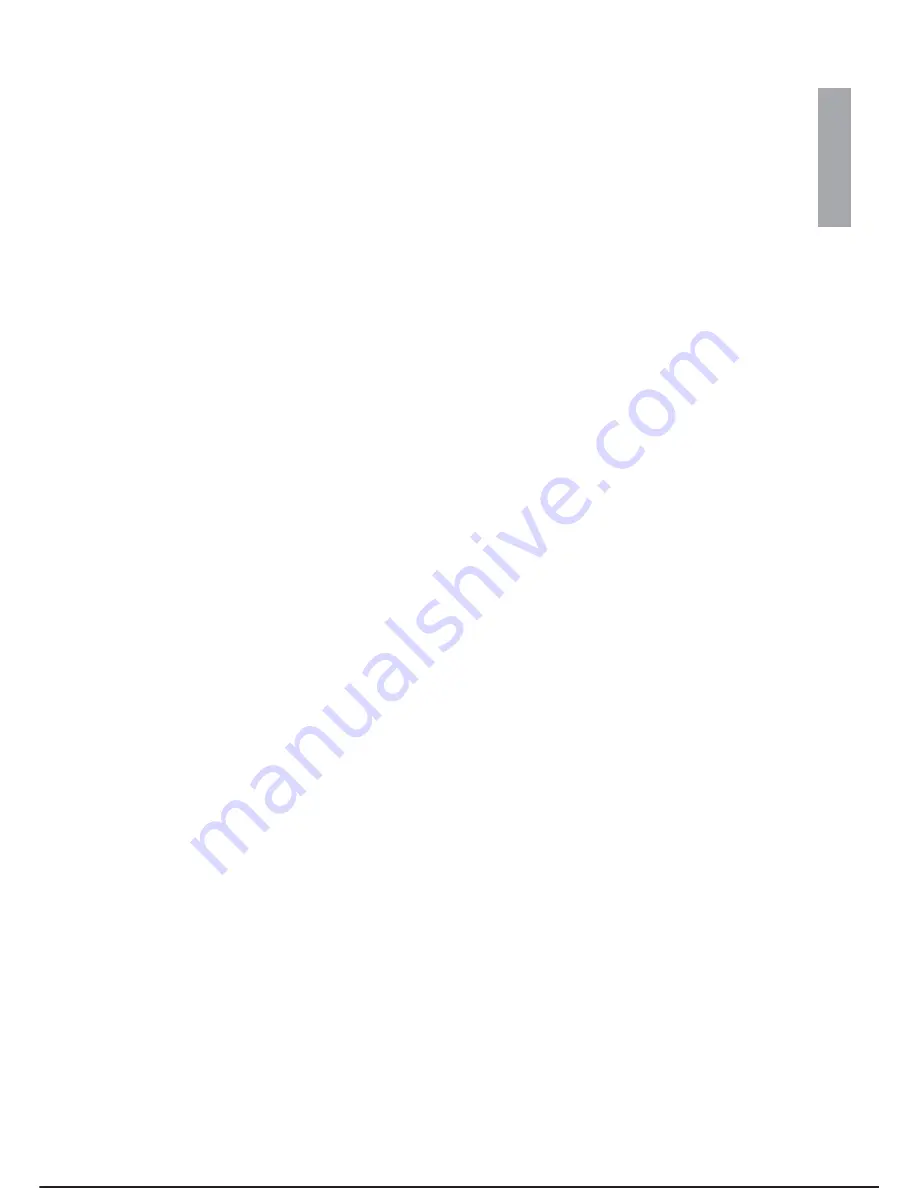
CALIBRATION
This paragraph describes the calibration and Turn-set procedures that can be carried out using the controller
and examines the subject of calibration in detail.
The basic concepts, the terminology used and the internal mechanisms for handling axis position information
are given below.
TERMINOLOGY
·
AXIS POSITIONAL VALUE: the axis positional value contains all the information necessary to determine
the exact position of an axis in space; it is handled by the control unit using information contained in 32
bits.
·
FLASH EPROM: is a memory used to save the characteristic information about the robot associated
with the controller, the calibration constant values and the length of the levers and other parameters for
use of the emergency terminal without the optional RPT module.
·
RPT module: the RPT (Resolver Position Tracker) module is an optional microprocessor device housed
at the base of the robot. Its main functions are:
- counting resolver revolutions for eight axes;
- containing the specifications of the robot to which it is associated, the calibration constants, the length
of the levers and other parameters for the emergency terminal;
This module makes the robot ABSOLUTE, as the data stored in it are retained even in the case of a power
failure. If this module is not operative when the controller is turned on, the revolution count cannot be re-
called.
The C3G controller handles a system without RPT. At system restart, the controller checks that the values
read from the resolver are the same as those read before switching off (either with a warm/cold restart or af-
ter a power failure). If the values correspond, the machine is considered calibrated. If they do not corre-
spond, a Turn_set procedure will be necessary.
Note that no check is performed on the resolver turn numbers. For this reason, the user is advised to put the
arm in the DRIVE OFF state before switching the system off.
·
RECONSTRUCTION OF THE AXIS POSITIONAL VALUE: when the controller is turned on, the system
software reconstructs the axes positional values among the various initialisations.
The system software verifies this value checking that the difference between the reconstructed position
and the position before switching off is below a threshold. If the threshold is exceeded, the controller dis-
plays the 59411 SAX: motion after switchoff error and the operator is responsible for checking that the
physical position of the robot corresponds to the new value.
·
CALIBRATION POSITION: the calibration position is the value that the positional value of the axis must
have. The calibration position is a “joint type” reference position in the robot working space.
