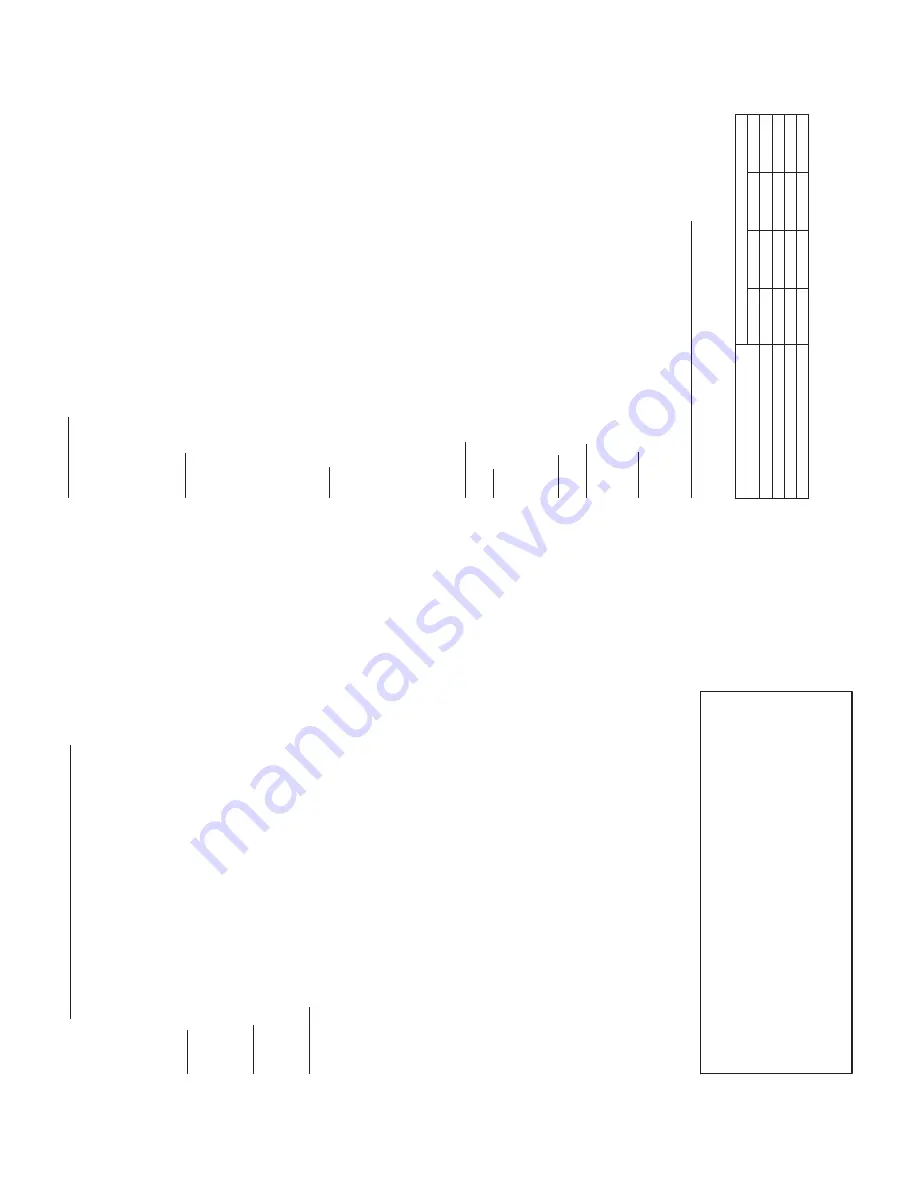
DC Motor Installation – Maintenance Instructions
W
he
n this motor is installed accor
ding to these instructions, it complies with
the EEC Machiner
y
D
irective. Electr
omagnetic Compatibility (EMC)
re
qu
irements for CE compliance ar
e met when the incoming power is pur
el
y
sinusoidal. For other power sour
ce types, r
efer to MN1383 Recommended
Practices for Installation for EC Dir
ective 89/336/EEC Relating to EMC".
These instructions ar
e intended to complement, not r
eplace, the infor
m
at
io
n
in MN605 Installation and Operation manual for Integral Horsepower DC Motor".
Handling
The weight of the motor and shipping container will var
y. Use corr
ec
t
material handling equipment to avoid injur
y.
Use caution when r
emoving the motor fr
om its packaging. Sharp cor
ners
may exist on motor shaft, motor key
, sheet metal and other sur
faces.
