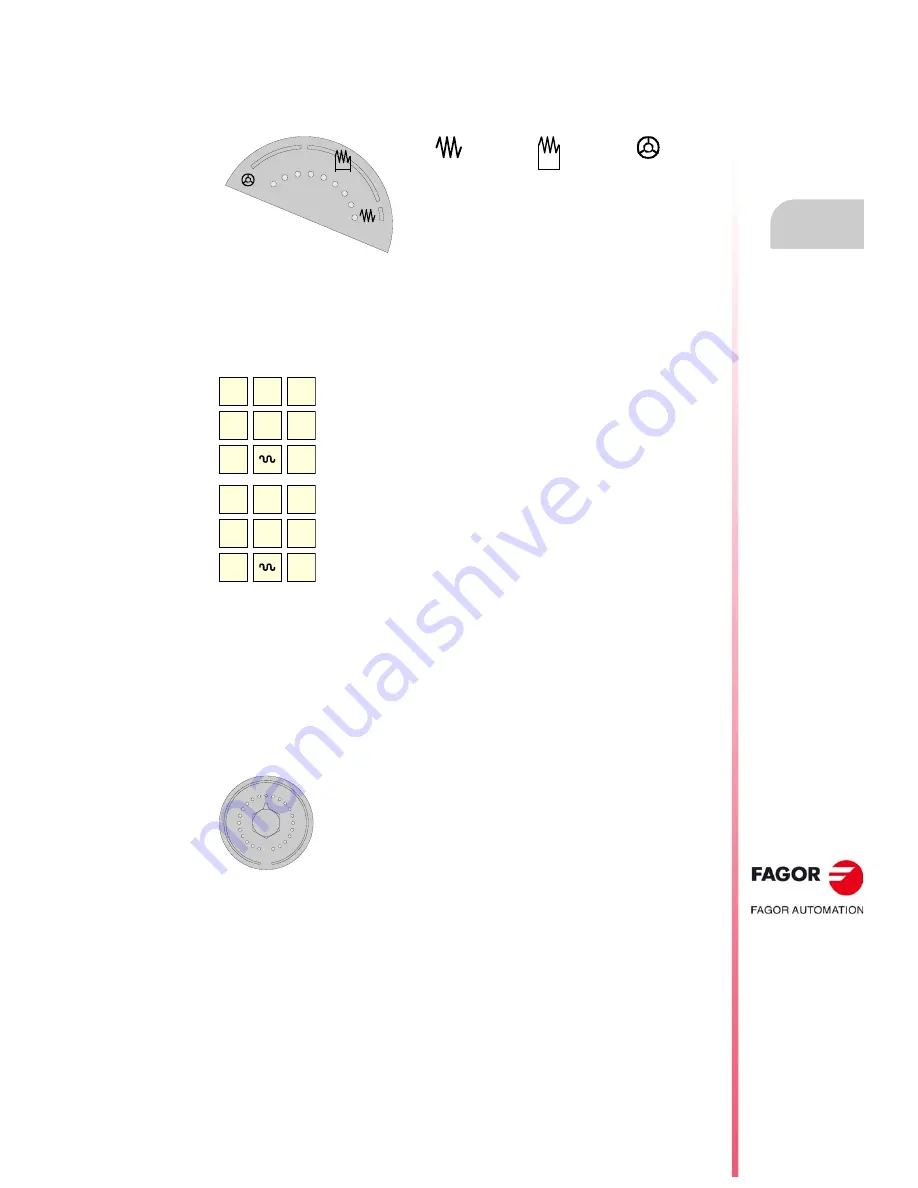
Operating manual (MC).
CNC 8060
CNC 8065
O
PERATING
IN JO
G MODE
2.
Ope
rations with the axes.
·37·
(R
EF
: 1709)
2.2.2
Jog
The axes may be jog using the JOG keyboard on the operator panel. The type of jog is
selected with the jog selector switch on the operator panel.
The jog keyboard and the feedrate selector
JOG keypad.
There are two types of jog keyboards depending on the behavior of the keys.
User keys as jog keys
The CNC offers the OEM the possibility to enable the user keys as jog keys. The user keys
defined this way behave like the jog keys.
Feedrate selector.
Continuous jog
Incremental jog
Handwheels
The keypad has two keys for each axis. One to jog the axis in the
positive direction and another one to move it in the negative direction.
To move a single axis, press the axis key and the one for its jogging
direction.
The keypad has a key for each axis and two keys for moving direction,
common to all the axes.
To jog an axis requires activating both the axis key and the moving
direction. There are two options, depending on how the jog keyboard
has been configured.
• The axis will move while both keys are pressed, the axis key and
the direction key.
• When pressing the axis key, the key remains active. The axis will
move while the direction key is kept pressed. To de-select the axis,
press [ESC] or [STOP].
The movement is carried out at the feedrate defined by the OEM. The
feedrate may be varied between 0% and 200% using the feedrate override
switch on the operator panel.
10000
1000
100
10
1
100
10
1
jog
jog
X+
X-
Y+
Z+
Y-
Z-
7+
7-
X
_
+
Y
Z
4
5
6
200
190
180
170
160
150
140
130
120
110
100
90
80
70
60
50
40
30
20
10
4
2
0
FEED
Содержание CNC 8060
Страница 1: ...Ref 1709 8060 8065 CNC Operating manual MC...
Страница 8: ...BLANK PAGE 8...
Страница 14: ...BLANK PAGE 14...
Страница 16: ...BLANK PAGE 16...
Страница 18: ...BLANK PAGE 18...
Страница 22: ...BLANK PAGE 22...
Страница 24: ...BLANK PAGE 24...
Страница 26: ...BLANK PAGE 26...
Страница 28: ...Operating manual MC CNC 8060 CNC 8065 1 GENERAL CONCEPTS Accessing the conversational mode 28 REF 1709...
Страница 169: ...Operating manual MC CNC 8060 CNC 8065 169 User notes REF 1709...
Страница 170: ...Operating manual MC CNC 8060 CNC 8065 170 User notes REF 1709...
Страница 171: ...Operating manual MC CNC 8060 CNC 8065 171 User notes REF 1709...