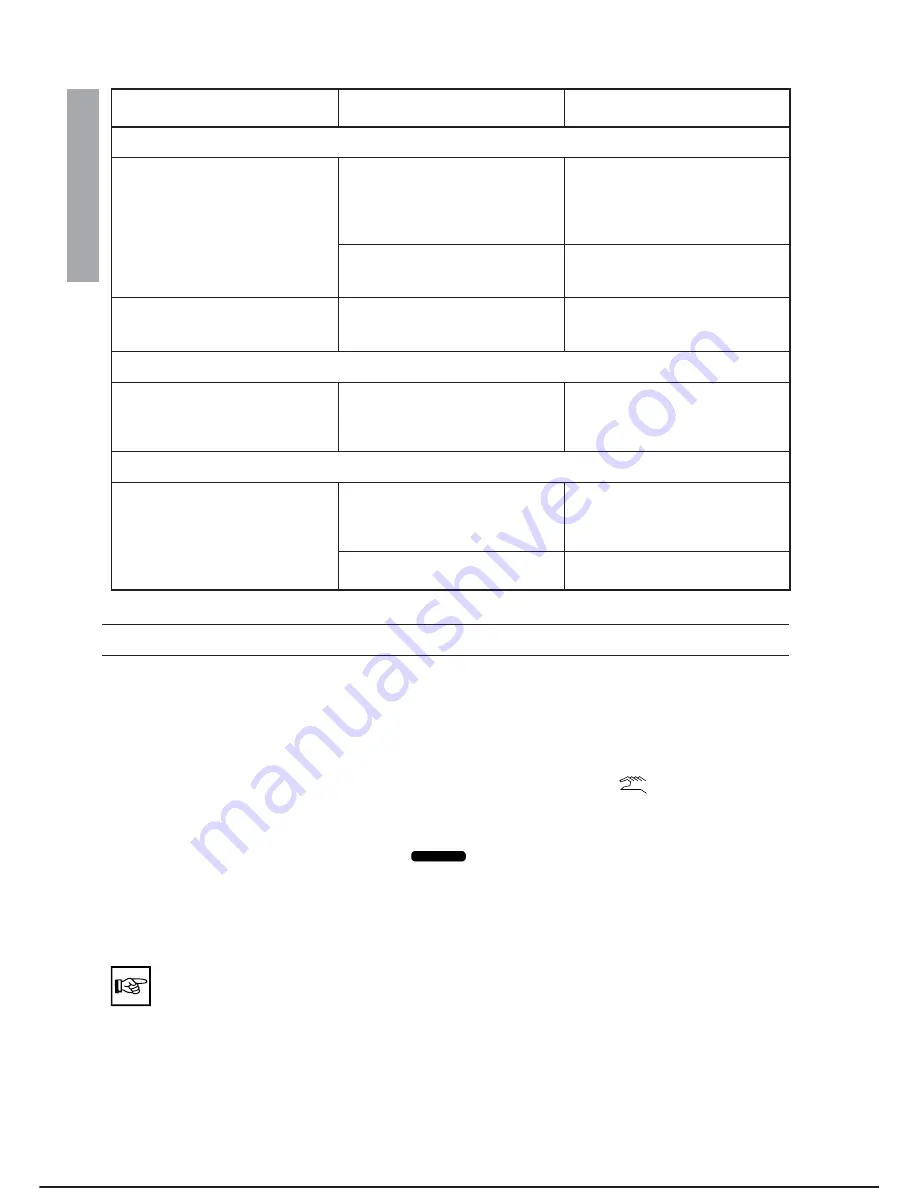
Fault
Check
Suggestions/Possible causes
3. Checking manual robot movement
The axis intended to be moved is
still
Check that: the Enabling Device
button is pressed and the motors
are on DRIVE ON (led on); the but-
ton of the axis to be moved is
pressed
Incorrect pressing of buttons, keys
or sequence of commands
If the clamping brackets for trans-
porting the robot have been re-
moved
Remove the brackets
The axis to be moved moves badly Check the mechanical geometry of
the axis for distortion or interfer-
ence
Removed the damaged robot parts
4. Checking TURN_SET
Difficulty in performing the opera-
tion
Correct command sequence and
correct robot positioning
Carry out the procedure carefully
following the instructions. Consult
chapter 3 of this manual for further
information about commands
5. Check the robot calibration position
The robot does not position cor-
rectly in the calibration position
(fixed and mobile indexes mis-
aligned, on all or on some axes)
Check that the controller is the one
associated with the robot con-
nected
(serial
numbers
corre-
sponding)
Correctly associate controller and
robot
Check that the robot geometry has
no distortions or interferences
Replace the damaged robot parts
This step of the procedure must be carried out if the word TURN appears in the PTU4 status window. TURN
may be shown following movement of one or more axes of the robot with the C3G
Plus
CONTROL UNIT off.
If TURN is not shown on the PTU4 carry out the next step of the procedure.
PROCEDURE
1.
Set the status selector on the control panel to the PROGRAMMING position
2.
On the PTU4 select the JNT type of movement using the TYP key
3.
Reduce the robot speed to 20% using the
key
4.
Pressing the PTU4 Enabling Device button the robot motors turn on (green led lit in correspondence
with the DRIVE ON button)
5.
Position the robot aligning the reference notches (fixed and mobile index) of the axis on which Turn_set
is to be performed using the key corresponding to the axis.
