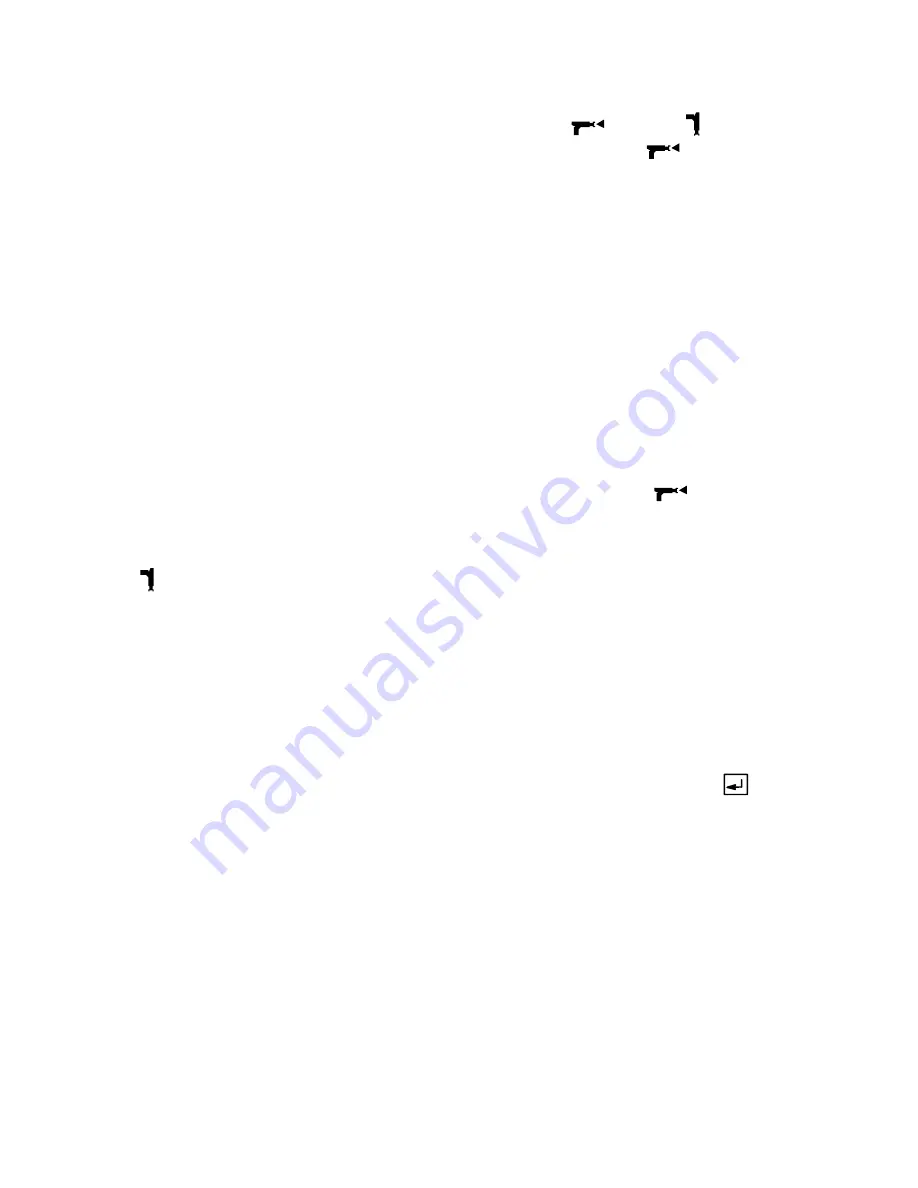
2–16
Overview
Using Recipes/Color Change
There are three modes of operation relating to the
changing of recipes: No Color Change, Integrated
Color Change, and Integrated Color Change with
Queue. Refer to page 8–22. The controller logic
decides whether or not to allow a chosen recipe
change to occur. The criteria for allowing a recipe
change are as follows:
1.
The new recipe must contain valid data for the
desired ratio, flow meter K-factors, tolerance, and
pot life times.
2.
An active alarm must not exist in the system.
3.
An Integrated Color Change can not already be in
progress.
4.
The recipe number must not be greater than the
number of recipes configured to run on the sys-
tem.
5.
The input device used to change the recipe value
must be configured as the recipe input device
(User Interface, Network, I/O, or Operator Station).
6.
When “No Color Change” is selected, the operator
switch on the Operator Station must be in the
Standby
position.
No Color Change
The system will boot up for the first time with color
change turned off. In this mode, color changes are
performed manually. The recipe number is changed
through the User Interface, Network, I/O, or Operator
Station. The operator must manually dump and purge
the old material from the system and then load the new
material into the system.
