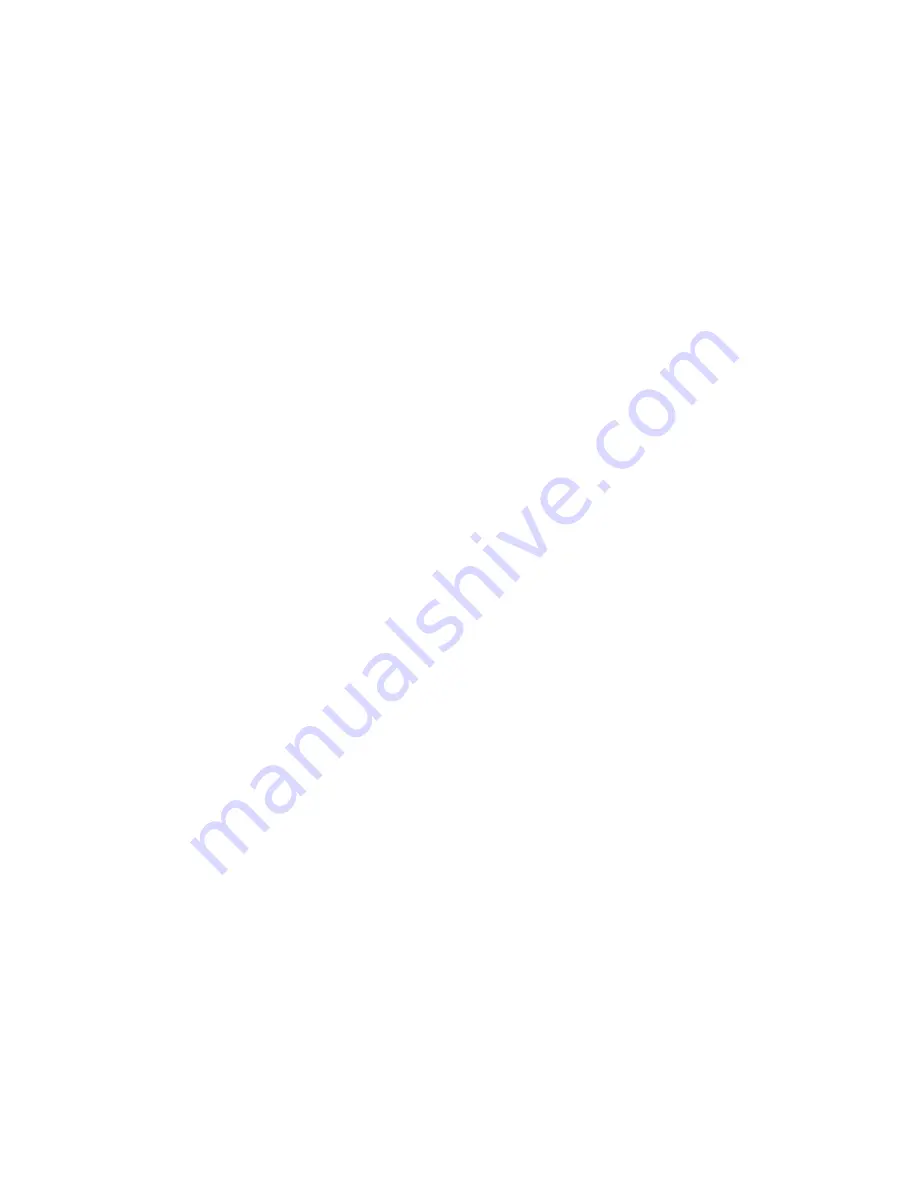
Revision 14
151
August 02, 2019
Section 7
Maintenance
7.1 Overview
The analyzer is designed for automatic trouble-free operation under the continuous
supervision of the internal computer. As described in Sections 4 and 5, a series of alarms are
presented on the hand held keypad and the application program if an operation or function is
not performing in the appropriate manner to alert the user that a problem exists. A detailed
discussion of service protocols is presented in Section 8.
Routine Preventative Maintenance of the analyzer consists of a periodic performance of the
Maintenance Check-out Procedure
(Section 7.2). Routine maintenance will typically
correspond to tape usage, which is 4 – 6 weeks for most applications.
On a periodic basis, it will be necessary to replace certain components of the system such as
the sensing tape, the quartz tube in the total sulfur accessory the H
2
S filter and the liquid in
the humidifier. Replacement procedures for these items are described in Section 7.3-7.6.
A series of videos demonstrating typical maintenance procedures for the ProTech903
analyzer is available on Galvanic Applied Sciences Inc.’s YouTube channel (search YouTube
for Galvanic Applied Sciences).
7.2. Routine Maintenance Procedure
a) Check display for any alarms (press
F2
on keypad). Refer to Section 8 for how to resolve
any active alarms
b) Disable alarms by pressing the
BYPASS
button.
c) Turn off gas to the analyzer. Pull back the Compression Head and inspect the Sample
Chamber for paper dust and dirt. If required remove the Sample chamber assembly and
clean as described in Section 7.3.
d) Change tape and ensure the tape is re-inserted properly as described in Section 7.3.
e) Advance the tape with TAPE ADV key.
f) Check for proper take-up.
g) Top up the level of the acetic acid solution to the red line as described in Section 7.7.
h) Re-calibrate the sensor. Press
F4 MNT
on the keypad, then press
F1
and
scroll down the
screens to
SenCal.
Press the EDIT key and press ENTER key to toggle the parameter to
ON. The sensor will calibrate and then automatically go online.
i) Check that the mV reading is 0 mV +/- 10 mV at the start of the cycle.
j) Check the sample system as described in Sections 7.4 and
7.5.
Содержание ProTech903
Страница 2: ......
Страница 96: ...Revision 14 96 August 02 2019 Figure 5 19 Event Log...
Страница 122: ...Revision 14 122 August 02 2019 Figure 5 38 Typical Modicon with Floating Point List...
Страница 124: ...Revision 14 124 August 02 2019 Figure 5 40 Expanded Modbus Nodes...
Страница 167: ...Revision 14 167 August 02 2019 Figure 9 1 DC Power Wiring Diagram Figure 9 2 AC Power Wiring Diagram...
Страница 168: ...Revision 14 168 August 02 2019 Figure 9 3 Total Sulfur Wiring Diagram Figure 9 4 AC DC Power Wiring Diagram...
Страница 169: ...Revision 14 169 August 02 2019 Figure 9 5 Solenoid Drivers Wiring Diagram Figure 9 6 Relays Wiring Diagram...
Страница 173: ...Revision 14 173 August 02 2019 Figure 9 13 Isolated RS 485 Port Figure 9 14 P17 RS232 Port to Ethernet Cable...
Страница 175: ...Revision 14 175 August 02 2019 Figure 9 17 Non Isolated 4 20 mA Inputs...
Страница 190: ...Revision 14 190 August 02 2019...