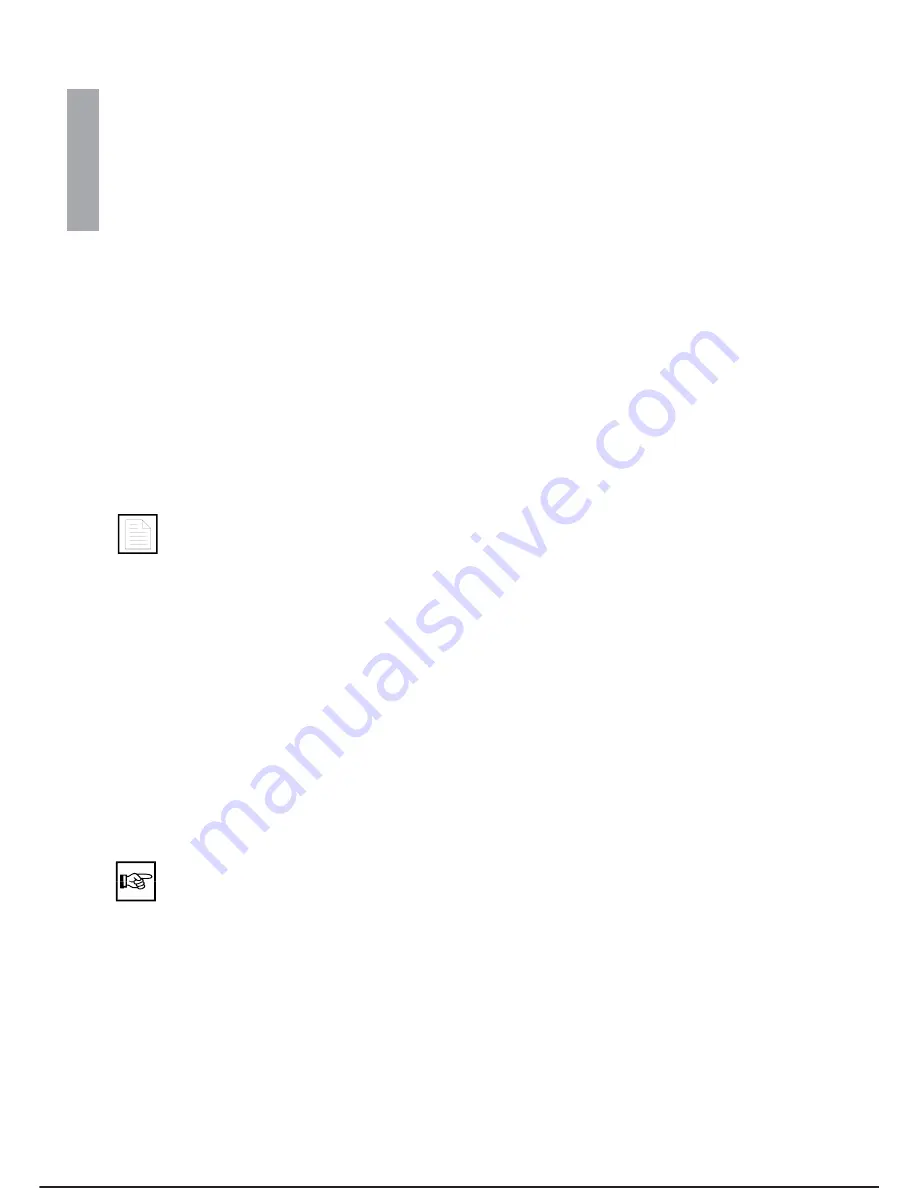
The system calibration procedure consists in moving the robot to a pre-established position checked
with suitable equipment (reference guards, dial gauges, supports, calibration equipment). Once this po-
sition has been reached, proceed as follows:
- fix the reference indexes of all the axes in the case of initial calibration or record the existing ones if
calibration is being performed after replacing a component in the kinematic chain;
- using the programming terminal enter the appropriate calibration command CAC (Configure Arm Cali-
brate) so that the control unit assumes the same axis positional value as the calibration position.
- Enter the Password, unless the command CCP (Configure Controller Password) has already been
sent
Once the indexes are aligned, the Turn-set and recalibration of a robot already installed in the workshop can
be carried out. Calibration performed by positioning each axis on the indexes is not as precise as that per-
formed by mechanical tools: there may be inaccurate positions in the application programmes.
Recovery of calibration, if necessary, (performed by COMAU SYSTEMS) must be carried out when the robot
is started for the first time. Afterwards calibration should not be repeated, unless a component in the
kinematic chain has to be replaced due to a mechanical failure or unless a collision damages the
structure of the robot.
·
USER CALIBRATION: allows the user to define and carry out calibration on a different position than the
system position. This type of calibration can be used when the system position can only be reached with
difficulty after the robot has been inserted in the final application. Calibration precision is the responsibil-
ity of the user who must provide the instruments to check the positioning of the robot for any subsequent
recalibration, in particular as regards the position of the reference indexes.
On some types of robot, calibration notches are used instead of reference indexes.
·
TURN-SET: the Turn-set operation must be performed when the RPT module (optional) and/or the con-
trol unit lose the count of the resolver revolutions; some possible situations in which this count is lost are
described below. The operation consists in moving the axis on the reference indexes and giving the ap-
propriate command.
·
ASCII CALIBRATION FILE: the calibration file CALIB1.TXT is an ASCII file with the syntax of a PDL2 file
inside which the calibration constants ($CAL_DATA[n]) and other typical robot data are stored. The file
name can be changed before performing calibration giving the predefined $CAL_FILE variable to the
name required (for further information refer to the PDL2 Programming Language Manual).
