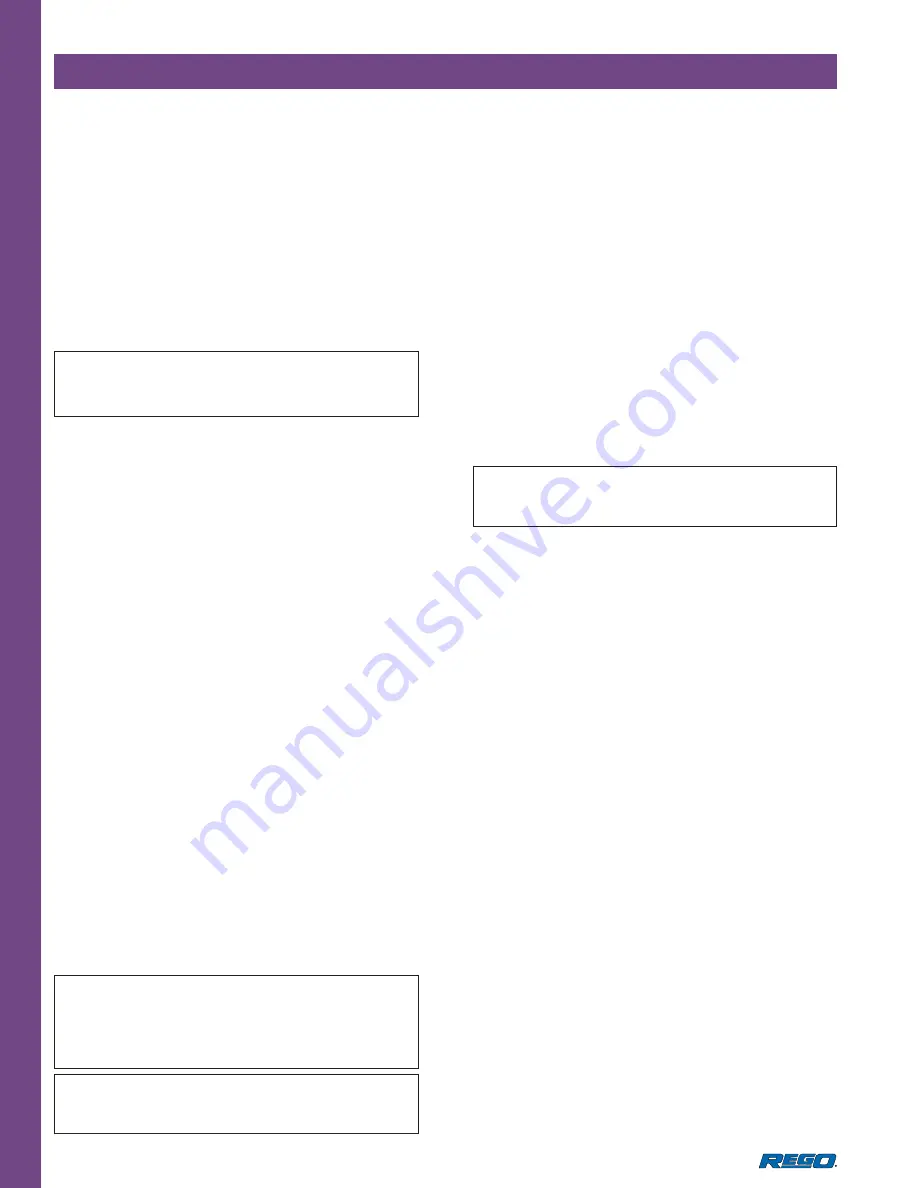
D6
D
100 RegO Dr. P.O. Box 247 Elon, NC 27244 USA www.regoproducts.com Phone (336) 449-7707 Fax (336) 449-6594
Consult NFPA Pamphlet #58 for LP-Gas and ANSI #K61.1 for
anhydrous ammonia, and/or any applicable regulations governing
the application and use of pressure relief valves.
RegO® Pressure Relief Valves
Requirements for Pressure Relief Valves
Every container used for storing or hauling LP-Gas and anhydrous
ammonia must be protected by a pressure relief valve. These
valves must guard against the development of hazardous
conditions which might be created by any of the following:
Ɣ
Hydrostatic pressures due to overfilling or the trapping of
liquid between two points.
Ɣ
High pressures resulting from exposure of the container to
excessive external heat.
Ɣ
High pressures due to the use of incorrect fuel.
Ɣ
High pressures due to improper purging of the container.
Operation of Pressure Relief Valves
Pressure relief valves are set and sealed by the manufacturer to function
at a specific “start-to-discharge” pressure in accordance with regulations.
This set pressure, marked on the relief valve, depends on the design
requirement of the container to be protected by the relief valve. If the
container pressure reaches the start-to-discharge pressure, the relief valve
will open a slight amount as the seat disc begins to move slightly away
from the seat. If the pressure continues to rise despite the initial discharge
through the relief valve, the seat disc will move to a full open position with
a sudden “pop”. This sharp popping sound is from which the term “pop-
action” is derived.
Whether the relief valve opens a slight amount or pops wide open, it will
start to close if the pressure in the container diminishes. After the pressure
has decreased sufficiently, the relief valve spring will force the seat disc
against the seat tightly enough to prevent any further escape of product.
The pressure at which the valve closes tightly is referred to as the “re-seal”
or “blow-down” pressure. Generally, the re-seal pressure will be lower than
the start-to-discharge pressure.The re-seal pressure can be, and in most
cases is, adversely affected by the presence of dirt, rust, scale or other
foreign particles lodging between the seat and disc. They interfere with
the proper mating of the seat and disc and the pressure in the container
will usually have to decrease to a lower pressure before the spring force
embeds foreign particles into the resilient seat disc material and seals
leak-tight. The degree by which the presence of dirt decreases the re-seal
pressure, is, of course, dependent on the size of the interfering particles.
