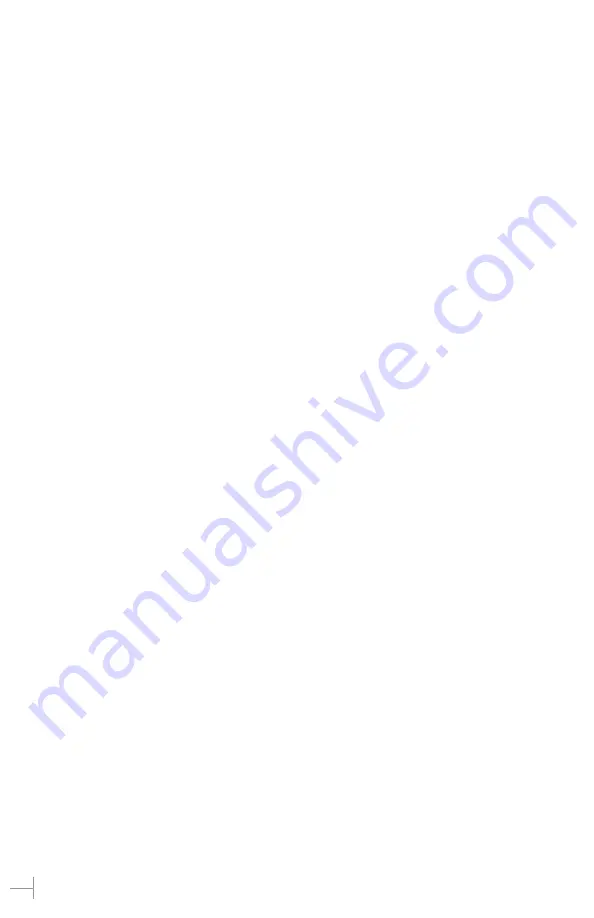
Once connected the machine now has the capability to send all real
time process and user data to a remote central database. That can
be polishing parameter data such as what fixture is in use or what
recipe is being run, or it can be user data such as what operator is
running the machine and how many loads of parts have been
polished. This accessory is essential for tracking the productivity and
quality of the polishing operations being run on the machine.
DE DataLink® Setup
Setup instructions to get started using the DE DataLink® data
collection system with the APM-HDC-5400 Polishing Machine.
1. Connect the polishing machine to the DE DataLink® network by
plugging the ethernet port on the back of the machine into an
ethernet switch that is connected to the DE DataLink® control IPC.
2. Start the DE DataLink® software on the DE DataLink® IPC.
3. On the APM-HDC-5400 polisher, navigate to the “System Config”
tab and select “User Rights and Settings” in the drop-down menu.
4. Once on the “User Rights and Settings” screen select the
DE DataLink® check box to enable the system.
67
DE DataLink® Operations
There are multiple ways to use the DE DataLink® system with the
polisher. It is the end-user’s decision to determine what data needs
to be collected and how they want to utilize the data collection ca-
pabilities of the equipment. All data collection features are optional
to maintain flexibility for the wide variety of needs that are encoun-
tered. The section to follow will outline all the data collection features
available for use.
1. Navigate to the “Home” tab after the DE DataLink® has been
enabled and you will see a field is now available for the operator
to enter his or her name or ID# in the machine. This data field
will be transferred to the database once it is entered into the
machine. By pressing the field a keyboard will appear allowing the
name to be changed by keyboard or by barcode scanner. USB
barcode scanners are available and can be connected via the USB
slots on the sides of the polishing machine.