Integrated Color Change
The Integrated Color Change mode of operation
automatically performs the tasks necessary to execute
a color change. This is a time-based mode that is
configurable by the user. Refer to page 8–21. The
timing of the color change is configured in one of four
color change sequences. The color change
sequences contain start times and timer duration for
the devices that are controlled during a color change.
Each recipe is then assigned one of the four color
change sequences for its operation.
A color change may be performed with the operator
switch in the Mix
or Standby
position. If the
operator switch is in the Mix
position, the system
will be ready for immediate spraying after a color
change. The green light on the Operator Station will
blink while a color change is in operation. The green
light indicates that the system is busy and is not ready
for spraying.
Mix/Load Volumes
If mix/load volumes are configured for the system, the
fill portion of the color change may continue after the
color change has timed out. This feature may be used
in conjunction with a gun flush box to make sure that
the desired volume of material is loaded into the sys-
tem. The system keeps track of the volume that is
mixed during the fill portion of the color change. If the
mix/load volume is not reached, then the system will
continue to fill until the volume is reached (the operator
switch needs to be in the Mix
position for this to
occur automatically). Setting the mix/load volume to
zero will disable the mix/load volume feature.
Recipe Zero
Recipe zero is considered the “Purge Down” recipe.
The purpose of this recipe is to allow the user to purge
out the material lines and the mixed material lines
without loading a new color. A typical use for recipe
zero is at the end of a shift. The operator performs a
color change to recipe zero and the lines are cleaned
out to prevent hardening of catalyzed material between
shifts. Multiple Purge Downs may also be performed if
the lines are not sufficiently clean. Another Purge
Down is triggered by pressing the Enter
key on the
Operator Station or by setting the the color change bit
on the I/O high.
NOTE:
Recipe 0 has a unique Purge Sequence 0 to
allow for end of shift or production shutdown. If you are
using a solvent meter, any additional solvent used in
the recipe 0 purge cycle will not be included in the
solvent totals. It is important to configure Purge Se-
quence 0 to flush all materials clean in one purge
cycle, to maintain accurate solvent use records.
Continued on the next page.
Содержание PrecisionMix ii
Страница 6: ...6 ...
Страница 7: ...1 1 Warnings Warnings 1 ...
Страница 8: ...1 2 Warnings ...
Страница 11: ...Overview 2 1 Overview 2 ...
Страница 12: ...2 2 Overview ...
Страница 15: ...Overview 2 5 ...
Страница 31: ...Installation 3 1 Installation 3 ...
Страница 32: ...Installation 3 2 ...
Страница 58: ...Installation 3 28 Notes ...
Страница 63: ...Installation 3 33 Power up Checklist Fig 3 23 CP Interface Step 5 Step 6 Step 4 Step 7 Step 10 ...
Страница 67: ...Operation 4 1 Operation 4 ...
Страница 68: ...Operation 4 2 ...
Страница 83: ...Operation 4 17 Notes ...
Страница 90: ...Operation 4 24 ...
Страница 91: ...Screen Map 5 1 Screen Map 5 ...
Страница 92: ...5 2 Screen Map ...
Страница 94: ...5 4 Screen Map ...
Страница 95: ...Run Monitor 6 1 Run Monitor 6 ...
Страница 96: ...Run Monitor 6 2 ...
Страница 103: ...Totalizers 7 1 Totalizers 7 ...
Страница 104: ...Totalizers 7 2 ...
Страница 108: ...Totalizers 7 6 ...
Страница 109: ...System Configuration 8 1 System Configuration 8 ...
Страница 110: ...System Configuration 8 2 ...
Страница 138: ...System Configuration 8 30 PrecisionMix II 3K Robotic Interface Integrated Color Change TI0494 Fig 8 1 ...
Страница 142: ...System Configuration 8 34 ...
Страница 143: ...Recipe Setup 9 1 Recipe Setup 9 ...
Страница 144: ...Recipe Setup 9 2 ...
Страница 165: ...10 1 Troubleshooting Troubleshooting 10 ...
Страница 166: ...10 2 Troubleshooting ...
Страница 182: ...10 18 Troubleshooting ...
Страница 183: ...11 1 Service Service 11 ...
Страница 184: ...11 2 Service ...
Страница 192: ...11 10 Service ...
Страница 193: ...12 1 Parts Parts 12 ...
Страница 194: ...12 2 Parts ...
Страница 207: ...12 15 Parts Notes ...
Страница 228: ...12 36 Parts ...
Страница 229: ...13 1 Utilities Software Utilities Software 13 ...
Страница 230: ...13 2 Utilities Software ...
Страница 254: ...13 26 Utilities Software ...
Страница 255: ...14 1 Technical Data Technical Data 14 ...
Страница 256: ...14 2 Technical Data ...
Страница 259: ...14 5 Technical Data Notes ...