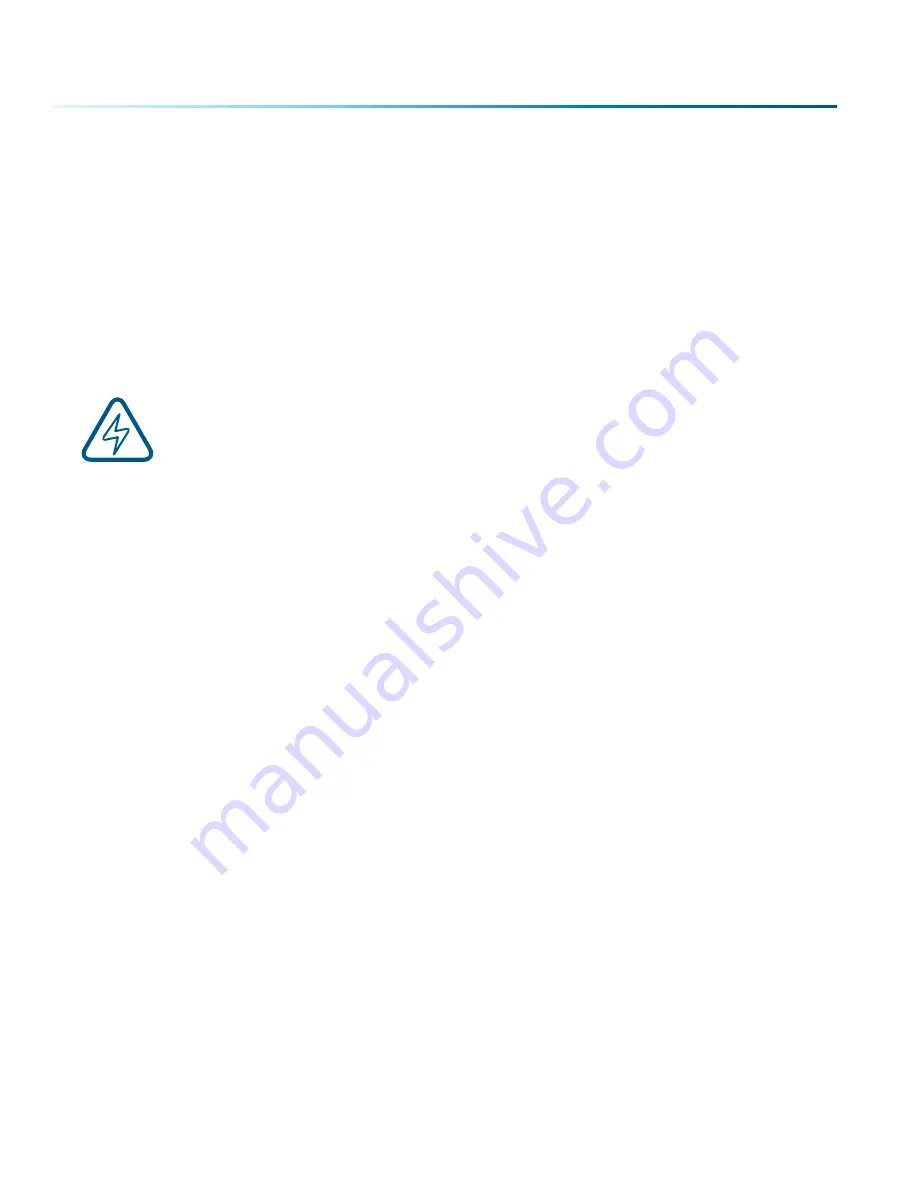
Anodized Aluminum
Anodized aluminum is a coated aluminum that comes in a variety of colors and can usually be easily
engraved with a CO2 laser.
• Black anodized aluminum is great to work with because it turns white when engraved and provides
the best contrast of all of the colors of anodized aluminum.
• Some colors of anodized – red for instance – will not turn completely white when laser engraved.
Red anodized will produce a light pink color. Performing a second pass can result in some
improvement, but usually a slight shadow of color will remain.
• Engrave anodized aluminum at high speeds and low powers for crisp, clean results. Too much
power applied to the anodized coating will distort the engraving and tends to over-burn the image.
•
Warning!
Metals are reflective. Using full power with them can potentially cause damage
to the machine.
Brass - Painted
Since the frequency of the CO2 laser is not compatible with bare metals, uncoated brass cannot be laser
engraved. For bare-metal marking you will want to use an Epilog FiberMark system. In order to engrave
brass with a CO2 laser you need to use brass that has some sort of coating – typically paint. The laser
removes the paint and exposes the brass substrate.
There are two basic types of engravable brass available, but they are not all compatible with the laser.
• By far, the most popular laser brass is actually brass-coated steel. First, a steel substrate is coated
with a thin layer of brass. Next, the brass is polished to a reflective finish and a coat of lacquer is
applied to the brass – Victory’s LaserBrite™ product has a lacquer finish. Finally, a paint coating is
applied on top of the lacquer for the finished product. When laser engraving brass-coated steel,
you are removing only the paint and exposing the polished brass coating that is protected by the
lacquer. The lacquer prevents the brass from oxidizing and the bright reflective surface will stay
bright for years.
• Some manufacturers also sell painted brass that is solid brass, not brass-coated steel. If the brass
is polished before the paint is applied you will have a bright, reflective engraved surface. If the
brass is not polished, the result will be a dull, tarnished brass that will require a secondary polishing
process after laser engraving. This is time consuming and most engravers do not want to spend the
time and effort necessary to turn this into an acceptable product.
• Note:
Always ask before lasering painted brass if you don’t know the substrate! If you are unsure
if your piece is brass-coated steel or genuine brass, you can test the material with a magnet. A
magnet will stick readily to brass-coated steel, but since solid brass is not magnetic, a magnet will
not adhere to solid brass.
- 182 -
SECTION 12: ENGRAVING MATERIALS
Содержание Fusion Pro 32
Страница 2: ......
Страница 6: ......
Страница 13: ...The following diagrams show the location of each specific label Fusion Pro 32 7 SECTION 1 SAFETY ...
Страница 14: ...Fusion Pro 48 8 SECTION 1 SAFETY ...
Страница 15: ... 9 SECTION 1 SAFETY ...
Страница 18: ......
Страница 28: ......
Страница 60: ......
Страница 98: ......
Страница 108: ......
Страница 132: ......
Страница 162: ......
Страница 184: ......
Страница 202: ......
Страница 214: ......
Страница 216: ......
Страница 242: ......