause 1: OFF state of input signal [CN2: FWD inhibit] or [CN2: REV inhibit].
⇒
Remedy: Verify breakage of CN2 connector cable.
(4) Actuator did not rotate.
◆
Cause 1: Incorrect motor cable connection or wrong phase order
⇒
Remedy 1: Correct the connection between the motor cable and the connector.
⇒
Remedy 2: Connect the motor cable and the connector in correct phase order referring
to [Chapter 3-7: Connecting motor and regeneration resistor cables] of this
manual.
◆
Cause 2: Poor encoder connector (CN1) connection.
⇒
Remedy: Plug the CN1 connector firmly.
Содержание HA-680 Series
Страница 6: ...HA 680 series servo driver manual MEMO ...