·
CALIBRATION CONSTANTS (or calibration error): a calibration constant is the difference between the
data read by the resolver and the theoretical position that the resolver should have in that particular ro-
bot position. In fact, as positioning of the resolver in relation to the robot joint is random, the real position
of the resolver must be corrected according to the theoretical position required for the joint. The calibra-
tion constant is contained inside the resolver revolution. It is described in the variable $CAL_DATA and
can be read using the command CAV (Configure, Arm, View_cal).
·
NUMBER OF RESOLVER REVOLUTIONS: the number of revolutions is pre-set by the calibration oper-
ation.
·
SYSTEM CALIBRATION: the purpose of this calibration procedure is to establish the position of the
axes of a robot comparing this to an ideal robot. This makes it possible to interchange robots of the
same type (if explicitly allowed) and assures universal applicability of the programmes they use.
C3G
Plus
MAIN OPERATIONS FOR SYSTEM USE
00/1097
5-13
CALIBRATION
Содержание C3G Plus
Страница 6: ...This page has been intentionally blank UPDATING LIST C3G Plus D 08 0702 ...
Страница 7: ...C3G Plus PREFACE 05 1199 i PREFACE C3G Plus VERSIONS SDLP SDMP SDHP C3G Plus VERSIONS DDMP DDHP ...
Страница 14: ...This page has been intentionally blank Operations and Maintenance Manual C3G Plus ...
Страница 22: ...This page has been intentionally blank SAFETY REGULATIONS C3G Plus 1 8 02 1299 SAFETY REGULATIONS ...
Страница 24: ...This page has been intentionally blank Operations and Maintenance Manual C3G Plus ...
Страница 26: ...This page has been left intentionally blank INSTALLATION C3G Plus 2 ii 01 0498 SUMMARY ...
Страница 48: ...This page has been intentionally blank Operations and Maintenance Manual C3G Plus ...
Страница 61: ...SAMPLE CONNECTION OF C3G EMC2 C3G Plus OPERATOR INTERFACE 07 1200 3 13 EMERGENCY CONTROL C3G EMC2 ...
Страница 120: ...This page has been left intentionally blank OPERATOR INTERFACE C3G Plus 3 72 05 1199 C3G Plus KIT IVECO ...
Страница 122: ...This page has been intentionally blank Operations and Maintenance Manual C3G Plus ...
Страница 127: ...C3G Plus INTEGRATION GUIDE 06 0400 4 5 SYSTEM I O ...
Страница 143: ...Additional I O modules C3G Plus INTEGRATION GUIDE 01 0498 4 21 parallel i o additional modules ...
Страница 158: ...This page has been intentionally blank INTEGRATION GUIDE C3G Plus 4 36 06 0400 SERIAL I O AND PDL2 TOOLS ...
Страница 160: ...This page has been intentionally blank Operations and Maintenance Manual C3G Plus ...
Страница 182: ...This page has been intentionally blank Operations and Maintenance Manual C3G Plus ...
Страница 188: ...This page has been intentionally blank Operations and Maintenance Manual C3G Plus ...
Страница 190: ...This page has been left intentionally blank MAINTENANCE C3G Plus 7 ii 00 1097 GENERAL RULES ...
Страница 192: ...This page has been left intentionally blank MAINTENANCE C3G Plus 7 2 00 1097 PREVENTIVE MAINTENANCE ...
Страница 195: ...Main C3G Plus Connections C3G Plus MAINTENANCE 08 0702 7 5 FUNCTIONAL LAYOUTS C3G Plus sdlp sdmp sdhp VERSIONS ...
Страница 198: ...Axes Control Circuit MAINTENANCE C3G Plus 7 8 00 1097 FUNCTIONAL LAYOUTS C3G Plus sdlp sdmp sdhp VERSIONS ...
Страница 205: ...Power Supply Distribution Page 1 of 2 C3G Plus MAINTENANCE 01 0498 7 15 FUNCTIONAL LAYOUTS C3G Plus ddmp VERSIONS ...
Страница 206: ...Power Supply Distribution Page 2 of 2 MAINTENANCE C3G Plus 7 16 01 0498 FUNCTIONAL LAYOUTS C3G Plus ddmp VERSIONS ...
Страница 207: ...Machine 1 Axes Control Circuit C3G Plus MAINTENANCE 01 0498 7 17 FUNCTIONAL LAYOUTS C3G Plus ddmp VERSIONS ...
Страница 208: ...Machine 2 Axes Control Circuit MAINTENANCE C3G Plus 7 18 04 0799 FUNCTIONAL LAYOUTS C3G Plus ddmp VERSIONS ...
Страница 209: ...Serial and Parallel Line Connections C3G Plus MAINTENANCE 04 0799 7 19 FUNCTIONAL LAYOUTS C3G Plus ddmp VERSIONS ...
Страница 221: ...SAFETY CIRCUIT TEST DEVICES Connector X113 test device C3G Plus MAINTENANCE 04 0799 7 31 diagnostic C3G Plus ...
Страница 225: ...X30 connector test device C3G Plus MAINTENANCE 01 0498 7 35 diagnostic ...
Страница 232: ...This page has been left intentionally blank MAINTENANCE C3G Plus 7 42 00 1097 CIRCUIT DIAGRAMS ...
Страница 255: ...SOFTWARE OPERATIONS FOR CONTROLLER REPLACEMENT 2 2 C3G Plus MAINTENANCE 01 0498 7 65 SYSTEM SOFTWARE ...
Страница 264: ...This page has been intentionally blank 7 74 08 0702 MAINTENANCE C3G Plus LIST OF SPARE PARTS ...
Страница 265: ...OPERATOR S NOTES C3G Plus NOTES ...
Страница 266: ...C3G Plus NOTES ...