Receiving
Inspect the motor for damage befor
e accepting it. The Motor shaft should
ro
tate fr
eely with no rubs.
Repor
t any damage immediately to the
co
m
m
er
cial carrier that deliver
ed your motor
.
Safety Notice
Only qualified personnel trained in the safe installation and operation of this equipment should install this motor
. When impr
operly installed or used,
rotating equipment can cause serious or fatal injur
y. Equipment must be
installed in accor
dance with the National Electrical Code (NEC), local codes
and NEMA MG2 Safety Standar
ds for Construction and Guide for Selection,
Installation and Use of Electric Motors and Generators. Observe the following guidelines: 1.
When eyebolts ar
e pr
ovided, they must be fully tightened and ar
e
intended to lift the motor and its included accessories only
.
2.
G
round the motor accor
ding to NEC and local codes.
3.
Pr
ovide a per
manent guar
d to pr
event accidental contact of body par
ts
or clothing with r
otating or moving par
ts or bur
ns if motor is hot.
4.
Shaft key must be secur
ed befor
e star
ting motor
.
5.
Do not apply power to the motor until the motor is secur
ely mounted by
its mounting holes.
6.
This motor must only be connected to the pr
oper line voltage, line
frequency and load size.
7.
Motors ar
e not to be used for load holding or r
estraining unless a
pr
operly sized brake is installed. If a motor mounted brake is installed,
pr
ovide pr
oper safeguar
ds for personnel in case of brake failur
e.
8.
Disconnect all power services, stop the motor and allow it to cool befor
e
servicing.
9.
For single phase motors, discharge the star
t and/or run capacitors
befor
e servicing.
10
.
Do not by-pass or r
ender inoperative any safety device.
11
.
DC series wound motors must be pr
otected fr
om sudden loss of load
causing overspeed damage. DC shunt wound motors must be pr
otected fr
om loss of field voltage which can r
esult in damage.
12
.
Mounting bolts should be high tensile steel. Be sur
e to use a suitable
locking device on each bolt (spring washer or thr
ead lock compound).
Guarding
After motor installation is complete, a guard of suitable dimensions
must be constructed and installed around the motor/gearmotor
.
This guard must prevent personnel from coming in contact with
any moving parts of the motor or drive assembly but must allow
s
u
fficient cooling air to pass over the motor
.
If a motor mounted brake is installed, provide proper safeguards
for personnel in case of brake failure.
Brush inspection plates and electrical connection cover plates or
lids, must be installed before operating the motor
.
Motor Enclosure
ODP
,
Open drip proof
motors ar
e intended for use in clean, dr
y locations with
adequate supply of cooling air
. These motors should not be used in the
pr
esence of flammable or combustible materials. Open motors can emit
flame and/or molten metal in the event of insulation failur
e.
TEFC,
totally enclosed
motors ar
e intended for use wher
e moistur
e, dir
t
and/or corr
osive materials ar
e pr
esent in indoor and outdoor locations.
Explosion proof
motors, as indicated by the Underwriters Laboratories, Inc.
label ar
e intended for use in hazar
dous ar
eas as specified by the NEC.
Mounting
Foot mounted
machines should be mounted to a rigid foundation to pr
event
excessive vibration. Shims may be used if location is uneven.
Flange mounted
machines should be pr
operly seated and aligned. Note: If
im
pr
oper r
otation dir
ection is detrimental to the load, check r
otation dir
ection
prior to coupling the load to the motor shaft. For
V-belt drive,
mount the sheave pulley close to the motor housing. Allow
clearance for end to end movement of the motor shaft. Do not over
tighten
belts as this may cause pr
ematur
e bearing failur
e or shaft br
eakage.
Direct coupled
machines should be car
efully aligned and the shaft should
rotate fr
eely without binding.
Wiring
Connect the motor as shown in the connection diagram. If this motor is installed as par
t of a motor contr
ol drive system, connect and pr
otect the
motor accor
ding to the contr
ol manufactur
ers diagrams. The wiring, fusing
and gr
ounding must comply with the National Electrical Code and local
codes. When the motor is connected to the load for pr
oper dir
ection of
rotation and star
ted, it should star
t quickly and run smoothly
. If not, stop the
motor immediately and deter
mine the cause. Possible causes ar
e: low
voltage at the motor
, motor connections ar
e not corr
ect or the load is too
heavy
. Check the motor curr
ent after a few minutes of operation and
co
m
pa
re the measur
ed curr
ent with the nameplate rating.
