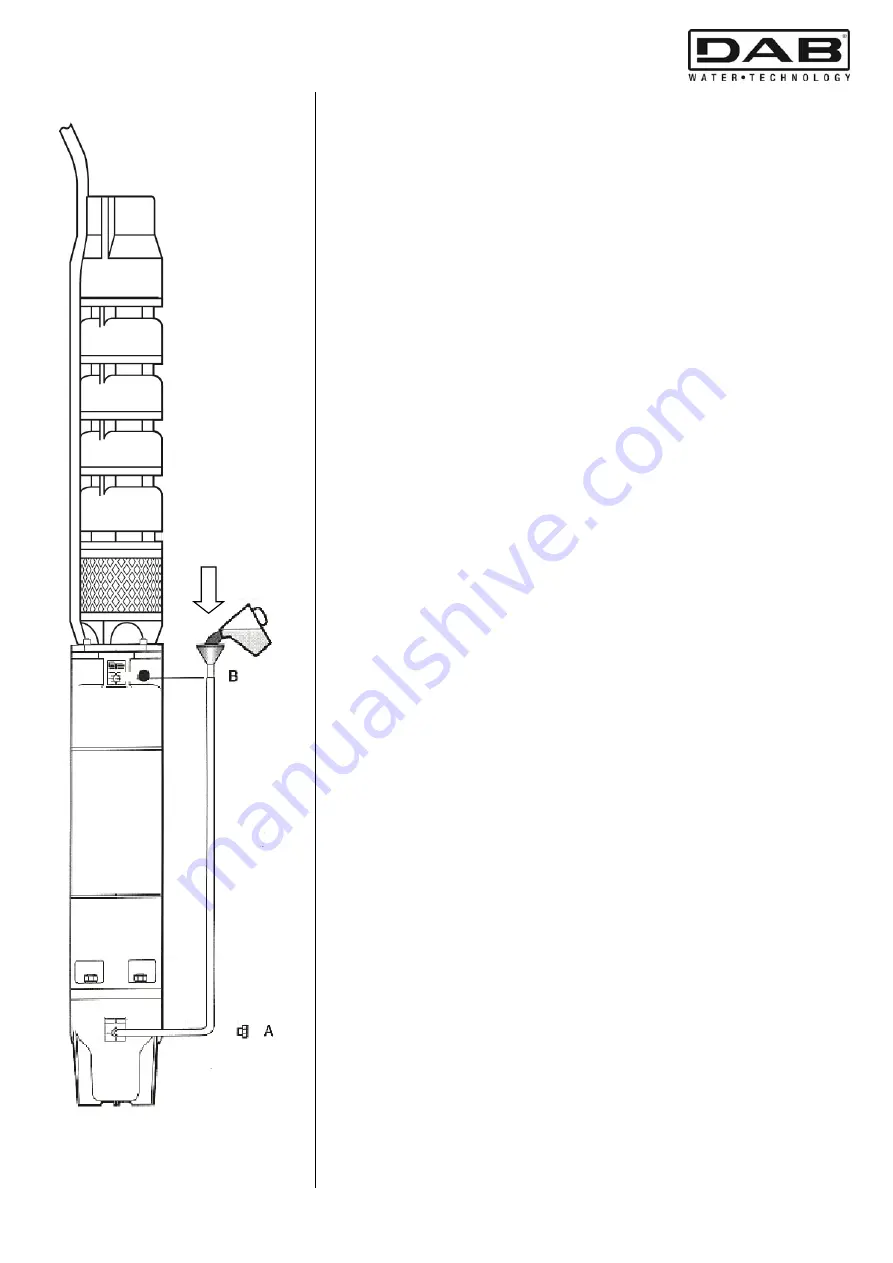
ENGLISH
27
Figure 7
6. INSTALLATION
For what concerns pump handling at the installation site, please refer to
section.4.2.
Clean the well from sand or grit by applying the normal cleaning
procedures.
Place the pumping unit at the top of the well, fasten it to the hoist hook and
fill the motor as follows:
a) Place the motor in vertical position.
b) Remove filling plug (A) and replace it with the nipple equipped with
pipe and funnel delivered with the motor.
c) Remove vent plug (B) to bleed the air possibly trapped in the motor.
d) Holding the funnel higher than the vent valve, pour clear water in the
motor until the mixture already in starts dropping from the vent valve.
e) Stop pouring water in the motor, screw valve (B) plug back in place,
remove the nipple and screw valve (A) plug back in place.
The group should never run without being filled, since pump bearings are
lubricated by the pumped fluid.
Dry running should be absolutely avoided even for a very short period,
since it might heavily damage the pump.
Also, the pump should not rest on the well bottom as the motor would run
in a high sand-concentration environment with a dangerous reduction of its
cooling capacity and probable windings burn-out.
Check cable connection to the control panel terminals. Check also the
calibration of thermal protection relays, which should be set according to
rated break power.
Disconnect the group from main electric supply before lowering it in the
well.
Fasten accurately the cable far end as the cable might fall in the well.
Lower then the electric pump into the well with the help of two supporting
brackets placed alternately on the pump column pipe.
Proceed in the following way:
a) Connect the first column section to the pump delivery nozzle after
having placed a splitted supporting bracket at the opposite end of the
pipe. In case of threaded column pipes, place by the upper end the
suited threaded sleeve to avoid possible sliding between pipe and
bracket.
b) Move the assembly with a hoist and lower it till the bracket will rest on
the well opening.
c) Fasten every 2 or 3 meters the electric supply cables to the pump
column by means of suited bands. We recomend a firm fastening,
since slacken cables will tend to slide down along the pipe due to their
own weight, creating loose, bending sections which could violently rub
against the well internal walls at pump startup and stopping.
d) Connect the second column pipe, that too coupled to a supporting
bracket at its top.
e) Keep the assembly lifted and remove the first supporting bracket, then
lower the unit as described at point (b).
f)
Repeat this operation till reaching the desired depth. The unit should
be submersed for at least f or 2 meters below the water dynamic level,
such however to fulfil its NPSH requirements. The water level, for
seasonal drop or for an excessive pump delivery compared to well
feeding, should never be lower than the pump suction chamber, as
that could cause driving bushes seizing and motor overheating. Check
the length of the column pipe while lowering the unit, to make sure the
unit is installed at the right depth. Definitive fastening is performed by
welding and bolting the last pipe flange to the well opening. In case of
threaded pipes, these have to be completely tightened and possibly
locked since the group reaction torque at startup could make them
loose.
ONLY FOR TR 6 - 8 - 10 - 12 MOTORS