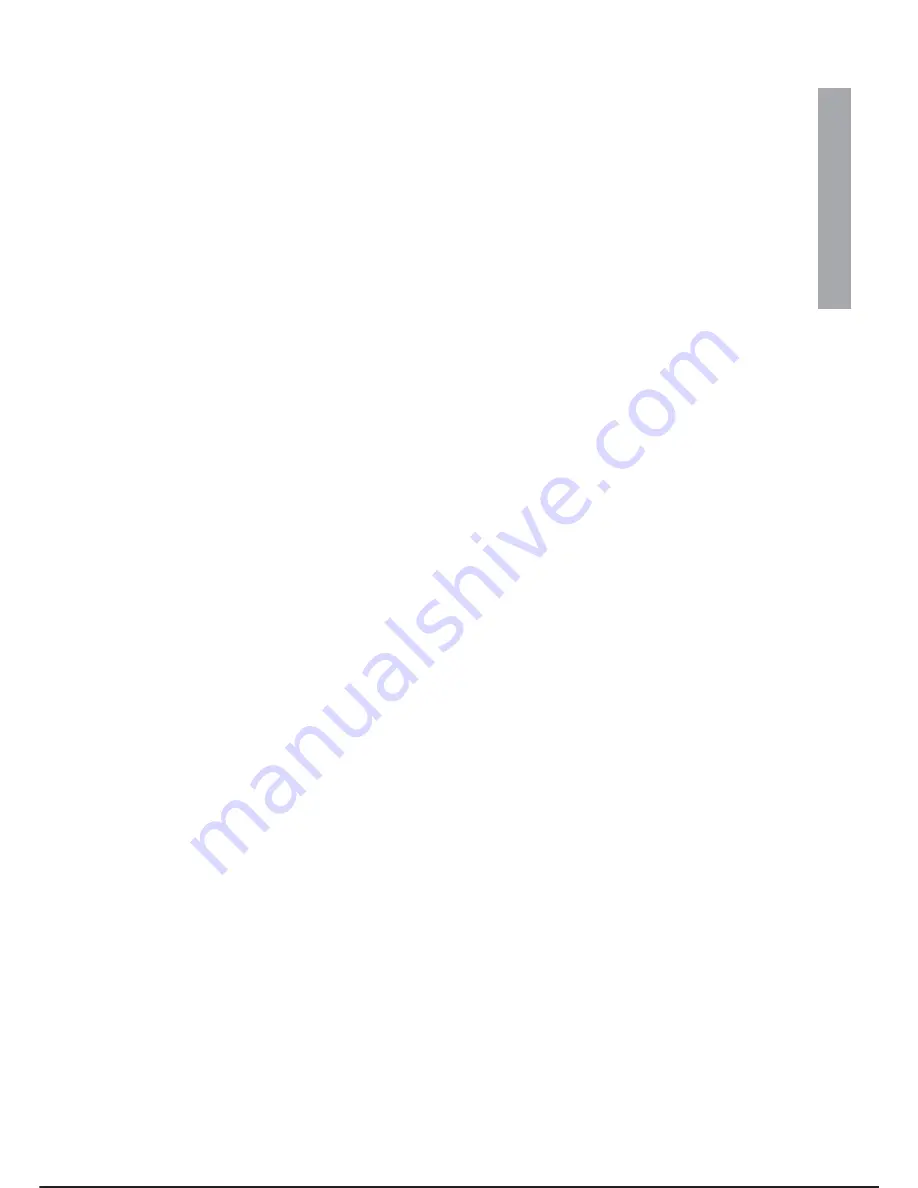
Installation and Commissioning - Continued
4.1.9
When required, connect the robot's pneumatic system to the air distribution network and check
carefully to make sure that the pressure is set correctly. If the pressure of the balancing system is
not correct it will affect the robot's movements.Also install filters to collect any condensate in the
system.
4.1.10
Install the control unit so that the control panel can only be operated from outside the protected
area.
