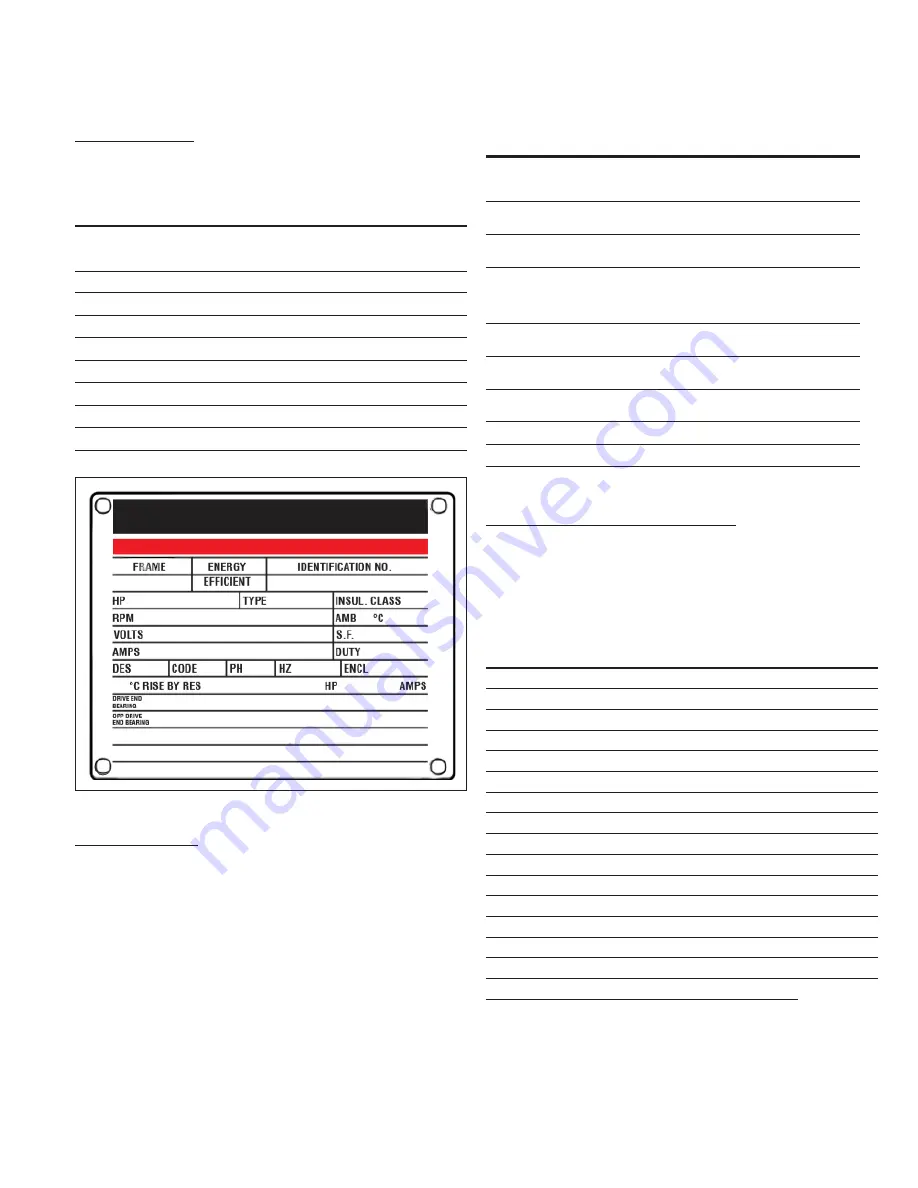
107
EATON
www.eaton.com
Instruction Booklet
IB020003EN
Effective January 2021
AMPGARD RVSS
Reduced Voltage Soft-Starter
User Manual
General starting guidelines
Motor characteristics
Setting up the RVSS will require defining the motor characteristics
(
PRG | 3. Motor Configuration
). Here you will enter (see
the motor nameplate (see
Figure 97
) or data sheets:
Table 37. RVSS motor characteristic parameters
Setting
Explanation
1. Service Factor
Motor nameplate service factor. Nameplate HP x
service factor = motor continuous rating (design
margin)
2. Motor Nominal Current Motor nameplate rated FLA (Amps)
3. Rated Voltage
Motor nameplate rated Volts
4. Rated Frequency
Motor nameplate rated HZ
5. Watts Motor
Motor power rating from data sheet
6. HP Motor
Motor nameplate rated HP
7. Motor Rated Efficiency
Motor nameplate or data sheet efficiency in %
8. Rated Power Factor
Motor nameplate or data sheet power factor in %
9. Speed Motor
Motor nameplate or data sheet RPM
Figure 120. Example motor nameplate
Starter characteristics
Once the motor is defined, the RVSS controller must be configured
for its mode of operation: (
PRG | 5.Operation Mode | 2.Profile 1 Selection
| 1. Starter Profile | 1. Voltage ramp with current limit
).