·
FILE C3G.SYS: is a system file in which the current system status regarding the situation of I/O’s, the
predefined variables and other typical controller parameters are stored (for further information refer to
the PDL2 Programming Language Manual).
PROCEDURES
·
CALIBRATION
Refer to the specific robot manuals for robots TRICEPT HP1 and robot SMART H4.
·
In this procedure the operator must move the axis to the calibration position with the aid of special tools.
With the axis in the required position, the drives on (Dr:ON) and the control unit in programming status
(St:PROGR), the operator must invoke the CAC (Configure Arm Calibrate) command: the command
asks for the arm and the axis to be calibrated (* for all the axes).
The command carries out the operations required and also sends the number of resolver revolutions de-
fined to the RPT module.
MAIN OPERATIONS FOR SYSTEM USE
C3G
Plus
5-14
06/0400
CALIBRATION
Содержание C3G Plus
Страница 6: ...This page has been intentionally blank UPDATING LIST C3G Plus D 08 0702 ...
Страница 7: ...C3G Plus PREFACE 05 1199 i PREFACE C3G Plus VERSIONS SDLP SDMP SDHP C3G Plus VERSIONS DDMP DDHP ...
Страница 14: ...This page has been intentionally blank Operations and Maintenance Manual C3G Plus ...
Страница 22: ...This page has been intentionally blank SAFETY REGULATIONS C3G Plus 1 8 02 1299 SAFETY REGULATIONS ...
Страница 24: ...This page has been intentionally blank Operations and Maintenance Manual C3G Plus ...
Страница 26: ...This page has been left intentionally blank INSTALLATION C3G Plus 2 ii 01 0498 SUMMARY ...
Страница 48: ...This page has been intentionally blank Operations and Maintenance Manual C3G Plus ...
Страница 61: ...SAMPLE CONNECTION OF C3G EMC2 C3G Plus OPERATOR INTERFACE 07 1200 3 13 EMERGENCY CONTROL C3G EMC2 ...
Страница 120: ...This page has been left intentionally blank OPERATOR INTERFACE C3G Plus 3 72 05 1199 C3G Plus KIT IVECO ...
Страница 122: ...This page has been intentionally blank Operations and Maintenance Manual C3G Plus ...
Страница 127: ...C3G Plus INTEGRATION GUIDE 06 0400 4 5 SYSTEM I O ...
Страница 143: ...Additional I O modules C3G Plus INTEGRATION GUIDE 01 0498 4 21 parallel i o additional modules ...
Страница 158: ...This page has been intentionally blank INTEGRATION GUIDE C3G Plus 4 36 06 0400 SERIAL I O AND PDL2 TOOLS ...
Страница 160: ...This page has been intentionally blank Operations and Maintenance Manual C3G Plus ...
Страница 182: ...This page has been intentionally blank Operations and Maintenance Manual C3G Plus ...
Страница 188: ...This page has been intentionally blank Operations and Maintenance Manual C3G Plus ...
Страница 190: ...This page has been left intentionally blank MAINTENANCE C3G Plus 7 ii 00 1097 GENERAL RULES ...
Страница 192: ...This page has been left intentionally blank MAINTENANCE C3G Plus 7 2 00 1097 PREVENTIVE MAINTENANCE ...
Страница 195: ...Main C3G Plus Connections C3G Plus MAINTENANCE 08 0702 7 5 FUNCTIONAL LAYOUTS C3G Plus sdlp sdmp sdhp VERSIONS ...
Страница 198: ...Axes Control Circuit MAINTENANCE C3G Plus 7 8 00 1097 FUNCTIONAL LAYOUTS C3G Plus sdlp sdmp sdhp VERSIONS ...
Страница 205: ...Power Supply Distribution Page 1 of 2 C3G Plus MAINTENANCE 01 0498 7 15 FUNCTIONAL LAYOUTS C3G Plus ddmp VERSIONS ...
Страница 206: ...Power Supply Distribution Page 2 of 2 MAINTENANCE C3G Plus 7 16 01 0498 FUNCTIONAL LAYOUTS C3G Plus ddmp VERSIONS ...
Страница 207: ...Machine 1 Axes Control Circuit C3G Plus MAINTENANCE 01 0498 7 17 FUNCTIONAL LAYOUTS C3G Plus ddmp VERSIONS ...
Страница 208: ...Machine 2 Axes Control Circuit MAINTENANCE C3G Plus 7 18 04 0799 FUNCTIONAL LAYOUTS C3G Plus ddmp VERSIONS ...
Страница 209: ...Serial and Parallel Line Connections C3G Plus MAINTENANCE 04 0799 7 19 FUNCTIONAL LAYOUTS C3G Plus ddmp VERSIONS ...
Страница 221: ...SAFETY CIRCUIT TEST DEVICES Connector X113 test device C3G Plus MAINTENANCE 04 0799 7 31 diagnostic C3G Plus ...
Страница 225: ...X30 connector test device C3G Plus MAINTENANCE 01 0498 7 35 diagnostic ...
Страница 232: ...This page has been left intentionally blank MAINTENANCE C3G Plus 7 42 00 1097 CIRCUIT DIAGRAMS ...
Страница 255: ...SOFTWARE OPERATIONS FOR CONTROLLER REPLACEMENT 2 2 C3G Plus MAINTENANCE 01 0498 7 65 SYSTEM SOFTWARE ...
Страница 264: ...This page has been intentionally blank 7 74 08 0702 MAINTENANCE C3G Plus LIST OF SPARE PARTS ...
Страница 265: ...OPERATOR S NOTES C3G Plus NOTES ...
Страница 266: ...C3G Plus NOTES ...