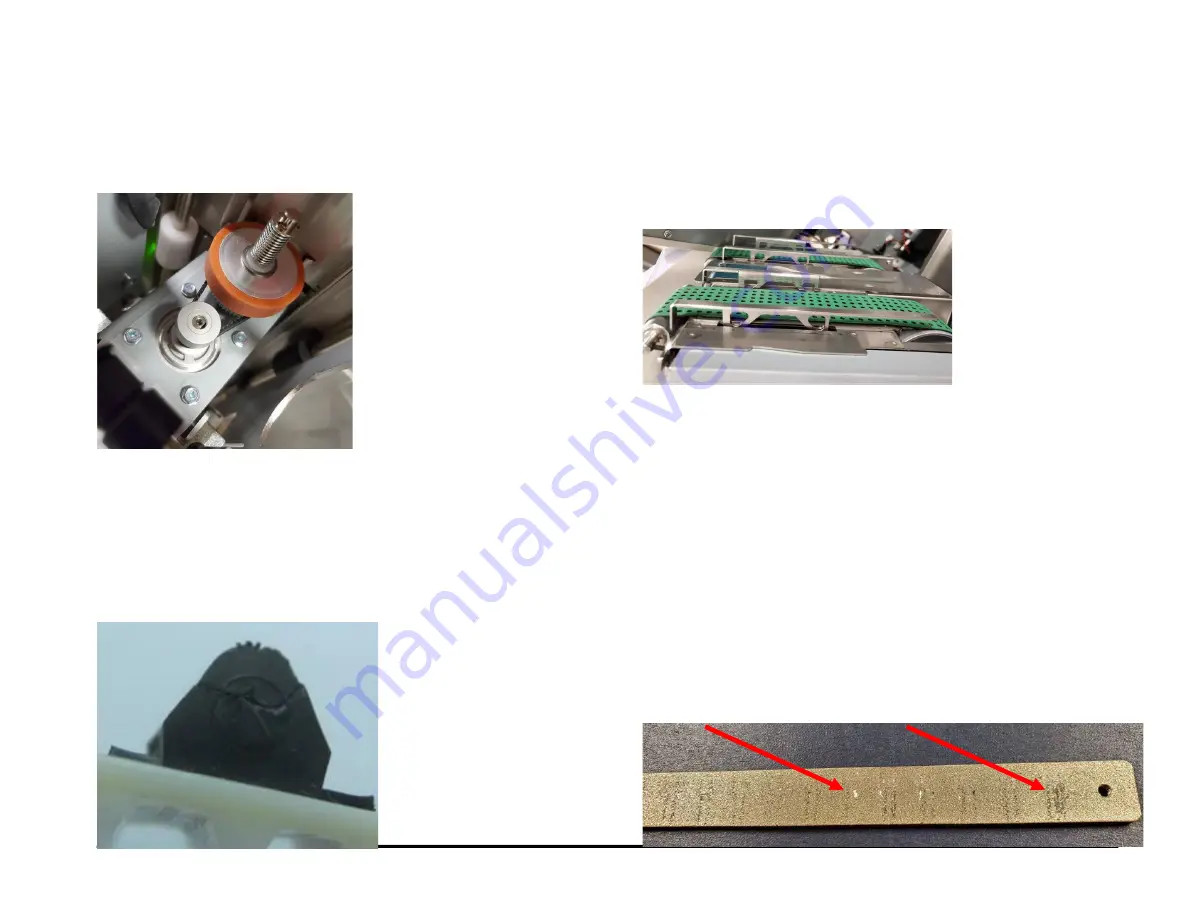
GBC StreamWire
07/23/2020
General Procedures and Information
6-71
Steering Rollers
Inspect the steering rollers for damage.
Replace the rollers if the rubber portion is broken or missing sections.
When inspecting the rollers also check that the tension of the belt is
properly set.
Element Feed Belt
Inspect the belt for damaged or missing teeth. Check each tooth for
damage. The element feed belt should be replaced when a broken tooth
is present. A broken tooth is any tooth that is missing a piece. Teeth
break and crack as the result of wire jams.
If teeth are cracked but not broken, the belt does not need immediate
replacement but should be monitored. Below is an example of a cracked
tooth.
Kick Downs
Inspect the kickdowns for damage.
The kickdowns should be free of bends. The flat sanction should be
straight and parallel to the green belts. All kickdowns should be the same
length. Kick downs should be replaced if they are bent or broken.
Attempting to bend a kickdown into shape will result in a failure shortly
after.
Closer Jaw Plates
Closer jaw plates should be replaced every 50,000 books or when the
machine has closing issues that cannot be resolved through adjustments.
Use the information below to determine if the jaws need to be replaced
early.
The surface of the closer jaws will naturally discolor as a result of the wire
element coating rubbing off onto the plates. This discoloration does not
indicate a plate requires replacement.
The jaw surface can become damages and loose its abrasive texture.
This can cause issues with binding if present in enough locations on the
jaw.
The area indicated by the arrow on the left is an instance of the abrasive
surface rubbing off.
The area indicated by the arrow on the right is an example of the abrasive
surface discoloring from the wire coating and should not cause
performance issues.
Содержание StreamWire
Страница 9: ...GBC StreamWire 07 23 2020 Service Manual ix Notes...
Страница 87: ...GBC StreamWire 07 23 2020 RTPS 2 72 Notes...
Страница 89: ...Book Quality 07 23 2020 GBC StreamWire 3 2 This page intentionally left blank...
Страница 343: ...General Procedures and Information 07 23 2020 GBC StreamWire 6 6 GP 6 1 4 Service Menu Flowchart...
Страница 420: ...GBC StreamWire 06 25 2019 General Procedures and Information 6 83 A C Board Test Points B Board Test Points...
Страница 428: ...GBC StreamWire 12 18 2018 Wiring Data 7 3 o System Wiring...
Страница 429: ...Wiring Data 12 18 2018 GBC StreamWire 7 4 o Element Feeder Module...
Страница 430: ...GBC StreamWire 12 18 2018 Wiring Data 7 5 o Element Transfer Module...
Страница 431: ...Wiring Data 12 18 2018 GBC StreamWire 7 6 o Knife Module...
Страница 432: ...GBC StreamWire 12 18 2018 Wiring Data 7 7 o Closer Module...
Страница 433: ...Wiring Data 12 18 2018 GBC StreamWire 7 8 o Holder Module...
Страница 434: ...GBC StreamWire 12 18 2018 Wiring Data 7 9 o Book Drawer...
Страница 435: ...Wiring Data 12 18 2018 GBC StreamWire 7 10 o Paper Transport Module...
Страница 436: ...GBC StreamWire 12 18 2018 Wiring Data 7 11 o Sheet Tappers Module...
Страница 437: ...Wiring Data 12 18 2018 GBC StreamWire 7 12 o Deflector Module...
Страница 438: ...GBC StreamWire 12 18 2018 Wiring Data 7 13 o Stacker Module...
Страница 439: ...Wiring Data 12 18 2018 GBC StreamWire 7 14 o Alignment Module...
Страница 440: ...GBC StreamWire 12 18 2018 Wiring Data 7 15 o Interlock AC and LCD Connections...
Страница 442: ...Installation Instructions 03 26 2019 GBC StreamWire 8 2 This page intentionally left blank...