4.1.11
Check that the pre-engineered voltage on the power supply transformers indicated on the specific
rating plate corresponds to the power mains voltage.
4.1.12
Before making the electrical connections to the control unit, make sure that the power mains cir-
cuit breaker is locked in the open position.
4.1.13
The connection between the control unit and the mains circuit breaker must be effected by means
of a shielded quadripole cable (3- ground) of suitable dimensions for the control unit
power installed
4.1.14
The supply cable must enter the control unit through the appropriate raceway and locked cor-
rectly.
4.1.15
After connecting the ground conductor (PE), connect the power conductors of the power cable to
the main circuit breaker or to the terminals on the controller Assemble the protectiive cover on the
main circuit breaker or on the input terminals.
4.1.16
Connect the supply cable to the circuit breaker on the power mains after checking, with the use of
an appropriate instrument, that the circuit breaker terminals are disconnected.
4.1.17
The controller can be provided with an internal lighting circuit and service socket connected down-
stream of the main circuit breaker. Should it be necessary to power the circuits independently
from the main circuit breaker, it will be necessary to alter an internal connection by connecting a
shielded three-core cable (2 ground) to the mains, scaled according to the protection
rating of the mains, in the same way and according to the same sequence of operations as speci-
fied for connection of the power supply.
4.1.18
Connect the earth wire and the signals and power cables between the control unit and the robot.
4.1.19
Check that the control unit door(s) is/are locked with the special key.
4.1.20
The components of the control unit may be permanently damaged if the connectors are con-
nected incorrectly.
4.1.21
The C3G
Plus
internally makes the main safety interlocks (gates, enable button, etc.). Should it be
necessary to connect to the signals provided to make additional external circuits, make sure that
these signals are used according to safety regulations. The safety of interlock signals leading from
the transfer line (emergency stop, gates safety, etc.), i.e. providing correct and safe circuits is the
task of the robot system integrator.
System safety cannot be guaranteed if these interlocks are missing, incomplete or incorrectly es-
tablished.
4.1.22
Stopping due to tripping of the protective barrier safety devices causes uncontrolled stopping of
the robot with possible loss of the trajectory programmed. To stop the robot with controlled
ramping down, it is advisable to connect the interlock signals so as to activate a Drive Off com-
mand before the emergency stop.
Example: opening of the protective barrier safety locks causes Remote Drive Off; opening of the
protective barriers causes an emergency stop..
4.1.23
If the C3G-CSM (Controlled Stop Module) is installed on the controller, in AUTO LOCAL and
AUTO REMOTE states, an emergency stop and/or opening of the safety gates causes controlled
stopping of the robot (EN 60204-1), category 1 stop). In this way, power is cut off (opening of the
power contactor) after 1 second. In PROGR. programming status, the power is cut off immediately
(EN 60204-1, category 0 stop). These times must be taken into account when installing the pro-
tective barriers in particular if light curtains are used.
4.1.24
Check that the environmental and operating conditions do not exceed the limits specified in the
product User Manual.
C3G
Plus
SAFETY REGULATIONS
02/1299
1-3
SAFETY
REGULATIONS
Содержание C3G Plus
Страница 6: ...This page has been intentionally blank UPDATING LIST C3G Plus D 08 0702 ...
Страница 7: ...C3G Plus PREFACE 05 1199 i PREFACE C3G Plus VERSIONS SDLP SDMP SDHP C3G Plus VERSIONS DDMP DDHP ...
Страница 14: ...This page has been intentionally blank Operations and Maintenance Manual C3G Plus ...
Страница 22: ...This page has been intentionally blank SAFETY REGULATIONS C3G Plus 1 8 02 1299 SAFETY REGULATIONS ...
Страница 24: ...This page has been intentionally blank Operations and Maintenance Manual C3G Plus ...
Страница 26: ...This page has been left intentionally blank INSTALLATION C3G Plus 2 ii 01 0498 SUMMARY ...
