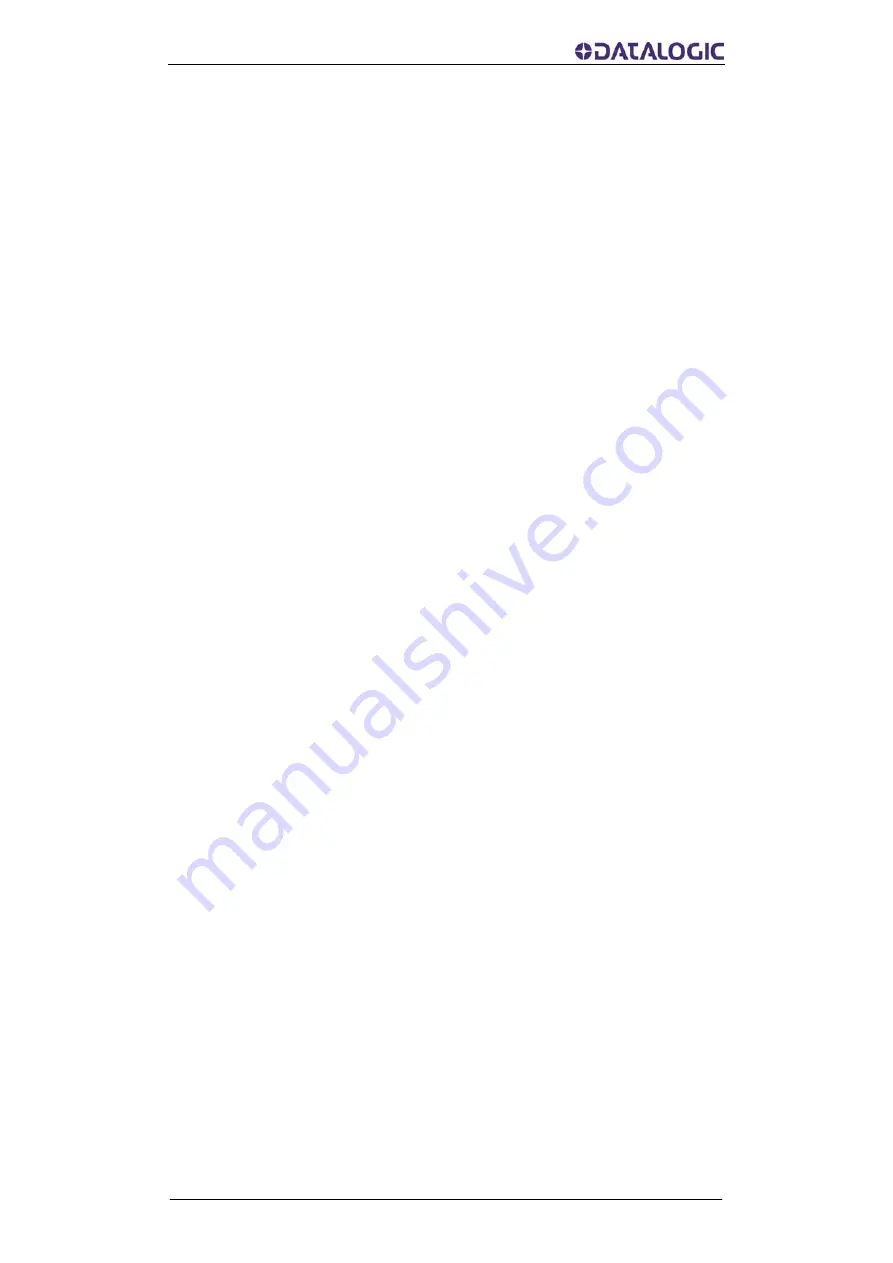
AMT58x-EC EtherCAT®
40
6.1.9 Timing and Synchronization
The main feature of EtherCAT is its almost ideal representation of a
real-time system.
Hence the Master has to synchronize all the Slaves at the same time
in order to build a system where all nodes have the same reference
time; this goal can be achieved by using “distributed clocks”.
Master downloads its clock into one of the salves (customarily the
first Slave) which becomes the reference clock for all the Slaves in
the network; so it has the task of synchronizing the other Slaves.
Master controller periodically sends a special synchronization-
telegram where the reference Slave writes its own “current time”.
This telegram is then sent to all the other Slaves that, in this way,
provide for a new re-synchronization of their own clock in order to
avoid possible drifts.