Adjustment
The neutral is adjustable on some motors.
Noise
For specific sound power or pr
essur
e l
evel infor
mation, r
efer to the Acoustic
Pe
rfo
rmance of Standar
d Baldor TEFC or Super E TEFC motors in the Baldor
Mechanical Design Standar
d MD950. The infor
mation is fr
om test r
esults and
should be used with the national safety code for noise in the work place.
V
ibration
This motor is balanced to NEMA MG1, Par
t 7 standar
d.
Lubrication
This is a ball or r
oller bearing motor
. The bearings have been lubricated at
the factor
y. Motors that do not have r
eg
rease capability ar
e factor
y
lubricated for the nor
mal life of the bearings.
Lubricant
Baldor motors ar
e pr
eg
reased, nor
mally with Polyr
ex EM (Exxon Mobil). If
other gr
eases ar
e pr
eferr
ed, check with a local Baldor Service Center f
or
recommendations.
Relubrication Intervals
(For motors with r
egr
ease capability)
New motors that have been stor
ed for a year or mor
e should be r
el
ubricated.
Lubrication is also r
ecommended at these intervals:
T
able 1 Relubrication Interval
NEMA
(IEC
)
Rated Speed (RPM)
NEMA
(IEC)
Frame
Size
3600
1800
1200
900
Up
to
210
incl.
(132)
5500Hrs.
12000Hrs.
18000Hrs.
22000Hrs.
Over
210
to
280
incl.
(180)
3600Hrs.
9500Hrs.
15000Hrs.
18000Hrs.
Over
280
to
360
incl.
(225)
*2200Hrs.
7400Hrs.
12000Hrs.
15000Hrs.
Over
360
to
5000
incl.(300)
*2200Hrs.
3500Hrs.
7400Hrs.
10500Hrs.
* Lubrication interval for 6313 or 6314 bearings that ar
e used in 360 thr
ough
5000 frame, 2 pole motors. If r
oller bearings ar
e used, bearings must be
lubricated mor
e fr
eq
uently
, d
iv
id
e
th
e
relubrication interval
by 2.
276
Содержание MOISTURE Link G2 DP
Страница 1: ...Operation Manual 2019 MODELS MSF DP DPSL DPXSL DPX4T DPX8T DPX12T DPX16GT Grain Dryer Controls...
Страница 2: ......
Страница 4: ...2...
Страница 7: ...GENERAL INSTRUCTIONS 3 5...
Страница 153: ...151...
Страница 154: ...152...
Страница 166: ...164...
Страница 190: ...188...
Страница 200: ...198...
Страница 201: ...199...
Страница 202: ...200...
Страница 203: ...201...
Страница 204: ...202...
Страница 205: ...203...
Страница 206: ...204...
Страница 207: ...205...
Страница 208: ...206...
Страница 209: ...207...
Страница 210: ...208...
Страница 211: ...209...
Страница 212: ...210...
Страница 213: ...211...
Страница 214: ...212...
Страница 215: ...213...
Страница 216: ...214...
Страница 217: ...215...
Страница 218: ...216...
Страница 219: ...217...
Страница 220: ...218...
Страница 221: ...219...
Страница 222: ...220...
Страница 223: ...221...
Страница 224: ...222...
Страница 225: ...223...
Страница 226: ...224...
Страница 227: ...225...
Страница 228: ...226...
Страница 229: ...227...
Страница 242: ...240...
Страница 243: ...241...
Страница 244: ...242...
Страница 245: ...243...
Страница 301: ...56 FIGURE 19 Red jumper wire Red wire...
Страница 302: ...57...
Страница 310: ...2011 Service Manual Rev A 282...
Страница 311: ...2011 Service Manual Rev A 283...
Страница 312: ...2011 Service Manual Rev A 284...
Страница 313: ...2011 Service Manual Rev A 285...
Страница 314: ...2011 Service Manual Rev A 286...
Страница 315: ...2011 Service Manual Rev A 287...
Страница 316: ...2011 Service Manual Rev A 288...
Страница 317: ...2011 Service Manual Rev A 289...
Страница 318: ...2011 Service Manual Rev A 290...
Страница 319: ...2011 Service Manual Rev A 291...
Страница 320: ...2011 Service Manual Rev A 292...
Страница 321: ...2011 Service Manual Rev A 293...
Страница 322: ...2011 Service Manual Rev A 294...