Страница 48: ...This page has been intentionally blank Operations and Maintenance Manual C3G Plus ...
Страница 61: ...SAMPLE CONNECTION OF C3G EMC2 C3G Plus OPERATOR INTERFACE 07 1200 3 13 EMERGENCY CONTROL C3G EMC2 ...
Страница 120: ...This page has been left intentionally blank OPERATOR INTERFACE C3G Plus 3 72 05 1199 C3G Plus KIT IVECO ...
Страница 122: ...This page has been intentionally blank Operations and Maintenance Manual C3G Plus ...
Страница 127: ...C3G Plus INTEGRATION GUIDE 06 0400 4 5 SYSTEM I O ...
Страница 143: ...Additional I O modules C3G Plus INTEGRATION GUIDE 01 0498 4 21 parallel i o additional modules ...
Страница 158: ...This page has been intentionally blank INTEGRATION GUIDE C3G Plus 4 36 06 0400 SERIAL I O AND PDL2 TOOLS ...
Страница 160: ...This page has been intentionally blank Operations and Maintenance Manual C3G Plus ...
Страница 182: ...This page has been intentionally blank Operations and Maintenance Manual C3G Plus ...
Страница 188: ...This page has been intentionally blank Operations and Maintenance Manual C3G Plus ...
Страница 190: ...This page has been left intentionally blank MAINTENANCE C3G Plus 7 ii 00 1097 GENERAL RULES ...
Страница 192: ...This page has been left intentionally blank MAINTENANCE C3G Plus 7 2 00 1097 PREVENTIVE MAINTENANCE ...
Страница 195: ...Main C3G Plus Connections C3G Plus MAINTENANCE 08 0702 7 5 FUNCTIONAL LAYOUTS C3G Plus sdlp sdmp sdhp VERSIONS ...
Страница 198: ...Axes Control Circuit MAINTENANCE C3G Plus 7 8 00 1097 FUNCTIONAL LAYOUTS C3G Plus sdlp sdmp sdhp VERSIONS ...
Страница 205: ...Power Supply Distribution Page 1 of 2 C3G Plus MAINTENANCE 01 0498 7 15 FUNCTIONAL LAYOUTS C3G Plus ddmp VERSIONS ...
Страница 206: ...Power Supply Distribution Page 2 of 2 MAINTENANCE C3G Plus 7 16 01 0498 FUNCTIONAL LAYOUTS C3G Plus ddmp VERSIONS ...
Страница 207: ...Machine 1 Axes Control Circuit C3G Plus MAINTENANCE 01 0498 7 17 FUNCTIONAL LAYOUTS C3G Plus ddmp VERSIONS ...
Страница 208: ...Machine 2 Axes Control Circuit MAINTENANCE C3G Plus 7 18 04 0799 FUNCTIONAL LAYOUTS C3G Plus ddmp VERSIONS ...
Страница 209: ...Serial and Parallel Line Connections C3G Plus MAINTENANCE 04 0799 7 19 FUNCTIONAL LAYOUTS C3G Plus ddmp VERSIONS ...
Страница 221: ...SAFETY CIRCUIT TEST DEVICES Connector X113 test device C3G Plus MAINTENANCE 04 0799 7 31 diagnostic C3G Plus ...
Страница 225: ...X30 connector test device C3G Plus MAINTENANCE 01 0498 7 35 diagnostic ...
Страница 232: ...This page has been left intentionally blank MAINTENANCE C3G Plus 7 42 00 1097 CIRCUIT DIAGRAMS ...
Страница 255: ...SOFTWARE OPERATIONS FOR CONTROLLER REPLACEMENT 2 2 C3G Plus MAINTENANCE 01 0498 7 65 SYSTEM SOFTWARE ...
Страница 264: ...This page has been intentionally blank 7 74 08 0702 MAINTENANCE C3G Plus LIST OF SPARE PARTS ...
Страница 265: ...OPERATOR S NOTES C3G Plus NOTES ...
Страница 266: ...C3G Plus NOTES ...