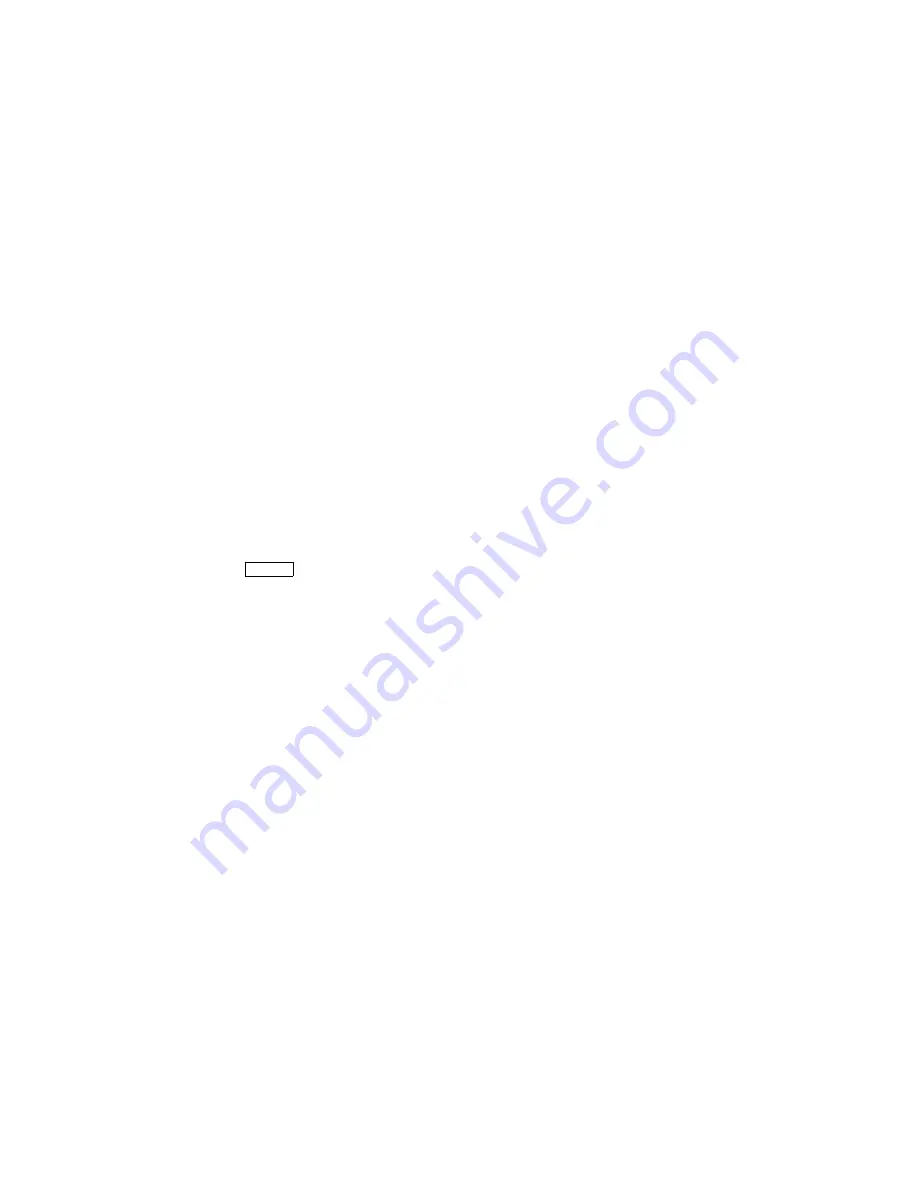
61
capacity, which is defined as 115 –
LAG % CAPACITY
.
The
LAG % CAPACITY
parameter is on the LEADLAG
screen, which is accessed from the EQUIPMENT SER-
VICE table on the SERVICE menu.
2. The lead chiller chilled water temperature is less than the
CONTROL POINT
temperature (see the MAINSTAT
screen) plus
1
/
2
the
CHILLED WATER DEADBAND
tem-
perature (see the SETUP1 screen).
3. The configured
LAG STOP TIMER
entry has elapsed.
