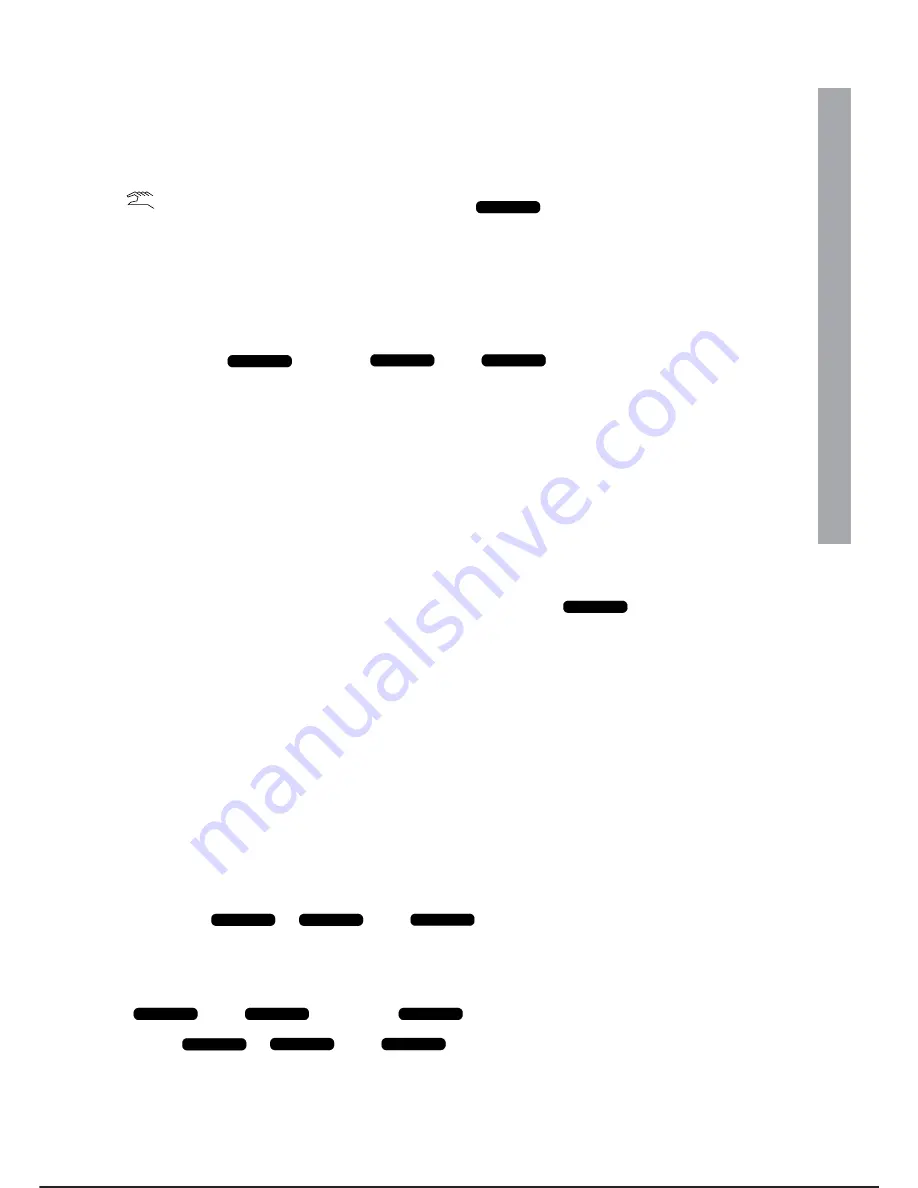
The procedure for manually moving the arms of a robotised cell differs slightly depending on the configura-
tion of the cell controller. The following paragraphs give further details for a few typical situations.
MANUAL MOVEMENT OF A SINGLE ARM SYSTEM
To perform manual movement of a single arm, simply set the status selector to the programming position
choose the most appropriate mode and press the
keys keeping the enable button on the
programming terminal pressed.
MANUAL MOVEMENT OF AUXILIARY AXES, SLIDES AND REVOLVING UPRIGHTS
The auxiliary axes can be added to an arm to move positioners of different kinds, thereby increasing the
working space. Another example of auxiliary axis is the welding gun for powered spot welding.