This synchronization of the reference time is very important in order
to have a snapshot of the system and accordingly to take
simultaneous actions in high sensitive applications such as the
coordination in axis control operations.
Besides, EtherCAT Slave Controller (ESC) is fitted with a
capture/compare unit that provides accurate synchronization signals
(SYNC0 or interrupts): they are sent to the local micro-controller so
that it is able to synchronize its own clock to Slaves clock.
Sync Manager
Sync Manager has the task of synchronizing data transfer between
Master and Slave and prevents the same memory area from being
written by different events.
There are two synchronization modes:
3-Buffer
Mode;
1-Buffer Mode.
Synchronisation mode is initialized through the XML file or by loading
data directly from EEPROM (SII).
Buffered Mode (3-Buffer Mode)
In this mode new data can be accessed at any time by both Master
EtherCAT and ESC controllers; no timing restrictions are imposed.
Three buffers are necessary (three consecutive memory areas); one
buffer is always available to ESC controller for writing and one buffer
always contains updated data to be read by the Master.
Customarily this is used for process data communication.
Mailbox Mode (1-Buffer Mode)
In this mode a “handshake” between Master and Slave must be
used; in fact one only memory buffer is available to both Master and
Slave for writing and reading; the Master (or the Slave) is enabled to
write only when the buffer is empty, that is when the Slave (or the
Master) has finished reading the data buffer. And vice versa: the
Master (or the Slave) is enabled to read only when the buffer is
empty, that is when the Slave (or the Master) has finished writing the
data buffer.
Содержание AMT58 Series
Страница 1: ......
Страница 8: ......
Страница 13: ...AMT58x CB CANopen 5 3 1 3 Fissaggio con flangia codice ST 58 FLNG ...
Страница 52: ......
Страница 55: ...Subject index ...
Страница 62: ...AMT58x PB Profibus 5 3 1 3 Installation using a flange code ST 58 FLNG ...
Страница 101: ......
Страница 102: ......
Страница 109: ......
Страница 114: ...AMT58x EC EtherCAT 5 3 1 3 Installation using a flange code ST 58 FLNG ...
Страница 166: ......
Страница 167: ...AMT58 PN INSTRUCTION MANUAL Absolute Encoders ...
Страница 179: ...INSTRUCTION MANUAL xiii SFC System function TCP Transmission Control Protocol TMAPC Master Application Cycle Time ...
Страница 180: ...LIST OF ABBREVIATIONS xiv AMT58 PN ...
Страница 213: ...RESETTING THE PARAMETERS TO THE DEFAULT FACTORY VALUES INSTRUCTION MANUAL 33 Figure 15 Encoder reset ...
Страница 221: ...TO TECHNOLOGY OBJECTS INSTRUCTION MANUAL 41 Figure 28 TO encoder enabled ...
Страница 231: ...INSTRUCTION MANUAL 51 ...
Страница 255: ...REAL TIME CLASS 3 IRT_TOP RT3 INSTRUCTION MANUAL 75 Figure 5 Telegram 81 IN Figure 6 Telegram 81 OUT ...
Страница 265: ...NORMAL OPERATION DIAGRAM INSTRUCTION MANUAL 85 NORMAL OPERATION DIAGRAM ...
Страница 266: ...ENCODER STATE MACHINE 86 AMT58 PN PRESET DIAGRAM ...
Страница 267: ...PARKING SENSOR DIAGRAM INSTRUCTION MANUAL 87 PARKING SENSOR DIAGRAM ...
Страница 268: ...ENCODER STATE MACHINE 88 AMT58 PN ERROR DIAGRAM Acknowledgment of acknowledgeable sensor error ...
Страница 269: ...ERROR DIAGRAM INSTRUCTION MANUAL 89 Acknowledgment of not acknowledgeable sensor error ...
Страница 284: ......
Страница 285: ......
Страница 287: ......
Страница 294: ......
Страница 299: ...AMT58x CB CANopen 5 3 1 3 Installation using a flange code ST 58 FLNG ...
Страница 335: ......
Страница 345: ...AMT58x DN DeviceNET 5 3 1 3 Installation using a flange code ST 58 FLNG ...
Страница 380: ...AMT58x DN DeviceNET 40 Default 21h ...
Страница 384: ...AMT58x DN DeviceNET 44 Default 00h ...
Страница 394: ......
Страница 404: ...AMT58x PB Profibus 5 3 1 3 Installation using a flange code ST 58 FLNG ...