Once particles have been trapped between the disc and seat, the start-
to-discharge pressure is also affected. For example, the pressure relief
valve will start-to-discharge at some pressure lower than its original start-
to-discharge pressure. Again, the pressure at which the valve will start to
discharge is dependent on the size of the foreign particles.
In the case of a pressure relief valve that has opened very slightly due
to a pressure beyond its start-to-discharge setting, the chances of
foreign material lodging between the seat and disc is negligible although
the possibility is always present. If the relief valve continues to leak at
pressures below its start-to-discharge setting it must be replaced.
Relief valves which have “popped” wide open must also be
checked for foreign material lodged between the seat and disc,
as well as for proper reseating of the seat and disc. Continued
leakage at pressures below the start-to-discharge setting indicate
the relief valve must be replaced.
The pressure at which a pressure relief valve will start to discharge
should never be judged by the reading of the pressure gauge
normally furnished on the container.
The reasons for this are two-fold:
Ɣ
If the relief valve is called upon to open, the resulting
discharge produces an increased vaporization of the
product in the container with the result that the liquid cools
to a certain extent and the vapor pressure drops. A reading
taken at this time would obviously not indicate what the
pressure was when the relief valve opened.
Ɣ
The pressure gauges usually on most containers provide
somewhat approximate readings and are not intended to
provide an indication of pressure sufficiently accurate to
judge the setting of the relief valve.
Repair and Testing
RegO® Pressure Relief Valves are tested and listed by
Underwriters Laboratories, Inc., in accordance with NFPA
Pamphlet #58. Construction and performance of RegO®
Pressure Relief Valves are constantly checked at the factory
by U.L. inspectors. Therefore, testing of RegO® Pressure
Relief Valves in the field is not necessary.
Any pressure relief valve which shows evidence of leakage, other
improper operation or is suspect as to its performance must be
replaced immediately using approved procedures.
Pipe-Away Adapters
Pipe-away adapters are available for most RegO® Pressure
Relief Valves, where it is required or desirable to pipe the
discharge above or away from the container. Each adapter
is designed to sever if excessive stress is applied to the vent
piping – thus leaving the relief valve fully operative.
Weep hole deflectors are available on larger relief valves.
These deflectors provide protection against flame impinging
on adjacent containers which could occur from ignition of
LP-Gas escaping through the relief valve drain hole when the
valve is discharging.
Selection of RegO® Pressure Relief Valves For ASME
Containers
The rate of discharge required for a given container is
determined by the calculation of the surface area of the
container as shown in “Chart A” for LP-Gas and “Chart B” for
anhydrous ammonia. See page D9.
Setting - The set pressure of a pressure relief valve depends
upon the design pressure of the container. Refer to NFPA
Pamphlet #58 for more information.
Selection of RegO® Pressure Relief Valves for DOT
Containers
To determine the proper relief valve required for a given
DOT container, refer to the information shown with each
pressure relief valve in the catalog. This information will give
the maximum size (pounds water capacity) DOT container for
which the relief valve has been approved.
Setting - The standard relief valve setting for use on DOT
cylinders is 375 PSIG.
156
Содержание MOISTURE Link G2 DP
Страница 1: ...Operation Manual 2019 MODELS MSF DP DPSL DPXSL DPX4T DPX8T DPX12T DPX16GT Grain Dryer Controls...
Страница 2: ......
Страница 4: ...2...
Страница 7: ...GENERAL INSTRUCTIONS 3 5...
Страница 153: ...151...
Страница 154: ...152...
Страница 166: ...164...
Страница 190: ...188...
Страница 200: ...198...
Страница 201: ...199...
Страница 202: ...200...
Страница 203: ...201...
Страница 204: ...202...
Страница 205: ...203...
Страница 206: ...204...
Страница 207: ...205...
Страница 208: ...206...
Страница 209: ...207...
Страница 210: ...208...
Страница 211: ...209...
Страница 212: ...210...
Страница 213: ...211...
Страница 214: ...212...
Страница 215: ...213...
Страница 216: ...214...
Страница 217: ...215...
Страница 218: ...216...
Страница 219: ...217...
Страница 220: ...218...
Страница 221: ...219...
Страница 222: ...220...
Страница 223: ...221...
Страница 224: ...222...
Страница 225: ...223...
Страница 226: ...224...
Страница 227: ...225...
Страница 228: ...226...
Страница 229: ...227...
Страница 242: ...240...
Страница 243: ...241...
Страница 244: ...242...
Страница 245: ...243...
Страница 301: ...56 FIGURE 19 Red jumper wire Red wire...
Страница 302: ...57...
Страница 310: ...2011 Service Manual Rev A 282...
Страница 311: ...2011 Service Manual Rev A 283...
Страница 312: ...2011 Service Manual Rev A 284...
Страница 313: ...2011 Service Manual Rev A 285...
Страница 314: ...2011 Service Manual Rev A 286...
Страница 315: ...2011 Service Manual Rev A 287...
Страница 316: ...2011 Service Manual Rev A 288...
Страница 317: ...2011 Service Manual Rev A 289...
Страница 318: ...2011 Service Manual Rev A 290...
Страница 319: ...2011 Service Manual Rev A 291...
Страница 320: ...2011 Service Manual Rev A 292...
Страница 321: ...2011 Service Manual Rev A 293...
Страница 322: ...2011 Service Manual Rev A 294...