The
LAG STOP TIMER
starts when the lead chiller
chilled water temperature is less than the chilled water
CONTROL POINT plus 1/2 of the
CHILLED WATER
DEADBAND
and the lead chiller compressor motor load
(
MOTOR PERCENT KILOWATT
or
AVERAGE LINE
CURRENT
on the MAINSTAT screen) is less than the
lead chiller percent capacity.
NOTE: The use of AVERAGE LINE CURRENT or PER-
CENT MOTOR KILOWATTS in the Lag chiller shutdown
decision is based on the DEMAND LIMIT SOURCE configu-
ration in the RAMP_DEM screen. If DEMAND LIMIT
SOURCE = 0 then AVERAGE LINE CURRENT will be
used. If DEMAND LIMIT SOURCE = 1 then PERCENT
MOTOR KILOWATTS will be used.
FAULTED CHILLER OPERATION — If the lead chiller
shuts down because of an alarm (*) condition, it stops commu-
nicating to the lag and standby chillers. After 30 seconds, the
lag chiller becomes the acting lead chiller and starts and stops
the standby chiller, if necessary.
If the lag chiller goes into alarm when the lead chiller is also
in alarm, the standby chiller reverts to a stand-alone CCN
mode of operation.
If the lead chiller is in an alarm (*) condition (as shown on
the ICVC panel), press the
softkey to clear the alarm.
The chiller is placed in CCN mode. The lead chiller communi-
cates and monitors the RUN STATUS of the lag and standby
chillers. If both the lag and standby chillers are running, the
lead chiller does not attempt to start and does not assume the
role of lead chiller until either the lag or standby chiller shuts
down. If only one chiller is running, the lead chiller waits for a
start request from the operating chiller. When the configured
lead chiller starts, it assumes its role as lead chiller.
If the lag chiller is the only chiller running when the lead
chiller assumes its role as a lead chiller then the lag chiller will
perform a
RECOVERY START REQUEST
(LL_MAINT
screen). The lead chiller will start up when the following condi-
tions are met.
1. Lag chiller ramp loading must be complete.
2. Lag
CHILLED WATER TEMP
(MAINSTAT screen) is
greater than
CONTROL POINT
plus
1
/
2
the
CHILLED
WATER DEADBAND
temperature.
3. Lag chiller
ACTIVE DEMAND LIMIT
value must be
greater than 95% of full load amps.
4. Lag chiller temperature pulldown rate (
TEMP PULL-
DOWN DEG/MIN
) of the chilled water temperature is
less than 0.5 F (0.27 C) per minute.
5. The standby chiller is not running as a lag chiller.
6. The configured
LAG START TIMER
configured in the lag
(acting lead) chiller has elapsed. The
LAG START TIMER
is started when the lag (acting lead) chiller’s ramp loading
is completed.
LOAD BALANCING — When the
LOAD BALANCE OP-
TION
(see LEADLAG screen) is enabled, the lead chiller sets
the
ACTIVE DEMAND LIMIT
in the lag chiller to the lead
chiller’s compressor motor load value
MOTOR PERCENT
KILOWATTS
or
AVERAGE LINE CURRENT
on the MAIN-
STAT screen). This value has limits of 40% to 100%. In
addition, the
CONTROL POINT
for the lag chiller will be mod-
ified to a value of 3
F (1.67
C) less than the lead chiller’s
CONTROL POINT
value. If the
LOAD BALANCE OPTION
is
disabled, the
ACTIVE DEMAND LIMIT
and the
CONTROL
POINT
are both forced to the same value as the lead chiller.
AUTO. RESTART AFTER POWER FAILURE — When
an auto. restart condition occurs, each chiller may have a delay
added to the start-up sequence, depending on its lead/lag con-
figuration. The lead chiller does not have a delay. The lag
chiller has a 45-second delay. The standby chiller has a 90-sec-
ond delay. The delay time is added after the chiller water flow
is verified. The PIC II ensures the guide vanes are closed. After
the guide vane position is confirmed, the delay for lag and
standby chillers occurs prior to energizing the oil pump. The
normal start-up sequence then continues. The auto. restart
delay sequence occurs whether the chiller is in CCN or LO-
CAL mode and is intended to stagger the compressor motor
starts. Preventing the motors from starting simultaneously
helps reduce the inrush demands on the building power system.