Manual movement of an auxiliary axis is normally possible only in the joints mode (Jnt) using the corre-
sponding keys
(typically
and
). However, if the auxiliary axis moves a
slide, an upright or an integrated gun, it is possible to carry out the axis movement also in the Cartesian
modes (Tol, Usr, Bas) using the same Jnt mode keys. For the integrated slide and upright see further details
in the C3G Programming guide manual.
MANUAL MOVEMENT WITH CONTROLLER MULTI-ARM CONFIGURATION
In the case of controller multi-arm configuration, it is necessary to choose the arm intended to be moved
pressing the ARM key and checking the current value on the programming terminal status window. Selection
can be done in the programming status, if the Drives are active (DRIVE ON) when the key is pressed, the
system switches to DRIVE OFF.
It is also possible to activate two arms belonging to two different machines at the same time. To do this it is
necessary to be in DRIVE OFF status and press the SHIFT key together with the ARM key. The program-
ming terminal status window will show the codes of the two arms separated by an arrow (for example 1
¬
2).
At the next DRIVE ON both arms are activated. The movement keys
will however be enabled to
move only the arm indicated by the arrow on the status line (arm 1 if 1
¬
2 and arm 2 if 1
®
2). It is possible
to change the direction of the arrow pressing the ARM key in DRIVE ON status (it has this function only if the
arms were both in DRIVE ON).
For manual movement of integrated arms (a particular case of the multi-arm system), see the special chapter
in the C3G Programming guide manual.
MANUAL MOVEMENT IN WRIST_JNT MODE
In movement of certain types of arms in the Cartesian mode (Tol, Usr, Bas) it is easier to change the direc-
tion of the tool in a mode that does not produce rotation around a Cartesian axis but directly moves the robot
wrist axes (for a robot with 6 axes, the wrist axes are the last three). This is typically helpful for machines
with less than six axes as their capability to turn the tool is limited and it is not possible to obtain require-
ments exactly. This mode can be selected pressing the SHIFT key together with TYP key. This operation
changes the behaviour of the Tol, Usr, Bas modes and because of this, also the corresponding abbrevia-
tions change into Twr, Uwr, Bwr. The Jnt mode remains unchanged.
The difference in the movement of the robot more clearly involves the keys dedicated to changing the geom-
etry, i.e. the
,
and
keys. In the Twr, Uwr and Bwr modes these keys
are associated directly with each axis of the wrist and pressing one of them moves the corresponding axis
leaving the position of the other wrist axes unchanged. However, this operation does not change the position
of the TCP as the first three axes move to compensate the change in direction. It should be noted that if the
robot possesses only two wrist axes (for example 4 and 5) it will only be possible to activate keys
and
, while only
will be usable for a robot with four axes. With regard
to keys
,
and
the difference is less apparent: movement is linear in
the direction required but the tool geometry is not constant during the path as the wrist axes are not moved.
The only model of robot that is an exception to this is the SMART S3 robot for which the first three keys pro-
duce the same effect as the normal modes (Tol, Usr, Bas).
C3G
Plus
MAIN OPERATIONS FOR SYSTEM USE
00/1097
5-7
ROBOT
MOVEMENT
IN
PROGRAMMING
STATUS
-
+
-
+
-
+
7
-
+
8
-
+
-
+
4
-
+
5
-
+
6
-
+
4
-
+
5
-
+
4
-
+
1
-
+
2
-
+
3
Содержание C3G Plus
Страница 6: ...This page has been intentionally blank UPDATING LIST C3G Plus D 08 0702 ...
Страница 7: ...C3G Plus PREFACE 05 1199 i PREFACE C3G Plus VERSIONS SDLP SDMP SDHP C3G Plus VERSIONS DDMP DDHP ...
Страница 14: ...This page has been intentionally blank Operations and Maintenance Manual C3G Plus ...
Страница 22: ...This page has been intentionally blank SAFETY REGULATIONS C3G Plus 1 8 02 1299 SAFETY REGULATIONS ...
Страница 24: ...This page has been intentionally blank Operations and Maintenance Manual C3G Plus ...
