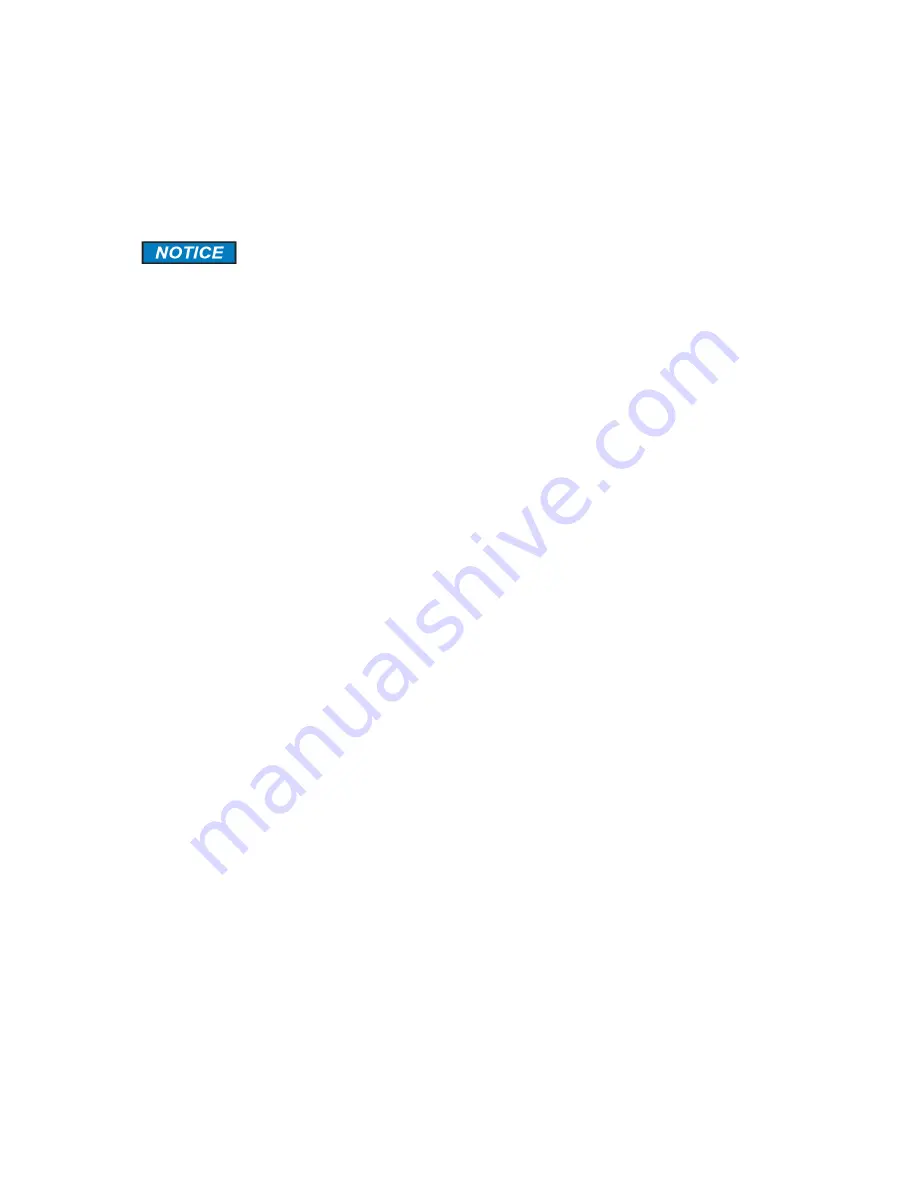
Revision 14
50
August 02, 2019
e) Repeat steps c and d for the other end of the tube.
f) Replace the end caps on the furnace enclosure. Be sure to align the threads correctly.
The end-caps will screw on very easily if the threads are aligned correctly. DO NOT
FORCE! Cross threading will seriously impair the explosion proof nature of the enclosure.
Once the quartz reaction tube has been inserted, it is necessary to leak
check the furnace for leaks prior to powering it back on (Section 3.8).
3.7 Connecting Gas to Analyzer
3.7.1 Connecting Gas to the Analyzer
To connect gas to the system:
a) Attach sample gas lines to the sample inlet, zero gas, calibration gas and reference gas
ports on the analyzer.
b) If the analyzer is equipped with a sample system, set the pressure regulator to 15 psig. If
the analyzer is not equipped with a sample system, ensure that the sample gas is clean
and is regulated to a pressure of 15 psig before connecting it to the system.
c) If the analyzer is equipped with the total sulfur option, set the sample flow meter to a flow
of 0.5 and the hydrogen flow meter to a flow of 1.5. If the total sulfur measurement range
is below 0-1ppm, set the hydrogen flow meter to 1.0 and the sample flow meter to 1.0.
3.7.2 Leak Testing of the Compression Head
To ensure that repeatable data is obtained, it is essential to have a good seal between the
compression head, the tape, and the sample chamber. To test the seal, Galvanic
recommends the use of a Dwyer Minihelic II gauge, available from Galvanic Applied
Sciences. The gauge measures a range of pressure from 0 to 5 inches of water column.
The following procedure is used to leak-check the analysis compression head and to ensure
that a proper seal is obtained:
a) Make sure the flow indicated on the chassis rotameter is approximately 2.0 before
following this procedure.
b) Place the system in
Bypass
mode via the hand held keypad before carrying out this
procedure.
c) Remove the vent line from the elbow at the base of the chassis and attach the Minihelic
to the elbow, as shown in Figure 3-23.
Содержание ProTech903
Страница 2: ......
Страница 96: ...Revision 14 96 August 02 2019 Figure 5 19 Event Log...
Страница 122: ...Revision 14 122 August 02 2019 Figure 5 38 Typical Modicon with Floating Point List...
Страница 124: ...Revision 14 124 August 02 2019 Figure 5 40 Expanded Modbus Nodes...
Страница 167: ...Revision 14 167 August 02 2019 Figure 9 1 DC Power Wiring Diagram Figure 9 2 AC Power Wiring Diagram...
Страница 168: ...Revision 14 168 August 02 2019 Figure 9 3 Total Sulfur Wiring Diagram Figure 9 4 AC DC Power Wiring Diagram...
Страница 169: ...Revision 14 169 August 02 2019 Figure 9 5 Solenoid Drivers Wiring Diagram Figure 9 6 Relays Wiring Diagram...
Страница 173: ...Revision 14 173 August 02 2019 Figure 9 13 Isolated RS 485 Port Figure 9 14 P17 RS232 Port to Ethernet Cable...
Страница 175: ...Revision 14 175 August 02 2019 Figure 9 17 Non Isolated 4 20 mA Inputs...
Страница 190: ...Revision 14 190 August 02 2019...