With the mode of operation defined, the operation parameters must
be set (
PRG | 6. Soft Start Configuration | Profile 1 Settings
) (see
):
Table 38. RVSS voltage ramp plus current limit mode of
operation
Setting
Explanation
1. Start ramp time
The time during which the output voltage ramps up
after a start to full voltage unless current limit is
reached first
2. Jog Voltage
The voltage (in % of line voltage) to be used when the
motor is jogged
5. Initial voltage
The immediate voltage output at the beginning of a
soft start, from which the voltage ramp begins
6. Current limit
The maximum allowed motor current (% of FLA) during
a start, regulated by the RVSS controller, as the motor
accelerates - see
Setting current limit based upon
Stop Ramp Time
For Stop Profile of Pump Deceleration (otherwise, not
used)
Deceleration Initial
Voltage
For Stop Profile of Pump Deceleration (otherwise, not
used)
Deceleration Final
Voltage
For Stop Profile of Pump Deceleration (otherwise, not
used)
Kick Start Voltage
For Kick Start enabled (otherwise, not used)
Kick Start Time
For Kick Start enabled (otherwise, not used)
14. Incomplete
sequence
Time allowed for motor acceleration after a start
initiation based upon motor thermal capacity. Set by
calculation or experiment.
Starter setpoints - by application experience
shows setpoints, based upon experience, intended to
provide initial setting that will likely achieve a successful start, for an
RVSS configured for Voltage Ramp with Current Limit control
.
ote:
N
They apply only when power system or mechanical system limits do
not overrule them.
Table 39. Approximate RVSS settings for voltage ramp with
current limit
Application
Initial
voltage
Ramp
time
Current limit
Pumps - Water
30-35%
13-15 sec
300-400%
Pumps - Other Than Water
35-45%
11-13 sec
350-450%
Positive Displacement Blowers
30-35%
13-15 sec
350-450%
Reciprocating Compressors
35-40%
13-15 sec
300-400%
Rotary Screw Compressors
35-45%
11-13 sec
400-500%
Chillers – Freon Based
25-30%
10 sec
300-400%
Chillers – Ammonia Based
40-50%
10 sec
400-450%
Fans
40-55%
12-13 sec
400-500%
Chippers
40-45%
11-12 sec
400-500%
Car Shredders
30-45%
10 sec
500-600%*
Ball Mills
35-40%
10 sec
400-600% *
Rod Mills
30-45%
10 sec
400-600% *
Conveyors
20-25%
13-15 sec
250-400%
Natural Gas Compressors
30-35%
12-13 sec
300-400%
High Centrifugal Loads
30-45%
10 sec
400-600% *
Setting current limit based upon motor nameplate data
RVSS current initial current limit settings can also be calculated using
the motor nameplate Locked Rotor Code values. These NEMA codes
relate a code alpha to a locked rotor KVA/HP range that translates
directly into corresponding Locked Rotor Amps from Full Load Amps
(also on the motor nameplate).
shows the relationship between the NEMA Locked Rotor
Codes and corresponding ranges of KVA per HP. For a Locked Rotor