Ice Build Control —
The selectable ice build mode per-
mits use of the chiller to refreeze or control the temperature of
an ice reservoir which may, for example, be used for thermal
storage. This mode differs from water or brine chilling in that
termination (indication that the need for cooling has been satis-
fied) is based on input(s) other than the temperature which is
being controlled during operation.
NOTE: For ice build control to operate properly, the PIC II
must be in CCN mode.
The PIC II can be configured for ice build operation.
• From the SERVICE menu, access the EQUIPMENT
SERVICE table. From there, select the OPTIONS screen
to enable or disable the
ICE BUILD OPTION
. See
Table 3, Example 18.
• The
ICE BUILD SETPOINT
can be configured from the
SETPOINT display, which is accessed from the PIC II
main menu. See Table 3, Example 9.
• The ice build schedule can be viewed or modified from
the SCHEDULE table. From this table, select the ice
build schedule (OCCPC02S) screen. See Fig. 22 and the
section on Time Schedule Operation, page 27, for more
information on modifying chiller schedules.
The ice build time schedule defines the period(s) during
which ice build is active if the ice build option is enabled. If the
ice build time schedule overlaps other schedules, the ice build
time schedule takes priority. During the ice build period, the
CONTROL POINT
is set to the
ICE BUILD SETPOINT
for
temperature control. The
ICE BUILD RECYCLE
and
ICE
BUILD TERMINATION
parameters, accessed from the OP-
TIONS screen, allow the chiller operator to recycle or termi-
nate the ice build cycle. The ice build cycle can be configured
to terminate when:
• the
ENTERING CHILLED WATER
temperature is less
than the
ICE BUILD SETPOINT
. In this case, the opera-
tor sets the
ICE BUILD TERMINATION
parameter to 0
on the OPTIONS screen.
• the REMOTE CONTACT inputs from an ice level indi-
cator are opened. In this case, the operator sets the
ICE
BUILD TERMINATION
parameter to 1 on the OPTIONS
screen.
• the chilled water temperature is less than the ice build set
point and the remote contact inputs from an ice level
indicator are open. In this case, the operator sets the
ICE
BUILD TERMINATION
parameter to 2 on the OPTIONS
screen.
• the end of the ice build time schedule (OCCP02S) has
been reached.
RESET
Содержание AquaEdge 19XR series
Страница 69: ...69 Fig 33 19XR Leak Test Procedures a19 1625 ...
Страница 150: ...150 Fig 62 PIC II Control Panel Wiring Schematic Frame 2 3 4 and E Compressors without Split Ring Diffuser a19 1870 ...
Страница 152: ...152 a19 1871 Fig 63 PIC II Control Panel Wiring Schematic Frame 4 and 5 Compressors with Split Ring Diffuser ...
Страница 154: ...154 Fig 64 Benshaw Inc Wye Delta Unit Mounted Starter Wiring Schematic Low Voltage a19 1873 ...
Страница 161: ...161 Fig 69 Typical Low Voltage Variable Frequency Drive VFD Wiring Schematic 575 v ...
Страница 162: ...162 Fig 69 Typical Low Voltage Variable Frequency Drive VFD Wiring Schematic 575 v cont ...
Страница 163: ...163 Fig 69 Typical Low Voltage Variable Frequency Drive VFD Wiring Schematic 575 v cont a19 1880 ...
Страница 176: ...176 CONTINUED ON NEXT PAGE Fig 71 Typical Medium Voltage Variable Frequency Drive VFD Wiring Schematic cont a19 2064 ...
Страница 186: ...186 APPENDIX B LEAD LAG WIRING 19XR Lead Lag Schematic Series Cooler Flow a19 1655 ...
Страница 187: ...187 APPENDIX B LEAD LAG WIRING cont 19XR Lead Lag Schematic Parallel Cooler Flow a19 1717 ...