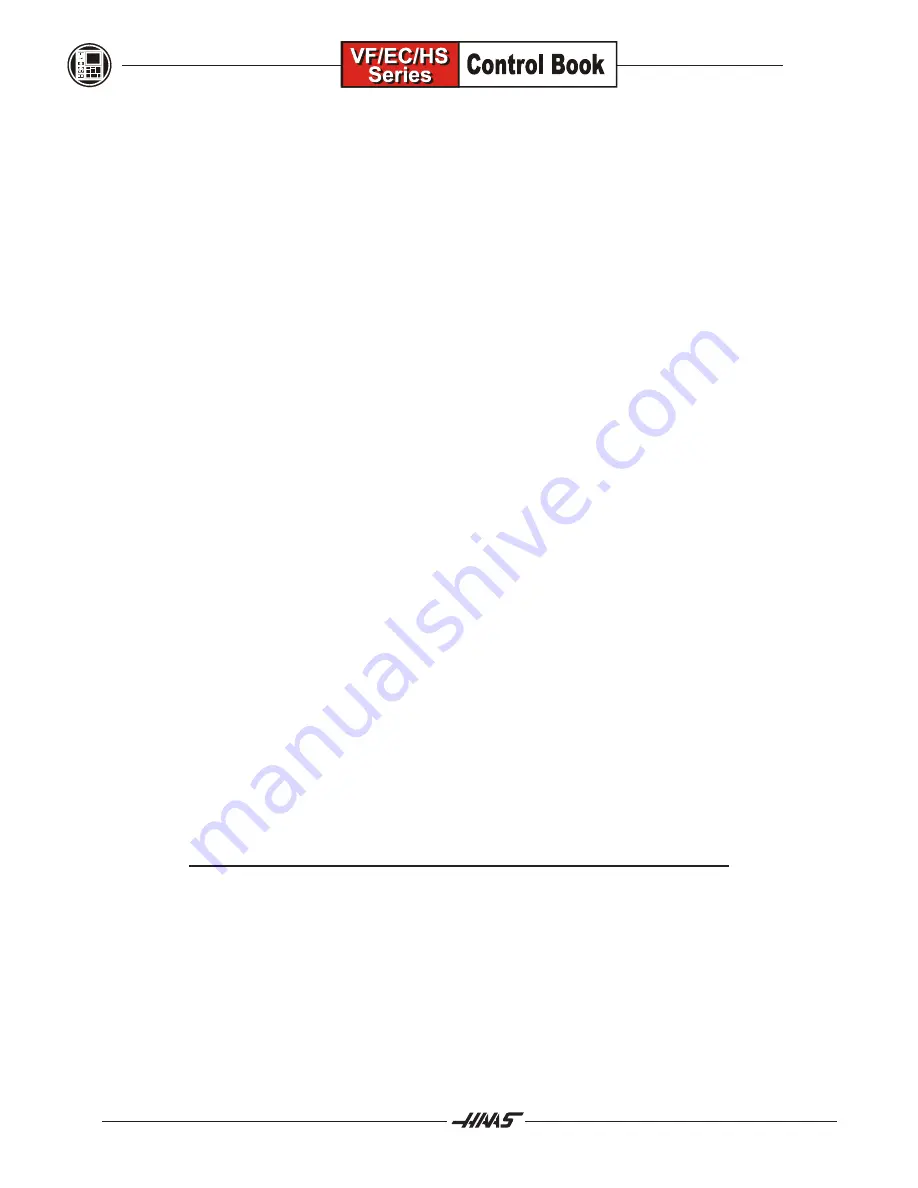
14
January 2004
The function of the offset display page can accommodate 3, 4, or 5 axes. Only the axes that are enabled are
displayed on the work offset display. For example, if the fourth axis is enabled with Setting 30, and the fifth axis
is not, then the display will show the X, Y, Z, A axes. If only the fifth axis is enabled with Setting 78, then the
position display will show X, Y, Z, B. If the fourth axis is not enabled, then it will not be displayed.
A tool diameter offset may be entered as either a RADIUS or DIAMETER value. Setting 40 is used to select
between these two choices. The RADIUS/DIAMETER value entered for cutter compensation is the sum of the
Geometry and Wear values. The number of flutes on each tool can be entered in for calculating and displaying
Chip Load on first page of the Current Commands display. The number of flutes default is 2, and each tool will
be set at 2 when the ORIGIN key is pressed to zero all the offsets, while the offset screen is displayed.
Cutter compensation is activated with G41 (left of the line) and G42 (right of the line) along with the selected
tool diameter (D value). Usually, positive values for cutter compensation are used when defining the actual tool
diameter, when programmed to the actual part line. Negative values for cutter compensation are usually used
when the tool center has been programmed, like when programming with a CAD/CAM system, to define only
the tool wear to adjust for part size from zero.
If you reverse the compensation numbers on either side of the part thats using cutter compensation, G41 and
G42 will be reversed. That means a G41 command with negative numbers will work the same as a G42 with
positive numbers.
Offsets may be sent and received with the RS-232 port. Refer to the Data Input / Output section for a descrip-
tion of how to do this.
When the COOLANT SPGT of Parameter 57 is enabled (with a 1), the CLNT POS column of the offset display
will then be accessible. The coolant spigot positions to the location defined in the offset register next to the
offset number under the CLNT POS column. The spigot will position to the location that is defined in the
H##
line, when it is encountered in a program that has an M08 coolant on command. If offset #5 (H05) has
8
entered on that line under the CLNT POS column, the spigot will then be moved to position #8. When the
cursor is positioned on the CLNT POS column, the current spigot position will be shown at the bottom left
corner of the display. If at start up, the spigot has not been zeroed, the position location will be blank. To enter
a nuber, cursor onto a coolant position register number, pressing WRITE will add to the number thats in the
register and F1 will set it into the register.
The permissible values that can be entered into this coolant position column are controlled by Parameter 206,
SPIGOT POSITIONS. Entering a value of zero (0) indicates that the spigot will not be moved when an H## code
sequence is encountered.
If Setting 15, H & T Code Agreement is ON, it is used by the control to force the tool number (T5) and offset
number (H05) to be the same; otherwise an alarm will occur. This is the preferred setting, as it avoids crashes,
if youre only using one offset per tool. If you are going to be using more then one offset, or different offsets per
tool, then this setting needs to be OFF.
NOTE
:
The tool length (H##) and Radius/Diameter (D##) offset numbers are usually the
same as the tool number (T##).
Содержание EC Series
Страница 1: ...January 2004 ...
Страница 7: ...V I January 2004 ...
Страница 125: ...118 January 2004 ...
Страница 126: ......