Страница 26: ...This page has been left intentionally blank INSTALLATION C3G Plus 2 ii 01 0498 SUMMARY ...
Страница 48: ...This page has been intentionally blank Operations and Maintenance Manual C3G Plus ...
Страница 61: ...SAMPLE CONNECTION OF C3G EMC2 C3G Plus OPERATOR INTERFACE 07 1200 3 13 EMERGENCY CONTROL C3G EMC2 ...
Страница 120: ...This page has been left intentionally blank OPERATOR INTERFACE C3G Plus 3 72 05 1199 C3G Plus KIT IVECO ...
Страница 122: ...This page has been intentionally blank Operations and Maintenance Manual C3G Plus ...
Страница 127: ...C3G Plus INTEGRATION GUIDE 06 0400 4 5 SYSTEM I O ...
Страница 143: ...Additional I O modules C3G Plus INTEGRATION GUIDE 01 0498 4 21 parallel i o additional modules ...
Страница 158: ...This page has been intentionally blank INTEGRATION GUIDE C3G Plus 4 36 06 0400 SERIAL I O AND PDL2 TOOLS ...
Страница 160: ...This page has been intentionally blank Operations and Maintenance Manual C3G Plus ...
Страница 182: ...This page has been intentionally blank Operations and Maintenance Manual C3G Plus ...
Страница 188: ...This page has been intentionally blank Operations and Maintenance Manual C3G Plus ...
Страница 190: ...This page has been left intentionally blank MAINTENANCE C3G Plus 7 ii 00 1097 GENERAL RULES ...
Страница 192: ...This page has been left intentionally blank MAINTENANCE C3G Plus 7 2 00 1097 PREVENTIVE MAINTENANCE ...
Страница 195: ...Main C3G Plus Connections C3G Plus MAINTENANCE 08 0702 7 5 FUNCTIONAL LAYOUTS C3G Plus sdlp sdmp sdhp VERSIONS ...
Страница 198: ...Axes Control Circuit MAINTENANCE C3G Plus 7 8 00 1097 FUNCTIONAL LAYOUTS C3G Plus sdlp sdmp sdhp VERSIONS ...
Страница 205: ...Power Supply Distribution Page 1 of 2 C3G Plus MAINTENANCE 01 0498 7 15 FUNCTIONAL LAYOUTS C3G Plus ddmp VERSIONS ...
Страница 206: ...Power Supply Distribution Page 2 of 2 MAINTENANCE C3G Plus 7 16 01 0498 FUNCTIONAL LAYOUTS C3G Plus ddmp VERSIONS ...
Страница 207: ...Machine 1 Axes Control Circuit C3G Plus MAINTENANCE 01 0498 7 17 FUNCTIONAL LAYOUTS C3G Plus ddmp VERSIONS ...
Страница 208: ...Machine 2 Axes Control Circuit MAINTENANCE C3G Plus 7 18 04 0799 FUNCTIONAL LAYOUTS C3G Plus ddmp VERSIONS ...
Страница 209: ...Serial and Parallel Line Connections C3G Plus MAINTENANCE 04 0799 7 19 FUNCTIONAL LAYOUTS C3G Plus ddmp VERSIONS ...
Страница 221: ...SAFETY CIRCUIT TEST DEVICES Connector X113 test device C3G Plus MAINTENANCE 04 0799 7 31 diagnostic C3G Plus ...
Страница 225: ...X30 connector test device C3G Plus MAINTENANCE 01 0498 7 35 diagnostic ...
Страница 232: ...This page has been left intentionally blank MAINTENANCE C3G Plus 7 42 00 1097 CIRCUIT DIAGRAMS ...
Страница 255: ...SOFTWARE OPERATIONS FOR CONTROLLER REPLACEMENT 2 2 C3G Plus MAINTENANCE 01 0498 7 65 SYSTEM SOFTWARE ...
Страница 264: ...This page has been intentionally blank 7 74 08 0702 MAINTENANCE C3G Plus LIST OF SPARE PARTS ...
Страница 265: ...OPERATOR S NOTES C3G Plus NOTES ...
Страница 266: ...C3G Plus NOTES ...