After executing the CAT command (Configure Arm Turn_Set) the following messages may
appear: Joints position insufficiently accurate and/or Negative (positive) adjustment is
required. In which case position the robot on the reference notches more accurately, as de-
scribed.
6.
From the PTU4 command menu execute: Conf (F1) Arm (F1) Turn (F3)
7.
Repeat the operation on all the robot axes.
INSTALLATION
C3G
Plus
2-18
08/0702
-
+
%
11. TURN_SET OPERATION
INSTALLATION
10.
Содержание C3G Plus
Страница 6: ...This page has been intentionally blank UPDATING LIST C3G Plus D 08 0702 ...
Страница 7: ...C3G Plus PREFACE 05 1199 i PREFACE C3G Plus VERSIONS SDLP SDMP SDHP C3G Plus VERSIONS DDMP DDHP ...
Страница 14: ...This page has been intentionally blank Operations and Maintenance Manual C3G Plus ...
Страница 22: ...This page has been intentionally blank SAFETY REGULATIONS C3G Plus 1 8 02 1299 SAFETY REGULATIONS ...
Страница 24: ...This page has been intentionally blank Operations and Maintenance Manual C3G Plus ...
Страница 26: ...This page has been left intentionally blank INSTALLATION C3G Plus 2 ii 01 0498 SUMMARY ...
Страница 48: ...This page has been intentionally blank Operations and Maintenance Manual C3G Plus ...
Страница 61: ...SAMPLE CONNECTION OF C3G EMC2 C3G Plus OPERATOR INTERFACE 07 1200 3 13 EMERGENCY CONTROL C3G EMC2 ...
Страница 120: ...This page has been left intentionally blank OPERATOR INTERFACE C3G Plus 3 72 05 1199 C3G Plus KIT IVECO ...
Страница 122: ...This page has been intentionally blank Operations and Maintenance Manual C3G Plus ...
Страница 127: ...C3G Plus INTEGRATION GUIDE 06 0400 4 5 SYSTEM I O ...
Страница 143: ...Additional I O modules C3G Plus INTEGRATION GUIDE 01 0498 4 21 parallel i o additional modules ...
Страница 158: ...This page has been intentionally blank INTEGRATION GUIDE C3G Plus 4 36 06 0400 SERIAL I O AND PDL2 TOOLS ...
Страница 160: ...This page has been intentionally blank Operations and Maintenance Manual C3G Plus ...
Страница 182: ...This page has been intentionally blank Operations and Maintenance Manual C3G Plus ...
Страница 188: ...This page has been intentionally blank Operations and Maintenance Manual C3G Plus ...
Страница 190: ...This page has been left intentionally blank MAINTENANCE C3G Plus 7 ii 00 1097 GENERAL RULES ...
Страница 192: ...This page has been left intentionally blank MAINTENANCE C3G Plus 7 2 00 1097 PREVENTIVE MAINTENANCE ...
Страница 195: ...Main C3G Plus Connections C3G Plus MAINTENANCE 08 0702 7 5 FUNCTIONAL LAYOUTS C3G Plus sdlp sdmp sdhp VERSIONS ...
Страница 198: ...Axes Control Circuit MAINTENANCE C3G Plus 7 8 00 1097 FUNCTIONAL LAYOUTS C3G Plus sdlp sdmp sdhp VERSIONS ...
Страница 205: ...Power Supply Distribution Page 1 of 2 C3G Plus MAINTENANCE 01 0498 7 15 FUNCTIONAL LAYOUTS C3G Plus ddmp VERSIONS ...
Страница 206: ...Power Supply Distribution Page 2 of 2 MAINTENANCE C3G Plus 7 16 01 0498 FUNCTIONAL LAYOUTS C3G Plus ddmp VERSIONS ...
Страница 207: ...Machine 1 Axes Control Circuit C3G Plus MAINTENANCE 01 0498 7 17 FUNCTIONAL LAYOUTS C3G Plus ddmp VERSIONS ...
Страница 208: ...Machine 2 Axes Control Circuit MAINTENANCE C3G Plus 7 18 04 0799 FUNCTIONAL LAYOUTS C3G Plus ddmp VERSIONS ...
Страница 209: ...Serial and Parallel Line Connections C3G Plus MAINTENANCE 04 0799 7 19 FUNCTIONAL LAYOUTS C3G Plus ddmp VERSIONS ...
Страница 221: ...SAFETY CIRCUIT TEST DEVICES Connector X113 test device C3G Plus MAINTENANCE 04 0799 7 31 diagnostic C3G Plus ...
Страница 225: ...X30 connector test device C3G Plus MAINTENANCE 01 0498 7 35 diagnostic ...
Страница 232: ...This page has been left intentionally blank MAINTENANCE C3G Plus 7 42 00 1097 CIRCUIT DIAGRAMS ...
Страница 255: ...SOFTWARE OPERATIONS FOR CONTROLLER REPLACEMENT 2 2 C3G Plus MAINTENANCE 01 0498 7 65 SYSTEM SOFTWARE ...
Страница 264: ...This page has been intentionally blank 7 74 08 0702 MAINTENANCE C3G Plus LIST OF SPARE PARTS ...
Страница 265: ...OPERATOR S NOTES C3G Plus NOTES ...
Страница 266: ...C3G Plus NOTES ...