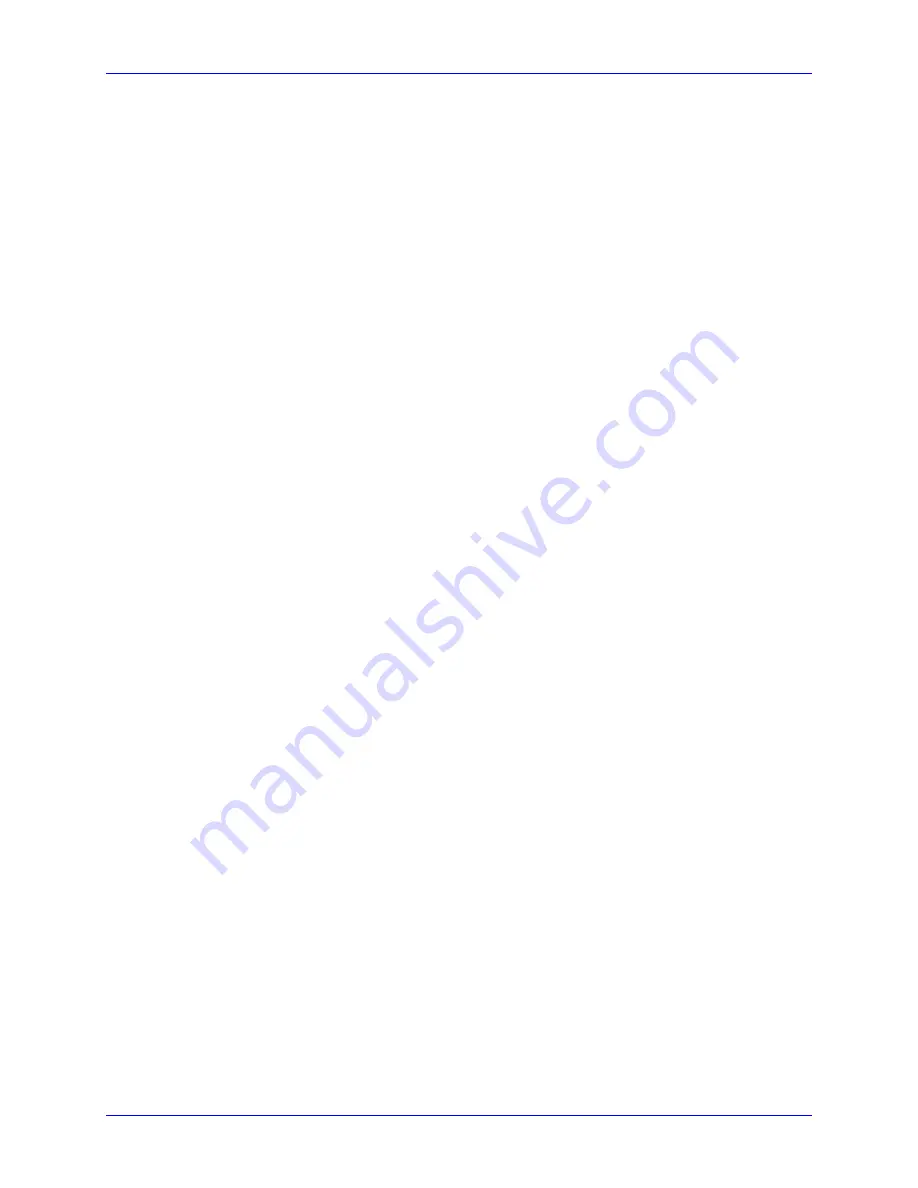
Geo Brick Drive User Manual
Pinouts and Software Setup
158
Motor Selection
The Geo Brick Drive interfaces with a wide variety of motors. It supports virtually any kind of three-
phase AC/DC rotary, linear brushless, or induction motors. Using two out of the three phases, it is also
possible to drive permanent magnet DC brush motors.
Motor Inductance
Digital direct PWM control requires a significant amount of motor inductance to drive the on-off voltage
signals resulting smooth current flow with minimal ripple. Typically, servomotors’ phase inductance
ranges from 2 to 15mH. The lower the inductance, the higher is the suitable PWM frequency.
Low inductance motors (less than 2 mH) can see large ripple currents causing excessive energy waste and
overheating. Additional in-series inductance is recommended in these cases.
High inductance motors (greater than 15 mH) are slower to react and generally not considered high
performance servo motors.
Motor Resistance
Motor resistance is not typically a determining factor in the drive/system performance but rather comes
into play when extracting a desired torque or horsepower out of the motor is a requirement.
Motor Inertia
Motor inertia is an important parameter in motor sizing. Considering the reflected load inertia back to the
motor in this process is important. In general, the higher the motor inertia, the more stable the system will
inherently be. A high ratio of load to motor inertia shrinks the operating bandwidth (gain limited) of the
system, especially in applications using belt or rubber based couplings. The ratio of load to motor inertia
is typically around 3:1. Mechanical gearing is often used to reduce reflected inertial load going back to
the shaft of the motor.
Motor Speed
In some applications, it is realistically impossible to achieve the motors’ specified maximum velocity.
Fundamentally, providing sufficient voltage and proper current-loop tuning should allow attaining motor
maximum speeds. Consider feedback devices being a limitation in some cases, as well as the load
attached to the motor. In general, the maximum speed can be determined dividing the line-to-line input
voltage by the back EMF constant Kb of the motor. Input voltage headroom of about 20% is
recommended for good servo control at maximum speed.
Motor Torque
Torque requirements in an application can be viewed as both instantaneous and average
Typically, the instantaneous or peak torque is the sum of machining, and frictional forces required to
accelerate the inertial load. The energy required to accelerate a load follows the equation T=JA where T is
the torque, J is the inertia, and A is the acceleration. The required instantaneous torque is then divided by
the motor torque constant (Kt) to determine the necessary peak current of the Geo Brick Drive. Headroom
of about 10% is always desirable to account for miscellaneous losses (aging, wear and tear, calculation
roundups).
The continuous torque rating of the motor is bound by thermal limitation. If the motor applies more
torque than the specified threshold, it will overheat. Typically, the continuous torque ceiling is the RMS
current rating of the motor, also known as torque output per ampere of input current.
Содержание Geo Brick
Страница 5: ...4...
Страница 286: ...Geo Brick Drive User Manual Appendix A 286 APPENDIX A Schematic Samples Watchdog X15 Inputs J6 J7...
Страница 287: ...Geo Brick Drive User Manual Appendix A 287 Outputs J6 J7 603793 109 and earlier Outputs J6 J7 603793 10A and later...
Страница 288: ...Geo Brick Drive User Manual Appendix A 288 Limits Flags J4...